
- Electronic Components
The history of power tools and secondary protection element (SCP)
Tools are indispensable for building and creating almost anything. This article describes the history from the invention of power drills to the latest smart electric tools. It will also review safety requirements and increased battery capacity of cordless power tools.
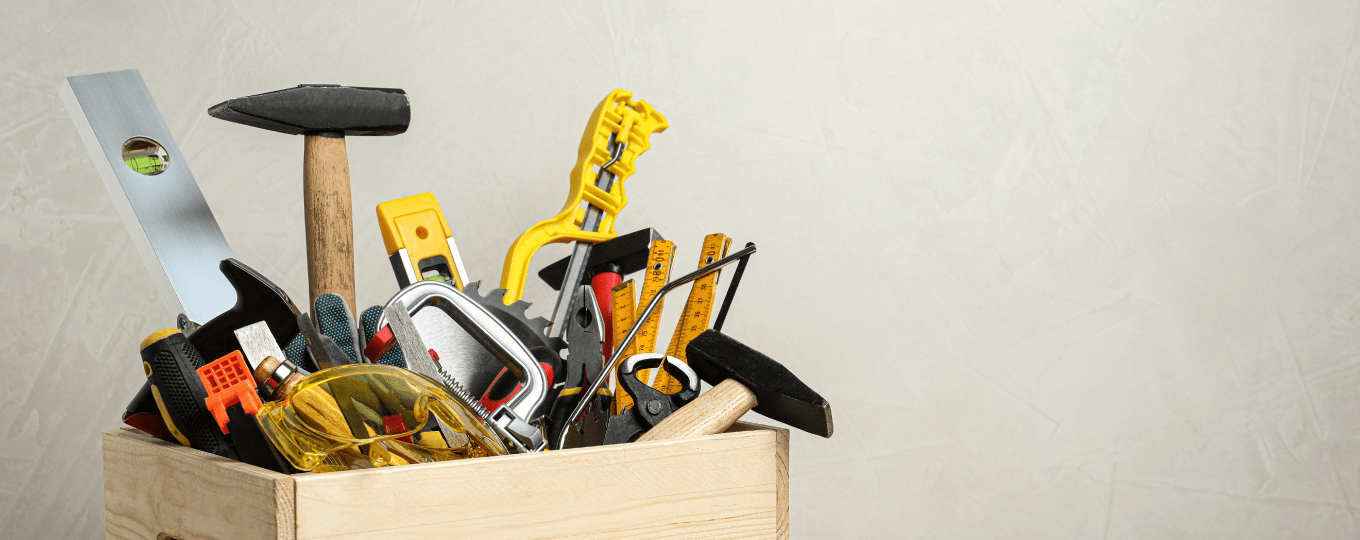
Contents
- 1 The history of the power drill
- 2 The invention of the cordless drill and the introduction of tools with lithium-ion batteries
- 3 Power tools with higher voltages
- 4 The electrification of gardening tools
- 5 Pros and cons of engine and electric tools
- 6 Emergence of smart power tools
- 7 Stricter safety standards as battery capacity increases
- 8 Dexerials’ secondary protection element (SCPs)
The history of the power drill
Drills have been used since ancient times to make holes in boards. Hand-powered drills were commonly used until the world’s first power drill was created by Arthur James Arnot and William Blanch Brain in Melbourne, Australia in 1889. At the time of its invention, the power drill was a specialized tool for drilling holes in wood and metal by attaching a drill and rotating it. Since then, drills for other functions were created and the increase in the variety of tools attached to the tip made it possible to perform various tasks such as drilling, tightening, loosening, grinding, and polishing.
A major milestone in the evolution of the power drill came in 1916, an American power tool company began manufacturing a drill with a “pistol-grip” and “trigger switch.” Until then, power drills were so large that they had to be operated by two people. The pistol-grip design reduced the size, allowing it to easily be carried around. The trigger-switch power allowed the drill to turn on while pressing a trigger. The same company then introduced the world’s first power drill for home use in 1946, selling one million drills by 1951. Incidentally, in Japan, a major electronics manufacturer developed and sold the first domestically produced power drill in 1935.
