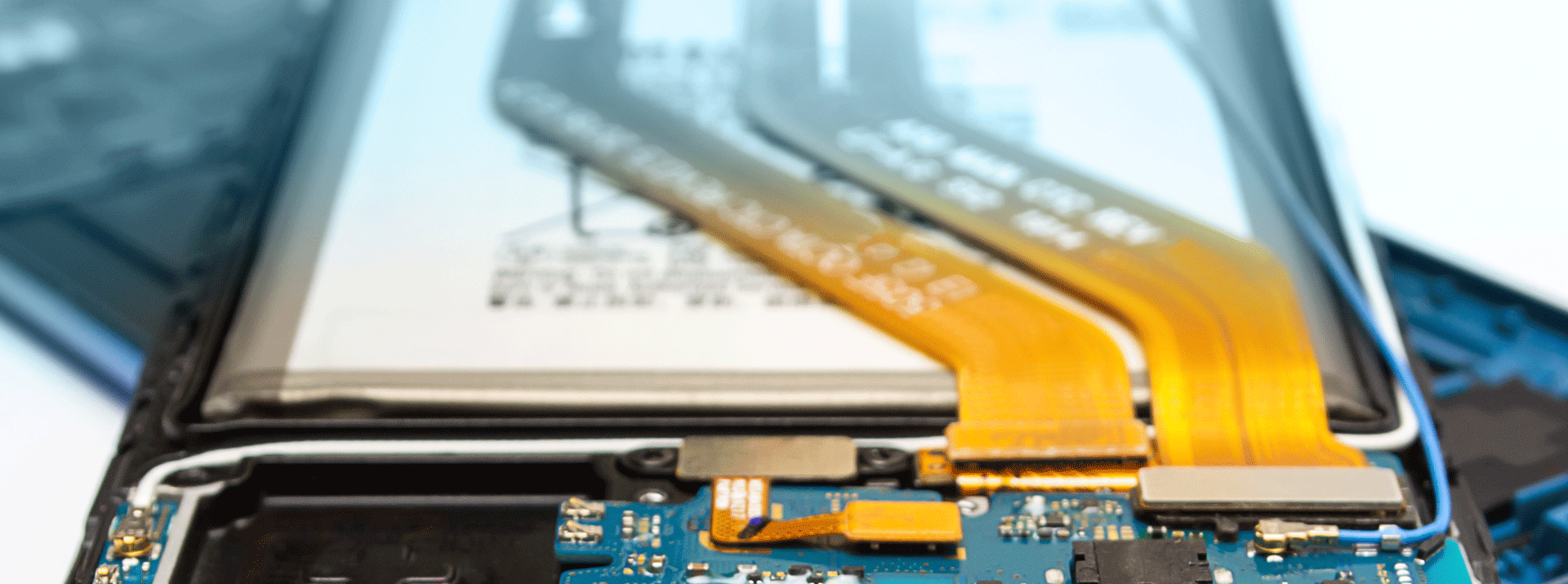
- 接合関連
フレキシブル基板(FPC)の基礎知識とその製造技術
目次
フレキシブル基板(FPC)とは何か
私たちが日常的に使っているデジタル機器に、いまや欠かせない部品となっているのが、フレキシブルプリント配線板とも呼ばれるフレキシブル基板(FPC)です。FPCはスマートフォン、タブレットPC、ノートパソコン、ウェアラブルデバイス、プリンター、デジタルカメラ、医療機器、自動車の電子回路などに数多く使われています。携帯電話がスマートフォンへと進化し、市場が急拡大したのに歩調を合わせ、FPCの市場も大きく成長してきました。またFPCはその特長によって、スマートフォンやタブレットPCの小型化・薄型化にも貢献しています。
本記事ではそうしたFPCについての基礎知識と製造技術を解説するとともに、FPCに貢献するデクセリアルズの材料を紹介します。
従来、電子回路基板によく使われている固く曲がらない「リジッド基板」と呼ばれる基板とは異なり、FPCはポリイミドなどの薄いプラスチックフィルムの上に回路を形成することで、薄く、軽く、折り曲げられるという特長を持ったプリント基板です。
