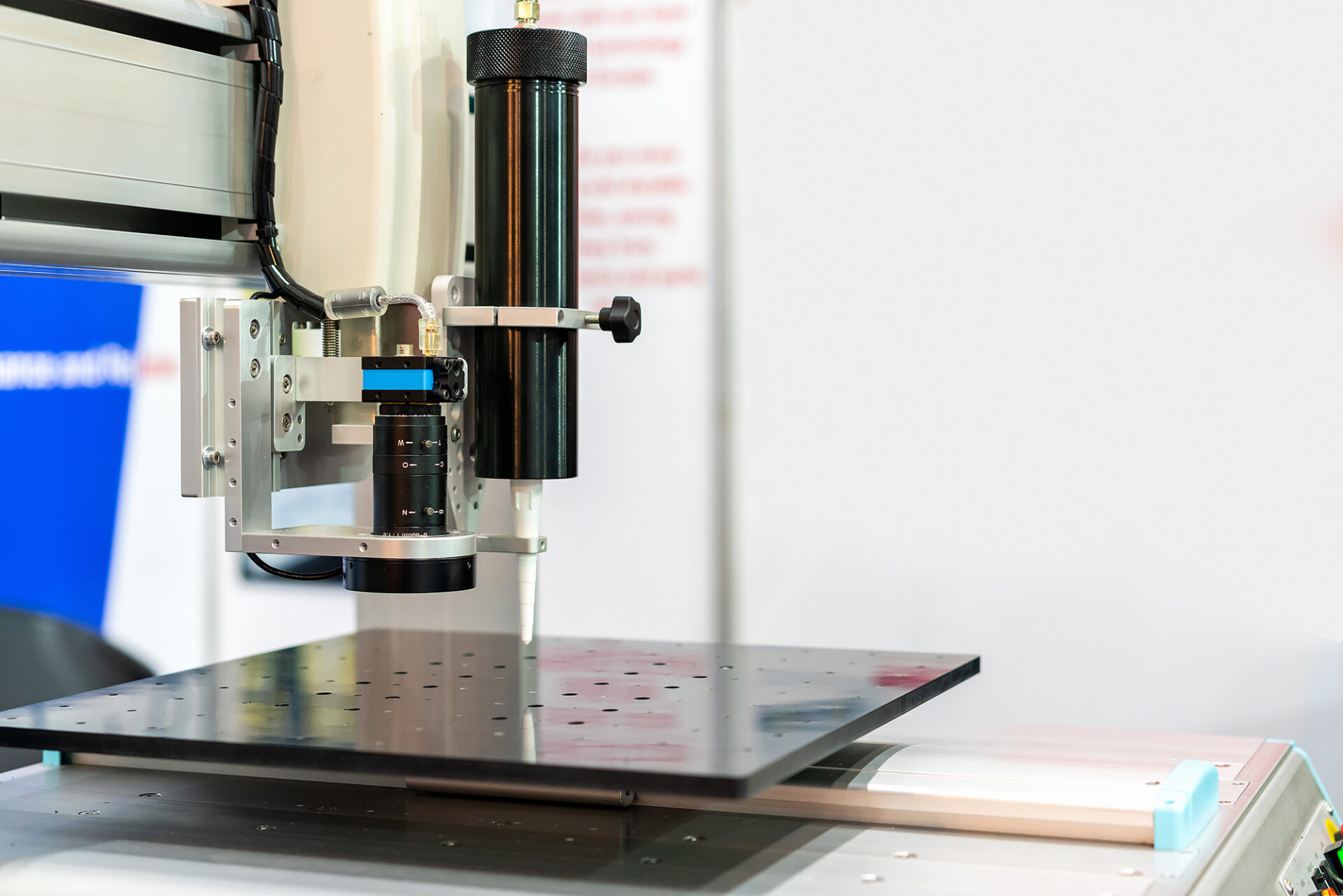
- 接合関連
工業用接着剤の使用方法
目次
正しい位置への固定 〜塗布の位置とバランス〜
最初に検討すべきは、どの位置でどのように固定するかになります。
レンズのようなわずかなズレも許されない高精度部品の固定を行うときには、接着剤をバランスの良い位置に塗布することが重要です。下図はレンズを4箇所の接着ポイントで固定することを想定した図となります。左側は、塗布位置が部品の中心に対して点対称に配置されバランスが取れていますが、右側のように部品中心と接着中心が異なる場合、硬化時の収縮や熱による膨張などによって部品の位置がずれてしまう懸念があります。
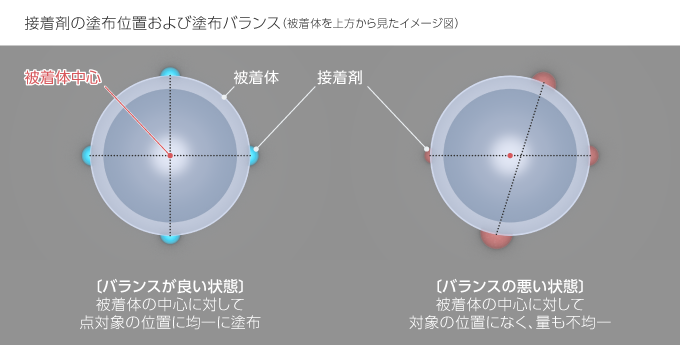
図のように塗布量が不均一だった場合、やはり収縮・熱膨張によって固定精度の悪化を招きかねません。塗布の位置だけでなく、塗布量についてもバランスを考えて同じにすることも重要です。
固定精度を高める工夫 〜塗布量のコントロール〜
物体を固定する力は、接着剤の塗布量(塗布面積)が多ければ多いほど強まります。
一方、接着時の固定精度は接着剤の使用量増加につれて下がる傾向にあります。
液状の接着剤は硬化反応の過程で中心に向かって体積収縮します。その際、樹脂の内部には中心に向かう「応力」が発生し、結果的に被着体を引っ張る形になります。引っ張る力は接着剤の使用量に比例するため、使用量が多いと引っ張る力が大きくなり、結果として被着体が正しい位置からずれることになります。また、この力は接着剤の周縁部で最大となり、被着体によっては歪みや湾曲などの変形をともなうため、正しい固定を妨げることにもつながります。