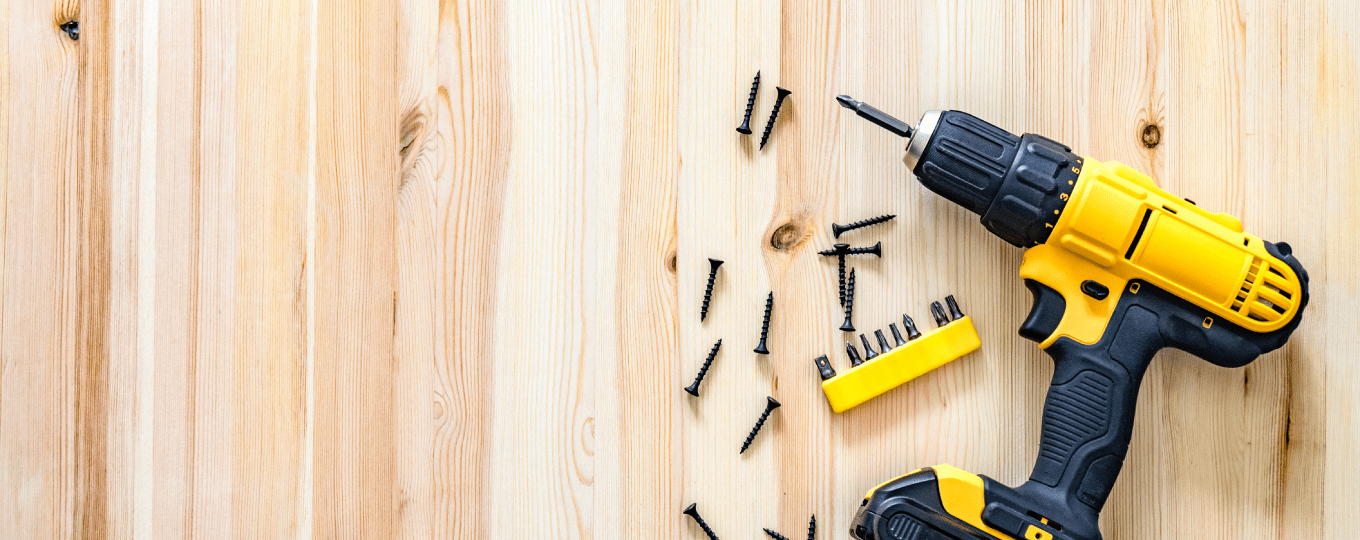
The invention of the cordless drill and the introduction of tools with lithium-ion batteries
The largest power tool manufacturer in the US then developed the world’s first cordless drill powered by nickel-cadmium batteries in 1961. Other types of battery-powered tools followed, and a variety of handheld tools and equipment emerged such as lawn mowers, vacuum cleaners, hand saws, and polishers.
In 2005, another American power tool manufacturer introduced the world’s first power tool with lithium-ion batteries. Since then, lithium-ion batteries replaced nickel-cadmium batteries in most tools. Lithium-ion batteries and rechargeable power tools enabled easier handling, enhanced stability, and optimized forced-air cooling systems.
Since electric tools have more torque (rotational strength) at higher voltages, many of the tools that were initially 12V increased to up to 14.4V. Lithium-ion batteries were initially adopted with a standard of 14.4V and 3.0Ah. However, since around 2010, the voltage of lithium-ion batteries increased and tools that use 6.0Ah lithium-ion batteries are now common.
In addition to increased voltage, the charging time of the batteries shortened. These products required several hours to recharge in the past, but most recent products can be recharged in as little as 15 to 30 minutes. Power tool manufacturers develop the outer tool housing and control board while the battery is purchased from battery manufacturers. Therefore, there is no significant difference in the performance of power tool batteries between manufacturers.
Power tools with higher voltages
As mentioned above, power tools have increased in voltage in recent years. In particular, European and US manufacturers tend to install more cells in battery packs in order to increase battery capacity and output. However, increasing the number of cells in a battery pack also increases its size, compromising the portability of power tools.
Almost all power tools use a general-purpose sized lithium-ion battery “18650.” Since the voltage of lithium-ion battery is approximately 3.6V per cell, the entire battery will have a voltage in multiples of 3.6V. Power tools often use 14.4V with four cells connected in a series, or 18V with five cells connected in series. Both offer a good balance of power and size. Below is a comparison of the features of each battery pack.
Comparison of 14.4V and 18V battery packs
14.4V | 18V | |
---|---|---|
Number of 3.6V cells | 4 cells | 5 cells |
Weight | Somewhat light | Heavy |
Size and handling | Slightly small and easy to handle | Slightly large and difficult to handle |
Workability in heavy-load, continuous work | Motor tends to heat up and may stop due to overheating. | The motor does not generate heat easily and can be used for longer period of time. |
Run time | Short | Long |
Cost | Cheaper | Expensive |
There has been a shift from 14.4V batteries to 18V batteries, especially in the professional power tool market. Furthermore, more recently, an increasing number of power tools are equipped with 36V batteries to increase motor output. Currently, most power tools with 36V batteries remain compatible with 18V battery power tools. Therefore, 18V battery-compatible products are expected to remain mainstream in the power tool industry for some time.