プリント基板は、部品への電力供給や部品間の電気信号の通り道となる導体パターンを持つ「配線板」を指す場合と、その配線板上にICなどの部品を実装し、電気的機能を持たせた「回路基板」を指す場合があります。さらに、複数の回路基板を電気的に接続して、機能の単位でまとまったものを「モジュール」と言います。モジュールには代表的なもとして「カメラモジュール」や「ディスプレイモジュール」などがあり、FPCは現在、この回路基板とモジュール双方を構成する部品として欠かせない部品となっています。
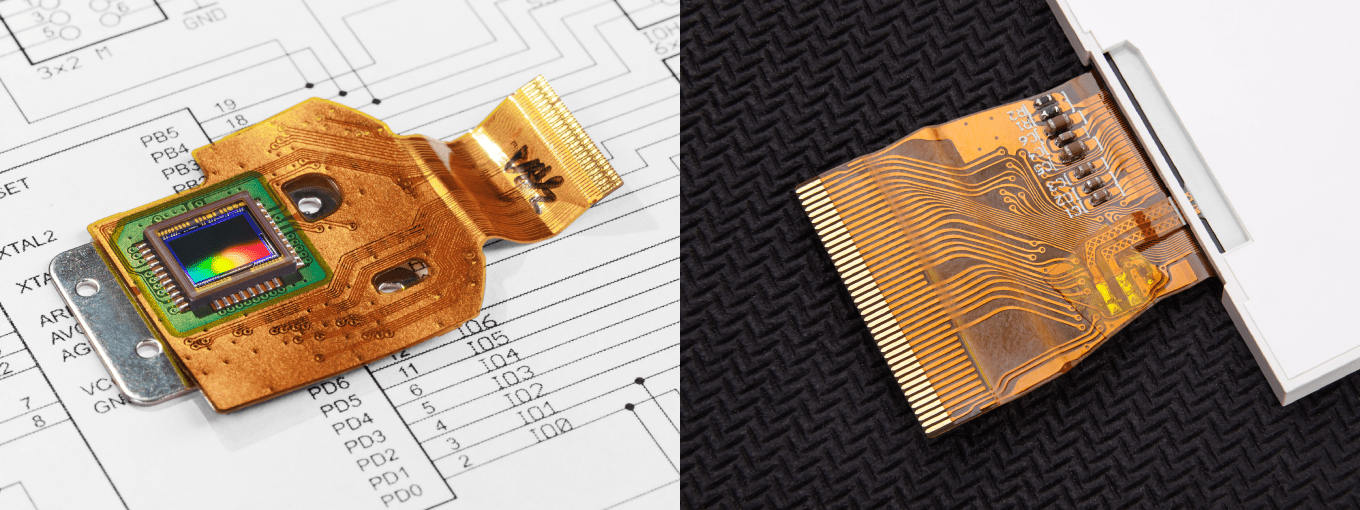
小型化・薄型化・軽量化に貢献
現在、FPCはその軽くて薄いという特長から、とくにスマートフォン用のモジュールに数多く採用されています。ディスプレイモジュールやタッチパネルモジュール、カメラモジュールやLiDARモジュール、バッテリーモジュールやアンテナモジュールなどに使われており、1つの機種で10個以上のFPCを採用したモジュールが使われることも珍しくありません。
また、自動車の分野でも電装化の進展に合わせてFPCの採用が進んでおり、今後さらに増えていくと予測されています。現在、主に使われている箇所としては、カーナビゲーションシステム、ヘッドライト、スイッチ、タイヤ空気圧センサーなどがあります。
