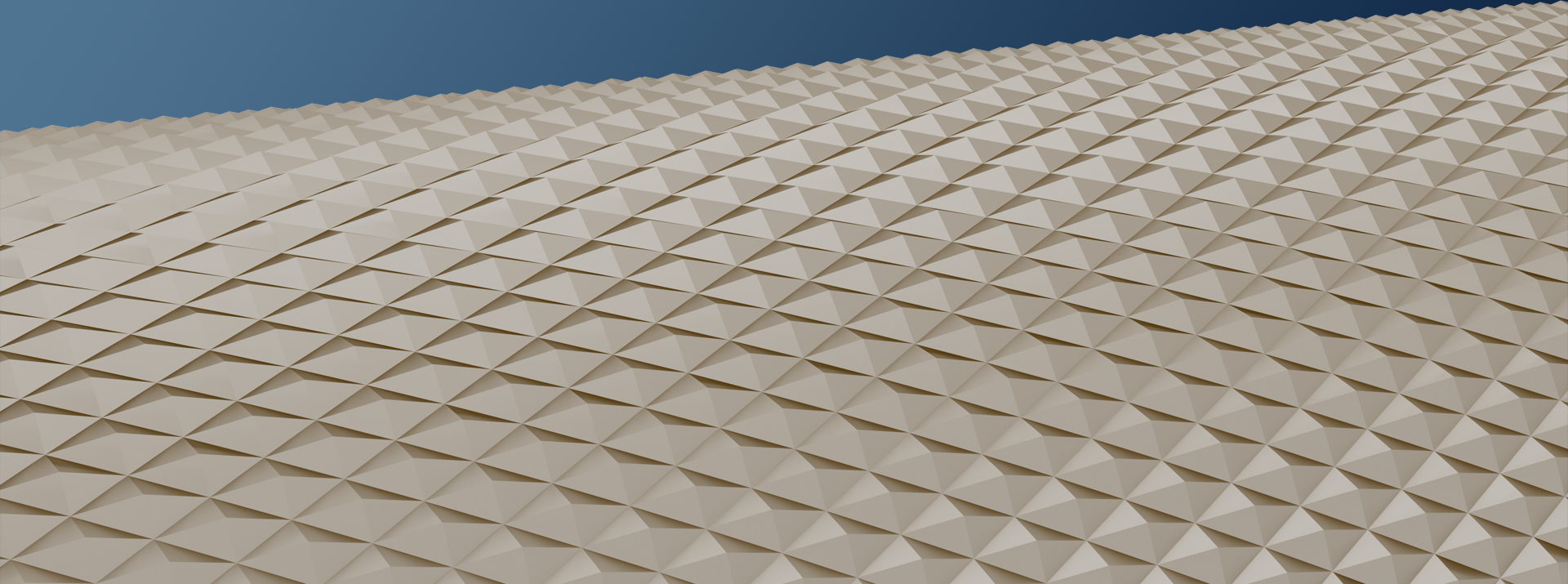
- 要素技術
インプリント技術の核心、原盤加工技術
微細構造がフィルムに形成される流れ
デクセリアルズが誇る「ロールtoロール方式のインプリント技術」は、数100nmから数100µmサイズの構造を何百mにもおよぶ長さのフィルム上に連続的に微細構造を形成する技術です。
こちらのイラストは、ロールtoロール方式のインプリントの概念図になります。左から流れてくる紫外線硬化型樹脂が塗られたフィルム基材は、中央にある微細構造が形取られた円筒原盤に押し当てられながら右側へ流れていきます。フィルム基材が原盤の下を流れる際、型に沿って樹脂が追従しますが、その過程で紫外線硬化を行うことによって基材表面に微細構造が転写・形成されます。
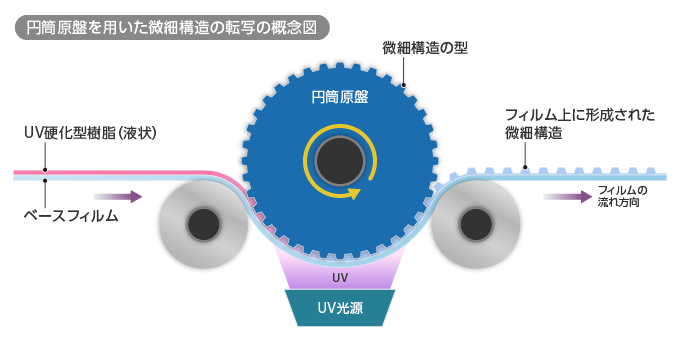
シームレスで精密な円筒原盤の作り方
当社はフィルム基材に微細構造を転写する際に用いる原盤の作り方として、「リソグラフィー加工」と「精密機械加工」の2つの技術を有しています。下の図は、レーザー描画によるリソグラフィー加工で円筒状の母材に微細構造の形を描いている模式図です。