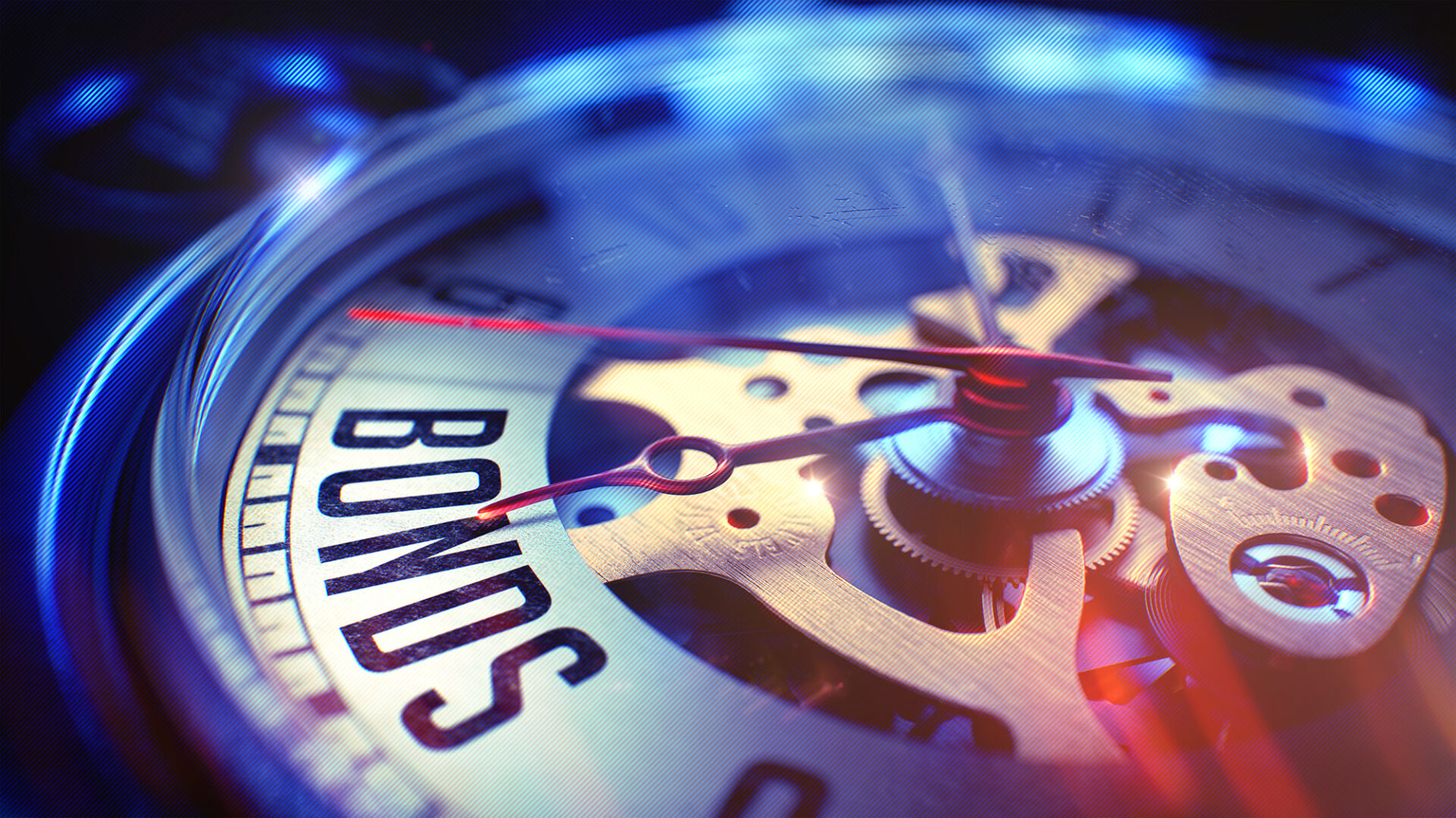
- 接合関連
熱硬化型接着剤の5つの課題とそのソリューション
熱硬化型接着剤の5つの改良ニーズ
電子部品の接着に幅広く使用されている熱硬化型接着剤ですが、その特性にはいくつか改良が望まれる点がありました。その代表的な改善点を5つご紹介します。
- 低温硬化
120℃〜180℃ぐらいの温度で硬化する熱硬化型接着剤が多く、そのため耐熱性が低い被着体への適用が困難となっている。耐熱性の高いプラスチック材料はコスト的に高いこと、光学系の部品は熱によるわずかな歪みも許されないこと、製品小型化のニーズ(被着体は薄く小さくなるほど耐熱性が下がる)などの理由から、熱硬化型接着剤にも60℃〜80℃の低温硬化の需要が高まっている。
- 速硬化
UV硬化型接着剤のような秒単位での固定ができない。
硬化に30分〜数時間を要する製品も多く、生産性向上のネックになることがある。
- アウトガスの削減
硬化時あるいは硬化後に熱硬化型接着剤中の低分子成分がガス化し、デバイスや作業環境を汚染する可能性がある。
- 固定精度の改善
硬化に時間がかかるため、固まるまで被着体を精度高く保持する必要がある。
- さらなる高信頼性
電子デバイスの機能向上、小型化にともない、接着剤にもさらなる高信頼性が求められるようになっている。
こうした改良ニーズに応えるべく、デクセリアルズでは今までになかった熱硬化型接着剤の開発に取り組んでいます。
改良ニーズに対する対応