FPCを使う大きなメリットの一つが、配線板(配線材)としての機能にあります。配線や接続作業を大幅に簡略化・簡素化できることで、配線の検査や修理にかかる時間が短縮されます。また、FPCは厚みが数十〜数百µmと薄いため、最終製品のダウンサイジングにも大きく貢献できます。最終製品の筐体内でのスペースの有効活用、体積あたりの軽量化にもつながっています。
FPCの構成材料
ここからは、片面FPCと両面FPCについてとその素材、製造工程について解説します。片面FPCは、ポリイミドフィルムの片面に銅の配線パターンを持つ標準的なFPCです。薄く、柔軟性が高く、スペース活用に利点があることから配線基板として利用されることが多く、システム全体の軽量化に貢献できます。また、FPC自体に直接部品を実装し、回路基板として利用することもできます。
両面FPCはポリイミドフィルムの両面に銅の配線パターンを持つFPCです。片面FPCと比べて、より複雑な回路を可能にします。また、FPCの両面に部品を実装できるため、さらなる省スペース化を実現できます。
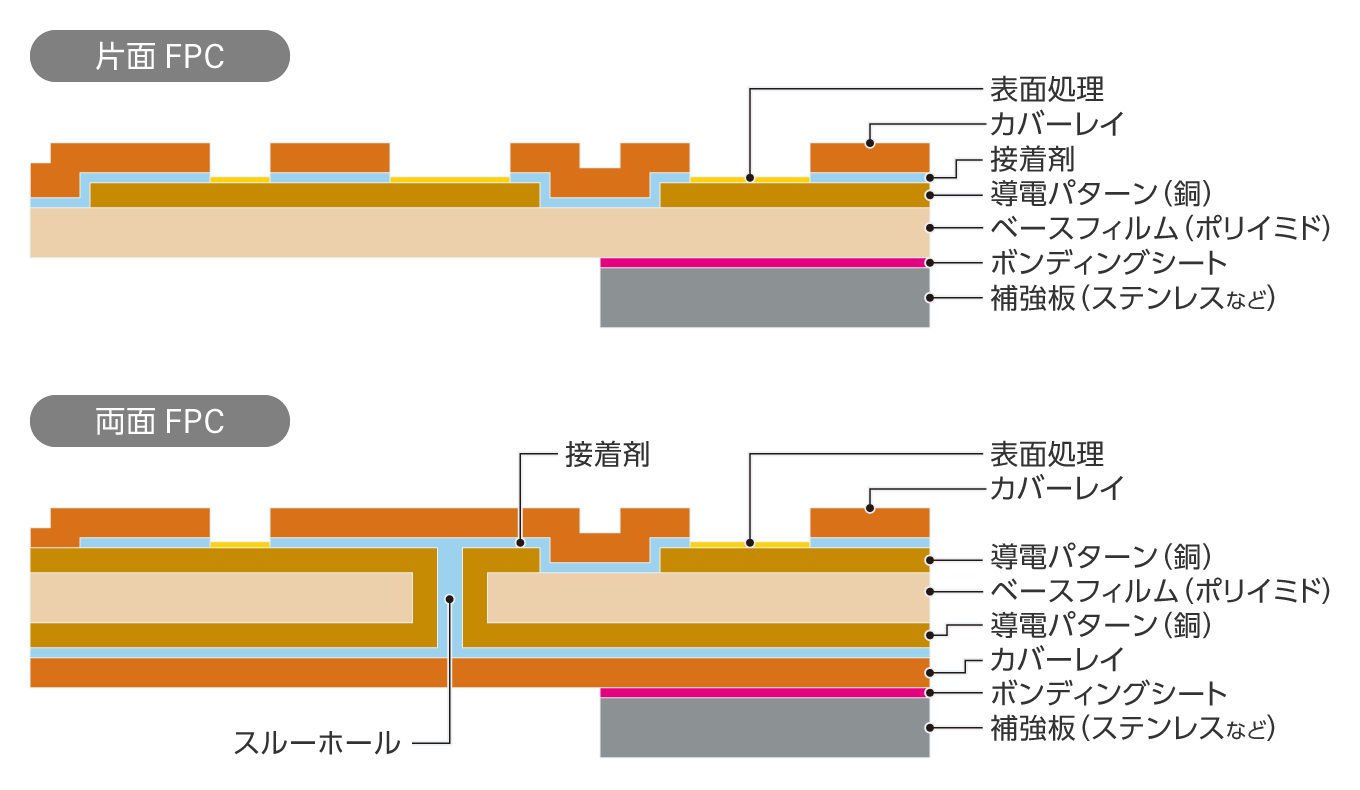
上の図は、FPCの基本的な構造を示したものです。基材(ベースフィルム)というポリイミドフィルムの上に銅でできた導電パターンがあり、そのパターンを被覆するようにソルダーレジストやカバーレイと呼ばれる絶縁層が設けられています。また、部品搭載や他の回路基板との接続部などは導電パターンが露出しており、腐食を防止するために表面処理が施されています。