円筒形状の母材の表面にはレジストと呼ばれる樹脂が塗られており、レーザー光があらかじめ計算された動きでパターンをレジストに描いた後に、プラズマ化したガスを当てるドライエッチングと呼ばれる処理を施すことで微細構造を形成します。リソグラフィー加工はナノメートルオーダーの精緻なパターンを原盤に刻むことができます。
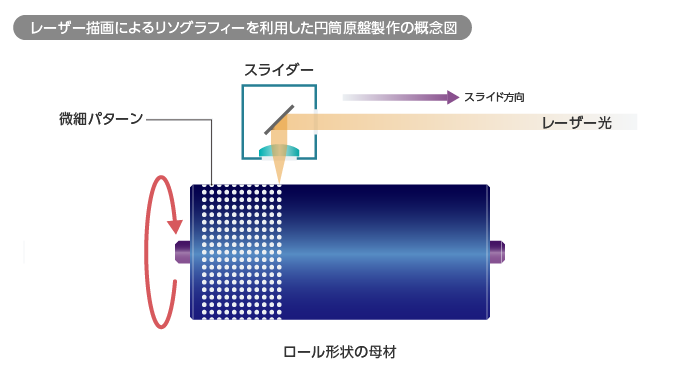
もう一つの原盤の作り方が機械による精密加工です。こちらは金属製の円筒形状の母材を回転させながら、ダイヤモンドなどの高硬度なバイト(刃)で削っていくことで表面に微細構造を形成していきます。バイトの刃の形や大きさによってさまざまな形状のパターンを刻むことが可能です。
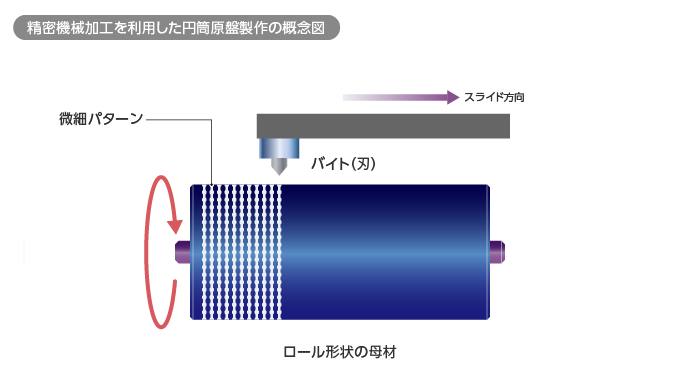
精密機械加工の驚異の加工精度
精密機械加工による原盤製作では、小さいもので単位の微細構造形成が可能で、高い精度での加工を実現しています。円筒原盤はステンレスや鉄などの金属を母材とし、その長さは1600mmと大きく、一度に大面積に対して微細構造を転写することが可能です。