先に記した改良ニーズは最近になって急に現れたものではなく、現在に至るまで継続して望まれている開発テーマです。もちろん数値的な目標や狙いは、技術の進歩や時代のニーズに合わせてアップデートをされています。ここでポイントとなるのは、他の特性を犠牲にすることなく改良ニーズに応えなければならない点です。改良ニーズには必ずトレードオフとなる特性があります。そのため、熱硬化型接着剤の改良に当たってはこの両者を満足する解決策を見出す必要があります。
ここでは、具体的なデクセリアルズの解決策を紹介する前に、これまでの対応について触れておきたいと思います。
接着剤の「低温硬化」と「速硬化」は、ニーズそのものがトレードオフの関係にあると言えます。一般には、硬化温度を上げると硬化時間を短くすることができ、逆に硬化温度を下げると硬化時間は長くなります。ただ、いたずらに「硬化温度が下がれば良い」「硬化時間が短ければ良い」というわけではなく、用途に合わせて硬化温度や硬化時間を設計する必要があります。
その意味で、接着剤には「都合の良いタイミング(温度や時間)」で固まって欲しいのです。
低温硬化と速硬化を両立するためには「化学的な反応性を高め、低刺激(小さいエネルギー)で硬化できるように接着剤を設計する」というのが基本的な考え方になります。ただし、ちょっと触っただけで直ぐ固まってしまうのも困りものです。そのため熱硬化接着剤の中には、不意の硬化を防ぐために接着剤の主剤と硬化剤を分けた2液タイプが存在します。
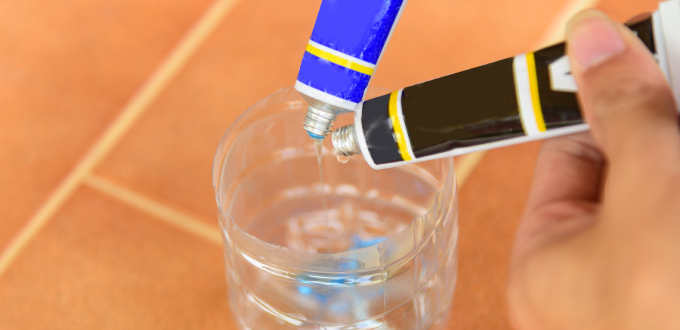
2液タイプは、2つの液剤を混ぜなければ一切反応が起こりません。この特性から2液タイプは、低刺激で接着する特性を持ちつつ、長期間の保管が可能となっており、低温硬化や速硬化の解決策として常温に近い環境下で用いられる「低温硬化型」接着剤や、寒冷地向けの塗料など多くの場所に採用されています。