薄さや柔軟性が特長のFPCですが、部品を搭載する部分など機能上硬さや厚みが必要な部分には、ステンレスやポリイミドなどでできた補強板という板状の材料がボンディングシートで固定されています。
FPCの製造プロセス
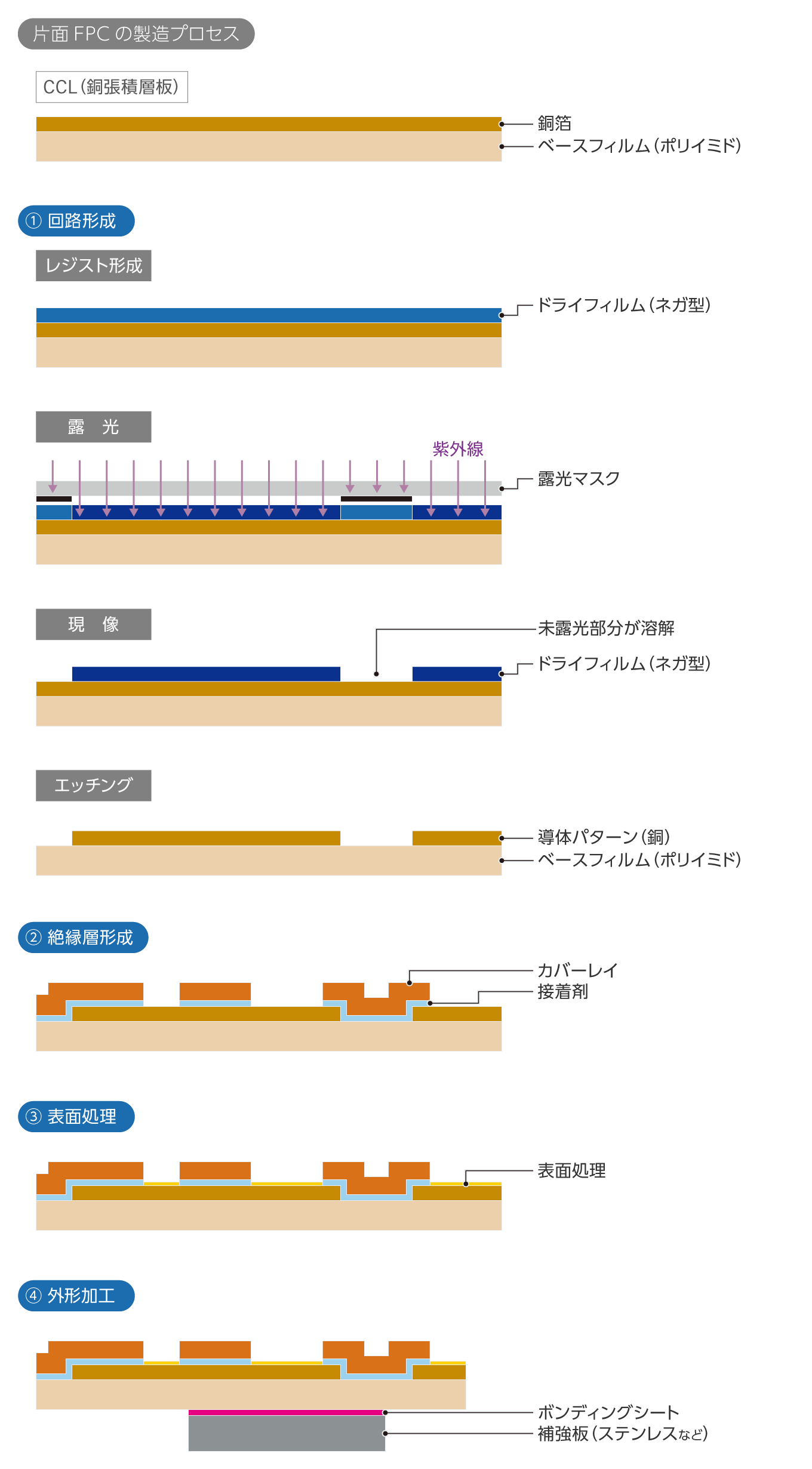
上図は片面FPCの製造プロセスを示しています。大まかに ①回路形成 ②絶縁層形成 ③表面処理(めっき加工)④外形加工の順でプロセスが進みます。
①回路形成
回路形成にもさまざまな方法がありますが、ここでは一般的なフォトリソグラフィーを使った回路形成について解説します。
[レジスト形成]
銅張積層板(CCL)の銅箔表面に感光性レジスト層を形成します。リジッド基板やFPCの場合は、ドライフィルムと呼ばれるフィルム状レジスト(ネガ型)を貼り合わせます。
[露光]
回路が描画された露光マスクを介して紫外線を照射します。ネガ型レジスト材の場合には、紫外線の照射部分の化学構造が変化し、現像液に対する溶解度が極めて小さくなります。
[現像]
レジスト層を現像液で溶解させて取り除きます。このとき、最終的に回路パターンとなる部分のレジストは溶解度が小さいためほとんど溶けず残ります。
[エッチング]
レジストで覆われていない部分の銅を化学的に溶かし、回路となる銅のみを残します。