また、電子部品の固定では、機器使用時の精度が最も重要になります。そのため、接着剤が硬化した後の「膨張・収縮」についても考えておく必要があります。電子機器を構成する部品のなかでも、接着剤は比較的、熱膨張が大きい材料です。そのため、接着剤の塗布量が多くなると、温度上昇・下降時の膨張・収縮が大きく、その分部品が動きやすくなり、部品の固定精度が低下してしまうのです。
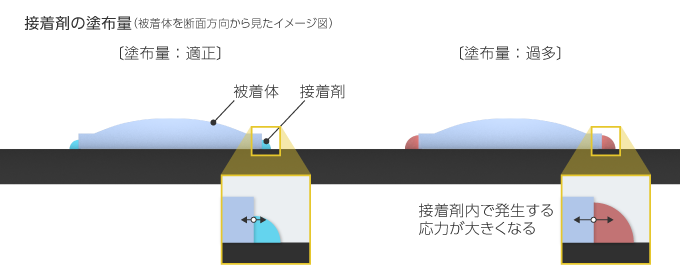
しっかり固定しようと思うと接着剤を多めに使いたくなりますが、高い固定精度を得るためには接着剤の塗布量を目標となる強度が維持できる最小量にすることがベストと言えます。もちろん、接着剤を選定する際に、被着体との線膨張率を加味して検討することも大切となります。
固定性能を左右する硬化
接着剤は適正な硬化プロセスを経て「接着剤全体が均一に硬化する」ことで最大性能が発揮できるよう設計されています。特に紫外線硬化型接着剤は、熱硬化型など他の接着剤に比べて比較的短時間で硬化する、またその目的のために光である「紫外線」を硬化に利用しています。この特徴ゆえに留意しなければならないポイントがいくつかあります。
ポイント(1) 〜紫外線硬化型接着剤は紫外線の「照度」に注意〜