精密機械加工で重要なのが、加工環境の制御です。加工中に室内温度が1°C上がると、長さ1600mmの金属の場合、熱膨張でおよそ20µm(0.02mm)長くなります。加工したい微細構造が数µmサイズであるとすると、とても無視できない変化となります。また、バイトで切削している部分では摩擦熱なども発生します。高精度に機械加工を行うためには安定した加工環境が欠かせません。デクセリアルズでは無人での自動加工はもちろん、室温、母材温度など加工精度に影響を与える数多くのパラペーターをシビアに制御し、意図する形状を高精度に加工しています。
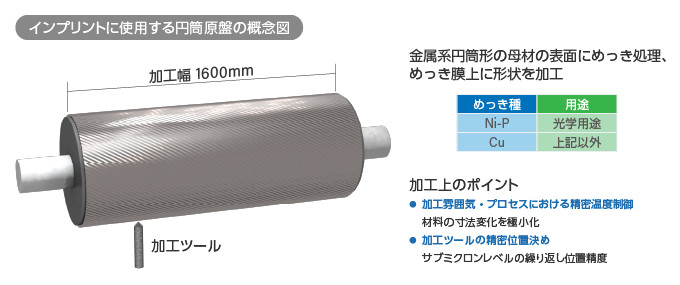
原盤加工の切削プロセス
こちらは精密機械加工のプロセスを示したチャートです。まず、母材上に施された快削性のめっき層に、目的とする微細なパターンを適切なバイトで刻み込みます。次に試験的にUVフィルムを形成して、走査電子顕微鏡(SEM)での計測・評価を行った後、洗浄と離型処理※を施し、インプリント用円筒原盤が完成します。
※型押しされた樹脂が原盤から剥がれやすくする加工のこと。
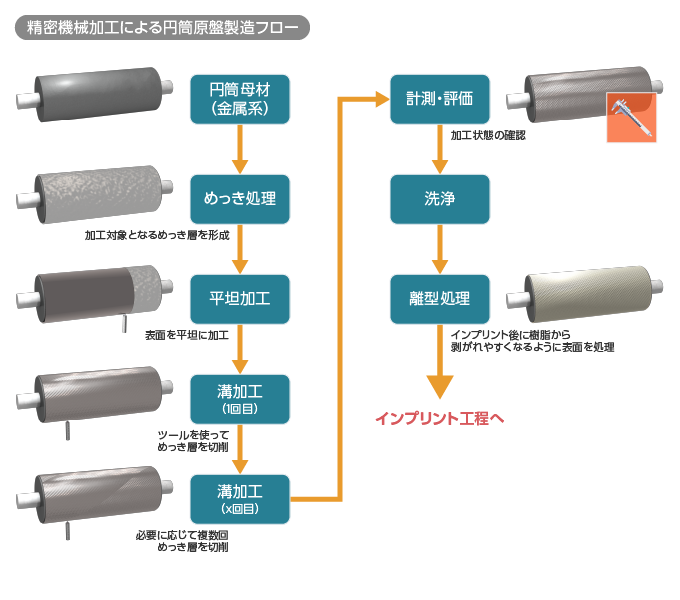
精密機械加工による微細形状の事例