回路上のレジストは、苛性ソーダなどの溶液を使って化学的に除去し、回路形成が完了します。
②絶縁層形成
事前に形状に加工を行ったカバーレイを所定の位置に配置し熱圧着を行ってCCLと一体化します。また、小型のチップコンデンサーやICなどの小さい部品の搭載が必要な場合には、ソルダーレジストと呼ばれる液状レジストを使って絶縁層を形成することもあります。
③表面処理
銅はさび(腐食し)やすく、そのままにしておくと、はんだ付けなどの部品搭載が難しくなるため、防錆処理として表面処理を行います。多くの場合はめっき処理で、代表的なめっき種は「金」や「ニッケル/金」になります。
④外形加工
外形加工は、FPCを一つ一つの基板に分ける作業になります。補強板はこの段階で固定されますが、この補強板の接着固定に使われるのが「ボンディングシート」と呼ばれる熱硬化性接着シートです。補強板の固定後に抜き型を使って一つ一つの基板に切り抜かれ、最終的なFPCが完成します。
以上、おおまかなFPCの製造プロセスを説明しましたが、実際にはこのようなプロセスの中で適宜検査工程があり、形状や仕様にあわせてプロセスが追加されたり、順序が変わったりすることがあります。
FPC製造に貢献するデクセリアルズのボンディングシート