反面、2液タイプでは安定した性能を出すために2つの液剤を精確な配合比で均一に混ぜ合わせる必要があります。モバイル機器など高い精度が求められる機器では、2液のわずかな配合比のズレや混合状態の不均一さが接着品質のバラツキとなり、改善点として挙げた「固定精度の向上」「さらなる高信頼性」が犠牲になりかねません。そのため、お客さまの使用現場においても正確かつ迅速なオペレーションが求められることになります。
熱硬化型接着剤の新しい取り組み
精密機器の接着では2液タイプよりも1液タイプの接着剤のほうが好まれいてます。これは1液タイプはそれ単体で硬化させますので、2液タイプのような配合・混合によるバラツキや、液剤の成分が不均一になるといった懸念はなく、安定した接着固定ができるためです。デメリットとして、1液タイプはわずかな熱を加えるだけで反応が始まるという特性から、製品によっては室温で放置するだけで固まり始めてしまうものもあります。それゆえ1液タイプの多くは冷凍庫での保管が基本となります。使用前に数十分〜1時間程室温放置し、容器内の接着剤を解凍します。解凍後の接着剤は、ディスペンサーと呼ばれる精密吐出装置により、規定量を精確に吐出させて使われます。
デクセリアルズでは材料としての精度、簡便性、生産性向上の観点から、1液タイプの熱硬化型接着剤の開発に力を入れています。
ここからはデクセリアルズが開発に成功した、これまでの熱硬化型接着剤の課題を克服した製品について解説します。
潜在性重合開始剤を使ったエポキシ−カチオン重合系熱硬化型接着剤
当社の熱硬化型接着剤の開発のなかでも、近年のイノベーティブな成功例が「エポキシ−カチオン系」の熱硬化接着剤にカプセル型重合開始剤を組み合わせた製品です。