こちらの写真は、精密機械加工で原盤を使って作成された「液晶テレビ用の輝度向上レンズフィルム」の電子顕微鏡による拡大画像です。表面に刻み込む山型の大きさや形状は、切削する刃物の大きさ・形状によってさまざまに変化させることができます。
精密機械加工技術によって生まれる微細構造は、その形によって光や熱の反射をさまざまにコントロールすることが可能です。デクセリアルズはインプリント用円筒原盤の精密機械加工技術をもとに、素材だけではなしえない機能の実現に向けて研究開発を進め、新たな製品の可能性を追求してまいります。
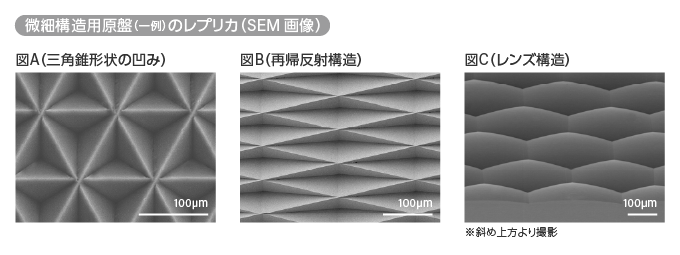
関連記事
- SHARE
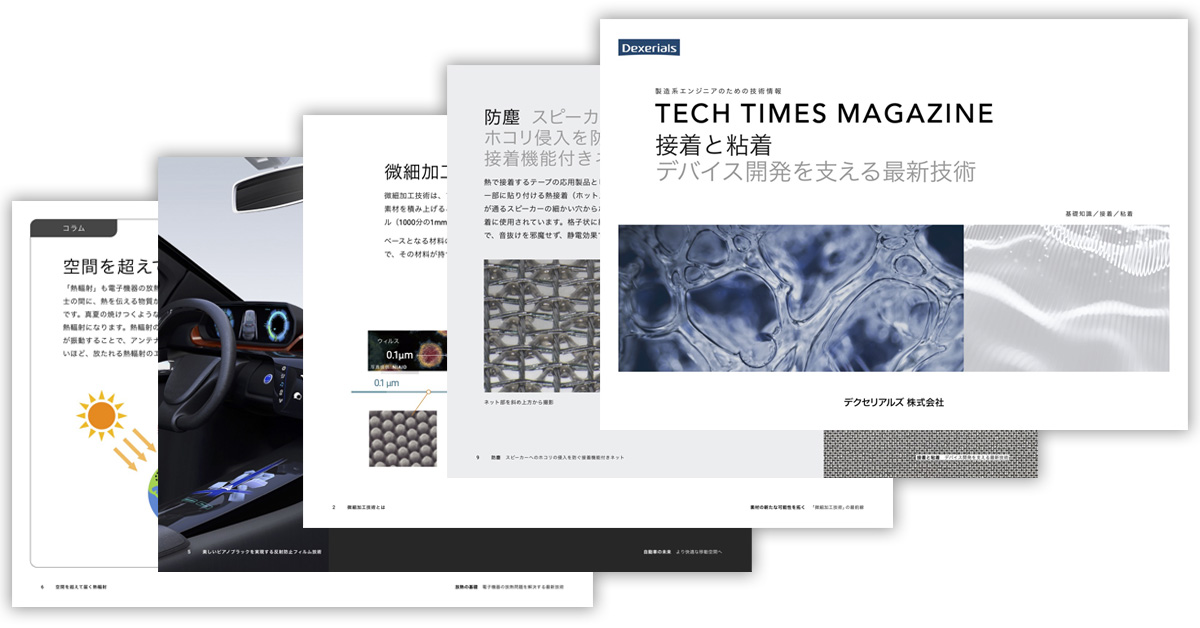
当社の製品や製造技術に関する資料をご用意しています。
無料でお気軽にダウンロードいただけます。
お役立ち資料のダウンロードはこちら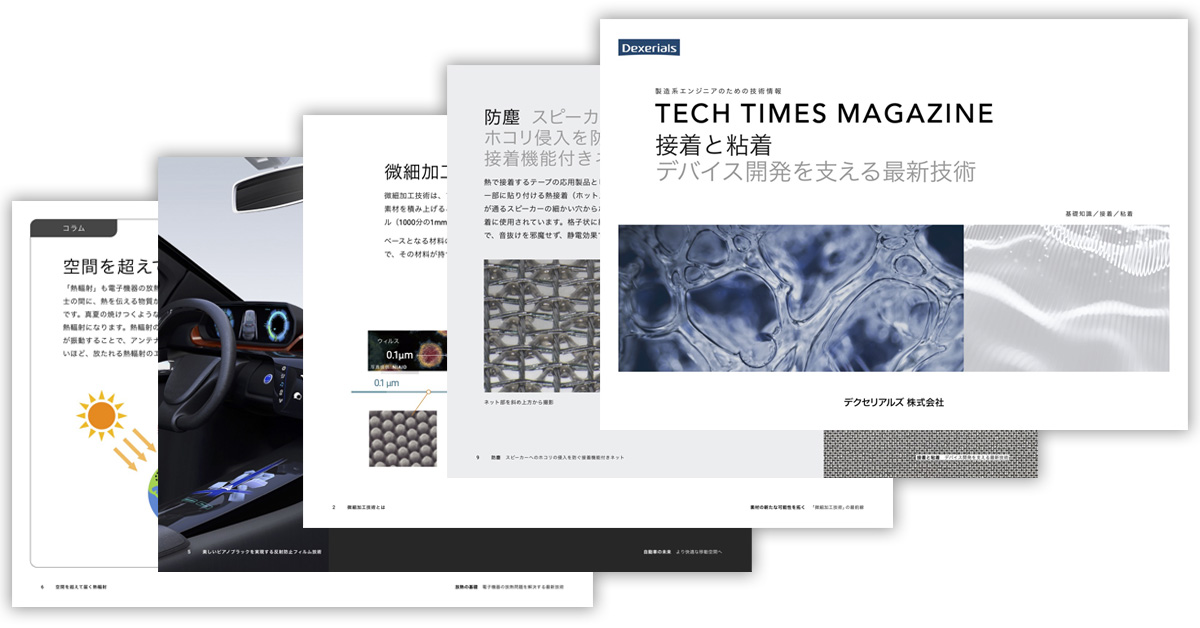
当社の製品や製造技術に関する資料をご用意しています。
無料でお気軽にダウンロードいただけます。
お役立ち資料のダウンロードはこちら