デクセリアルズは現在、FPC用の「ボンディングシート」を開発・製造・販売しています。ボンディングシートは、FPCの端子部やカメラモジュールの下部にステンレス(SUS)やポリイミド(PI)、アルミニウム(AI)などの補強板を固定するために使われる熱硬化性接着フィルムで、耐熱性や接着性に優れています。(当社の粘着テープ製品に関する詳細は、接着テープの特徴とその用途 – TECH TIMES | 製造系エンジニアのための技術情報メディア (dexerials.jp)の記事をご覧ください。)また、当社のボンディングシートの大きな特長は、常温で長期保存ができる点にあります。一般的な熱硬化性接着フィルムは冷蔵保存が基本となっており、使用前に冷蔵庫から取り出して一定時間常温にさらしておく必要があります。再度保管する際には、冷蔵庫に戻す必要があります。回路基板の製造において、材料の性能発揮の観点から冷蔵保管・冷凍保管を行うことはそれほど珍しいことではありません。とはいえ、製造スケジュールにあわせて事前に材料を出し入れするのは手間がかかります。必要なタイミングですぐに使用できること、また、省エネルギーの観点からも、常温で保管できることはメリットとなります。
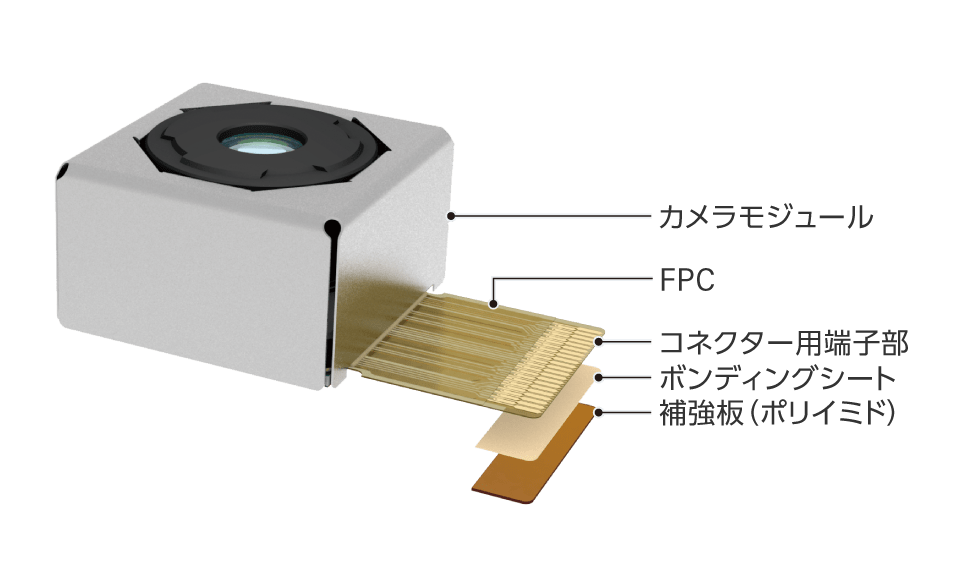