紫外線を照射することで硬化する紫外線硬化接着剤を使用するときは、紫外線の「照度」に気をつける必要があります。照度が高いと硬化反応が早く進むのですが、高すぎると接着剤表層が急速に硬化してしまい内部・深部に紫外線が届きににくくなります。結果として、十分に硬化できない部分が残るなど硬化状態にムラが発生してしまうことがあります。早く固めたい気持ちから、照度高めで作業を行いがちですが、硬化ムラは固定の安定性を損ね、固定精度の低下を招くと同時にその他の機能低下にもつながります。接着剤の性能を十分に発揮させるためにも、接着剤全体が均一に硬化できるように適切な照度でゆるやかに硬化させるのが理想です。
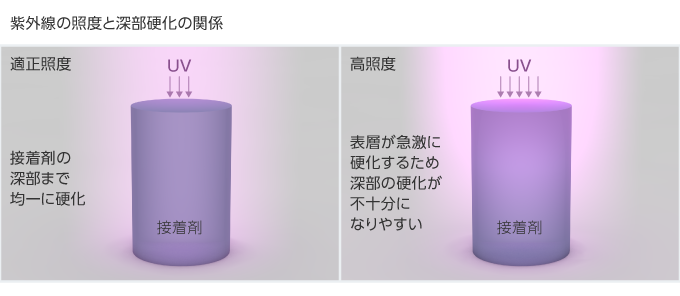
ポイント(2) 〜アクリル系紫外線硬化型接着剤は「低照度」に注意〜
紫外線硬化型接着剤の中でもアクリル系の接着剤は、逆に照度が弱いと酸素による硬化阻害という別のトラブルが起きやすくなります。アクリル系接着剤は硬化反応にラジカル重合を利用し、重合開始剤にはラジカルを発生しやすい物質が選ばれます。このラジカルですが活性が高く、空気中の酸素とも結合しやすい性質を持っています。紫外線の照度が低い場合、接着剤の表層近くのラジカルが重合開始前に周辺の酸素にトラップされてしまう「酸素阻害」が発生します。その結果、接着剤の表層での硬化が甘く(硬化度が不十分に)なりベタベタするようになります。また硬化度が低いと接着剤中の低分子量の成分がガス化してしまうことがあります。ガス化によって発生したガスは周囲の部品を汚染し、予期せぬトラブルの原因となります。そのため、アクリル系の紫外線硬化型接着剤は、適正な照度の紫外線を当てる必要があります。