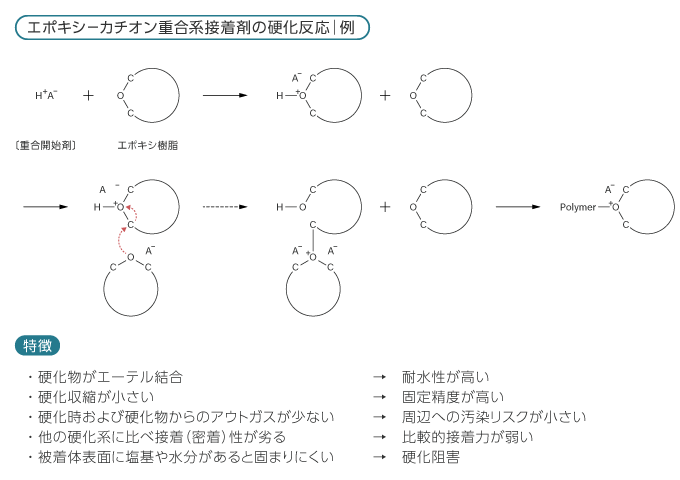
エポキシ−カチオン系接着剤は、硬化物を構成する主要部がエーテル結合で構成されるため、耐水性が高く硬化収縮が小さい、さらに硬化時に出るアウトガスが少ないという、冒頭に示した改良点の2つの解決策になり得る特徴を持っています。一方で硬化反応が遅く、重合開始剤に起因する課題があるなどデメリットもあり、精密部品の固定用接着剤としてほとんど選択肢に入ってこない存在でした。
私たちは、エポキシーカチオン系熱硬化型接着剤の持つ「低硬化収縮」が今後の精密接着の分野で大きなメリットとなり、新たな用途の開発ができるのではと考え、この反応系の改良に取り組みました。従来、この反応系の重合開始剤には劇物であるアンチモン(Sb)を含むものが使われることが多く、この接着剤を敬遠する一因になっていたため、最初に重合開始剤の改良に取りかかりました。新しい重合開始剤には低温硬化速硬化の実現はもちろん、劇物やハロゲンを含まない材料で構成することを目標として開発に取り組み、最終的に現在の開始剤にたどり着きました。ただ、この新しい開始剤は、低温硬化と速硬化は期待できたのですが、液剤中に入れると即座に硬化反応が始まるほど活性が高く、都合の良いタイミングまで待ってくれないものでした。接着品質や生産現場での使い勝手を考えると1液化は必須であり、1液化するためには意図するタイミングまで活性を隠す何らかの工夫「潜在化」が必要でした。