また、近年のスマートフォンに代表される通信機器では、高速・大容量通信へのニーズから回路基板に高周波伝送対応が求められています。そうした高機能なスマートフォンに実装されるFPCには、構成材料にも高周波伝送対応が求められることから、当社では高速伝送用多層FPCの層間接着用途向けに「低誘電ボンディングシート」を開発、量産販売をスタートしています。
さらに、FPCとディスプレイモジュール、カメラモジュールやICを実装するための異方性導電膜(ACF)も、高速伝送に欠かせない材料です。ACFを使ってFPCを実装することで、従来の金属ワイヤー(ワイヤーボンディング)やはんだボール、メカニカルコネクターを使った実装に比べて厚みを減らすことができるだけでなく、接続部での伝送損失を大きく低減することが可能です。
多様なエレクトロニクスデバイスにおいて、今後もますます採用が進むFPCに、デクセリアルズの材料はさまざまな形で貢献していきます。FPCに関する疑問、関連する材料の詳細については、ぜひ当社までご連絡ください。
関連記事
- SHARE
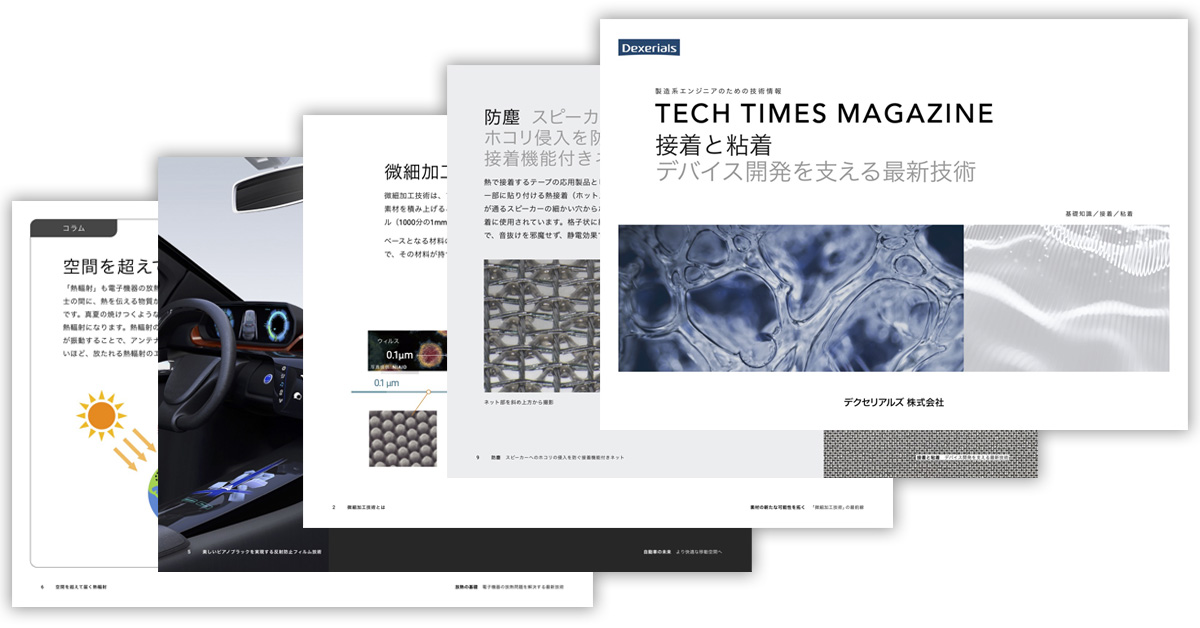
当社の製品や製造技術に関する資料をご用意しています。
無料でお気軽にダウンロードいただけます。
お役立ち資料のダウンロードはこちら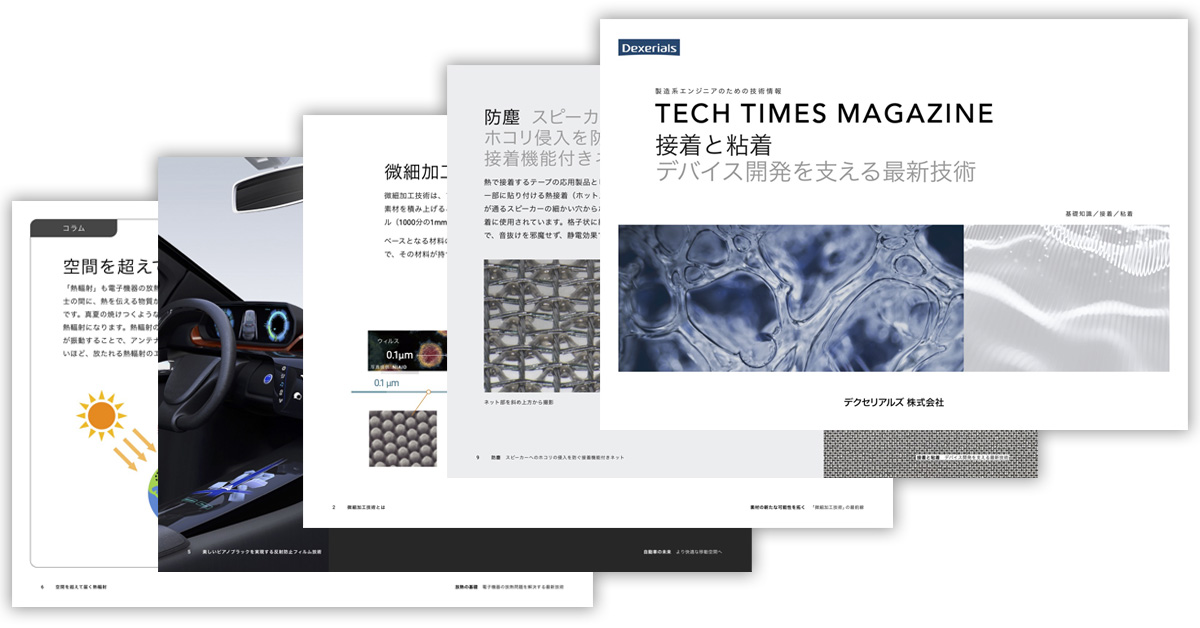
当社の製品や製造技術に関する資料をご用意しています。
無料でお気軽にダウンロードいただけます。
お役立ち資料のダウンロードはこちら