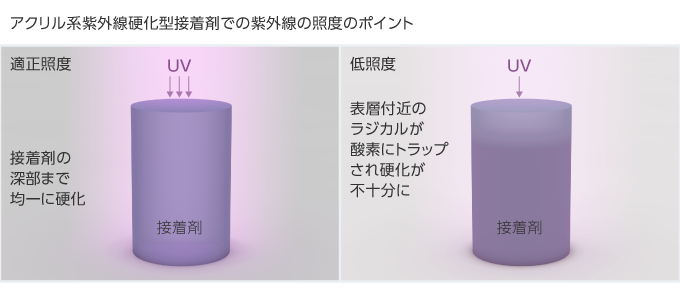
ポイント(3) 〜紫外線の照射方向〜
紫外線硬化型接着剤の性能を引き出すためには、接着剤全体に紫外線を届ける必要があります。しかしながら、接着剤は2つあるいはそれ以上の被着体を固定するために被着体と被着体の間に位置することが多く、状況によっては接着剤全体に光を届けることが難しい場合も少なくありません。
光はその性質上真っ直ぐにしか進まないため、影になる部分は硬化できません。均一に硬化させるためにも、接着剤全体に十分な紫外線が当たるような照射方向を見つけることが大切です。
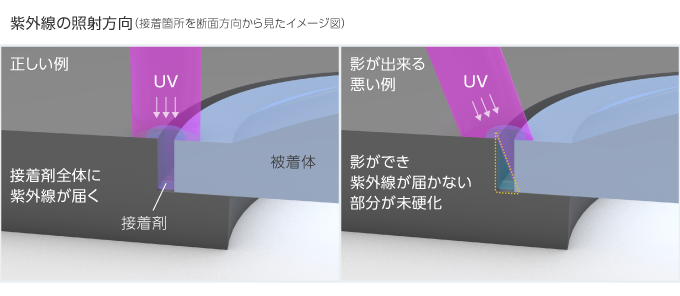
ポイント(4) 〜被着体の光線透過〜
紫外線硬化型接着剤を使用する場合、特に材料越しに紫外線をあてて接着剤を固定させる場合、材料の光線透過率にも注意を払う必要があります。硬化に使用する紫外線の波長によって状況は変わりますが、最近よく使われる紫外線LEDだと中心波長365nmあたりの紫外線を使うことになります。下記のグラフは、ガラス(緑線)とPMMAという透明なアクリル板(ピンク線)の光の波長に対する光線透過率を示したものになります。ガラスは波長が300nmを超えたあたりから光を透過しますが、アクリル板は370nmぐらいの波長にならないと光を透過しません。