新しい重合開始剤としての潜在性を付与する方法として考案したのが、独自製法のカプセルポリマーに開始剤を閉じ込めることでした。カプセルは特殊なポリマーでできており、ある温度を超えるとカプセルが壊れ、中の開始剤と外部の液剤が触れて反応が始まります。一定の温度を超えない限り、開始剤はカプセル内に留まっていますので、硬化反応は起こりません。この「潜在性熱硬化用重合開始剤」の開発により1液化に成功、熱硬化型接着剤の分野でも、エポキシーカチオン系の持つ「低硬化収縮」のメリットが享受できるようになったのです。
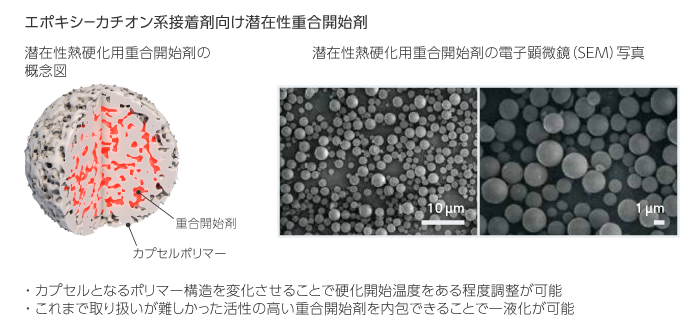
デクセリアルズでは、活性の高い材料をカプセルに内包する技術、反応を制御するカプセルポリマーの技術を進化させることで、この潜在化技術のさらなる応用を検討しています。また、主剤となる樹脂についても改良を重ねています。低温硬化、速硬化性、イオン不純物やアウトガスの低減など新規カチオン重合系の熱硬化型接着剤は、お客さまの多用なニーズに応えることが可能です。私たちデクセリアルズは今後ともこの分野に力を入れ、その普及に取り組んでいきます。
※当社では潜在性硬化剤を使った熱硬化型接着剤の製造・販売をしておりますが、潜在性硬化剤の外販は行っておりませんので、予めご了承ください。
関連記事
- SHARE
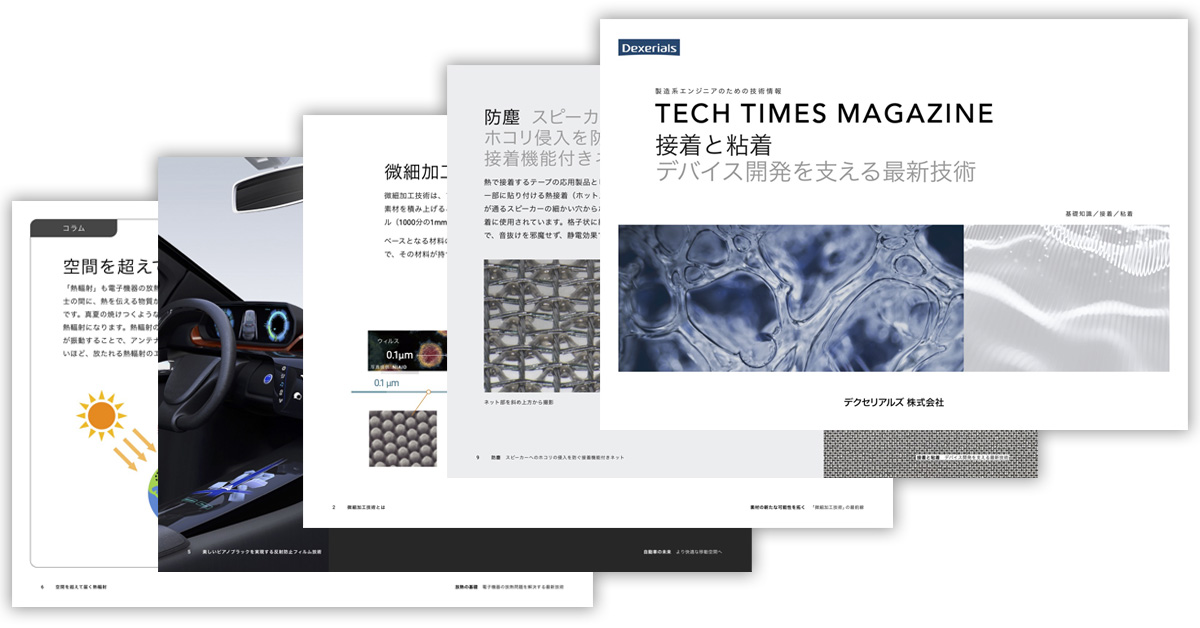
当社の製品や製造技術に関する資料をご用意しています。
無料でお気軽にダウンロードいただけます。
お役立ち資料のダウンロードはこちら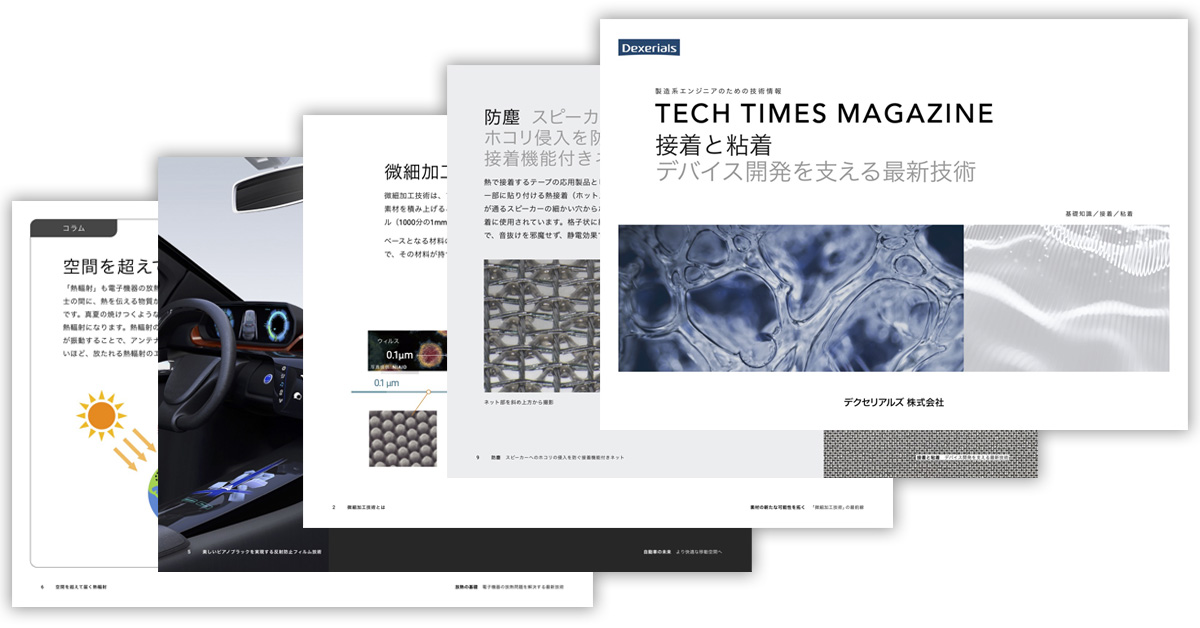
当社の製品や製造技術に関する資料をご用意しています。
無料でお気軽にダウンロードいただけます。
お役立ち資料のダウンロードはこちら