そのため中心波長365nmの紫外線LEDを光源とした場合、ガラスは透過できても、PMMAはほとんど透過しないため接着剤を素早く硬化することができません。この例の場合、使用する紫外線の波長を長波長側にずらすか、ポイント(3)で記した照射方向を工夫することになります。硬化に使用する波長をずらす場合は、接着剤側もこれに対応した接着剤を選ぶことになります。
また材料の光線透過率は、表面処理があるかどうかによっても大きく変わります。材料越しに紫外線をあてて硬化したい場合は、実際に使用する材料の光線透過率を事前に確認したうえで、照射条件を決定すると良いでしょう。
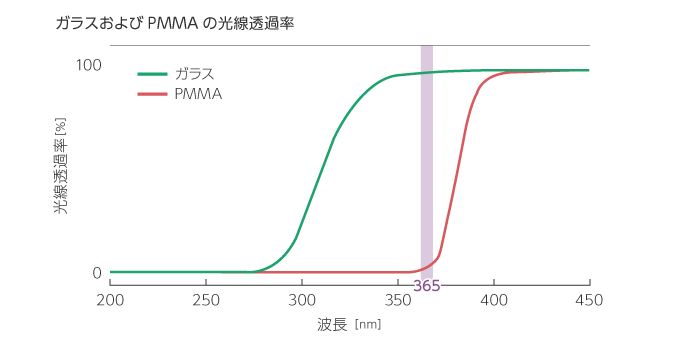
ここで挙げた課題に関して、この記事では使用方法(硬化プロセス)にスポットを当てて記していますが、接着剤側からのアプローチも考えられます。デクセリアルズでは、用途に合った様々な接着剤を用意しているほか、使用方法に関するご提案などをさせて頂いています。ぜひお問い合わせください。
関連記事
- SHARE
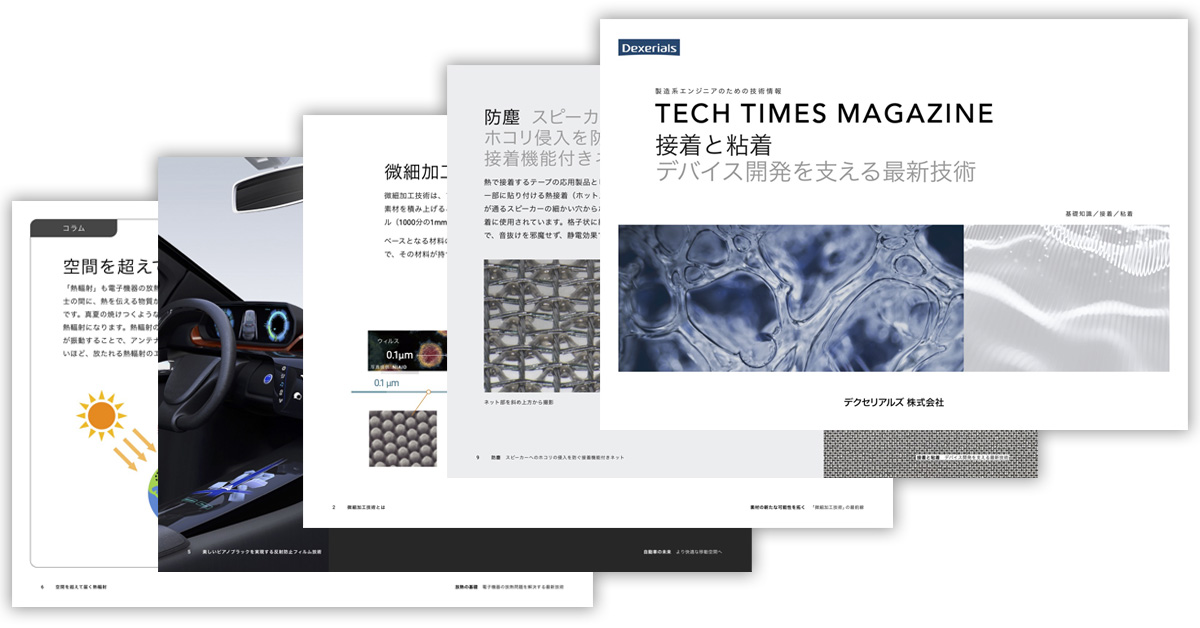
当社の製品や製造技術に関する資料をご用意しています。
無料でお気軽にダウンロードいただけます。
お役立ち資料のダウンロードはこちら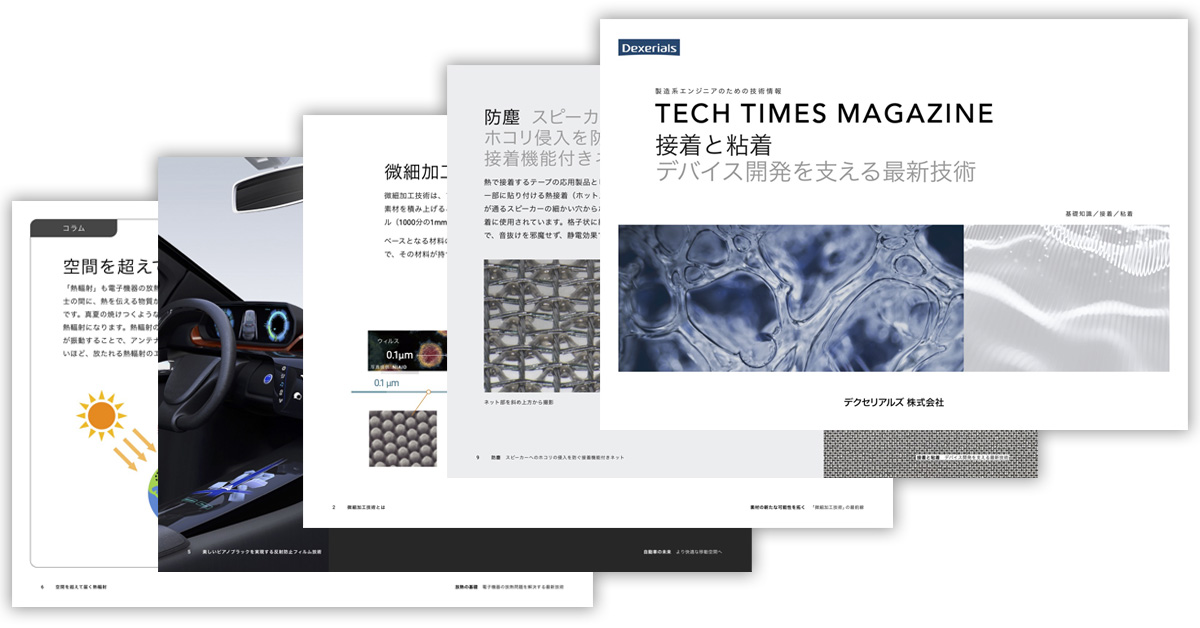
当社の製品や製造技術に関する資料をご用意しています。
無料でお気軽にダウンロードいただけます。
お役立ち資料のダウンロードはこちら