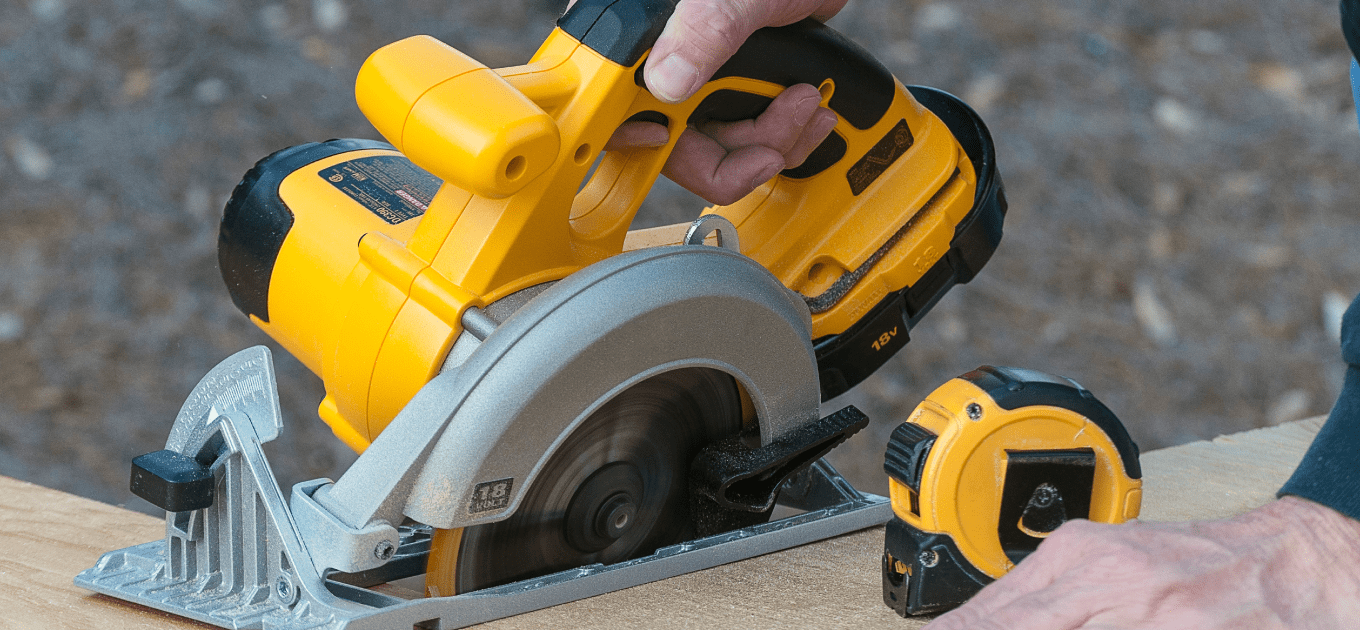
Electric tools, especially rotary tools such as circular saws and angle grinders, are likely to benefit from the shift to higher voltages as efficiency increases significantly. If 18V and 36V products use motors with the same output, the higher the voltage, the lower the current flowing to the motor. This reduces motor loss (heat generation) and results in higher motor efficiency, improving productivity.
In addition, due to regulations in various countries aimed at reducing CO2 emissions, the number of gas-powered tools are declining. Equipment with large-capacity battery packs is therefore expected to replace gas-powered equipment. It should be noted that the capacity of the battery itself has not improved, so the amount of work possible per charge does not change much.
The electrification of gardening tools
In recent years, gas-powered gardening tools such as lawnmowers and chainsaws have been shifting to electric versions that use batteries and motors in response to reducing CO2 emissions.
Gas-powered gardening tools have reliable power. In particular, two-stroke engines were often used in gardening tools. While two-stroke engines have the advantage of being lightweight, compact, and capable of producing high output, their downsides include exhaust emissions and high consumption of gas. In a two-stroke engine, combustion becomes unstable because the air-fuel mixture and combustion gas mix during the scavenging process. Two stroke-engines require oil to be mixed with fuel and some of it comes out of the exhaust. Therefore, four-stroke engines are more fuel efficient and environmentally friendly. In the US, it has become harder to find two-stroke engine lawn mowers. Furthermore, the state of California passed a legislation in 2022 to restrict the use of gas-powered lawn equipment by 2024 to reduce air pollution.
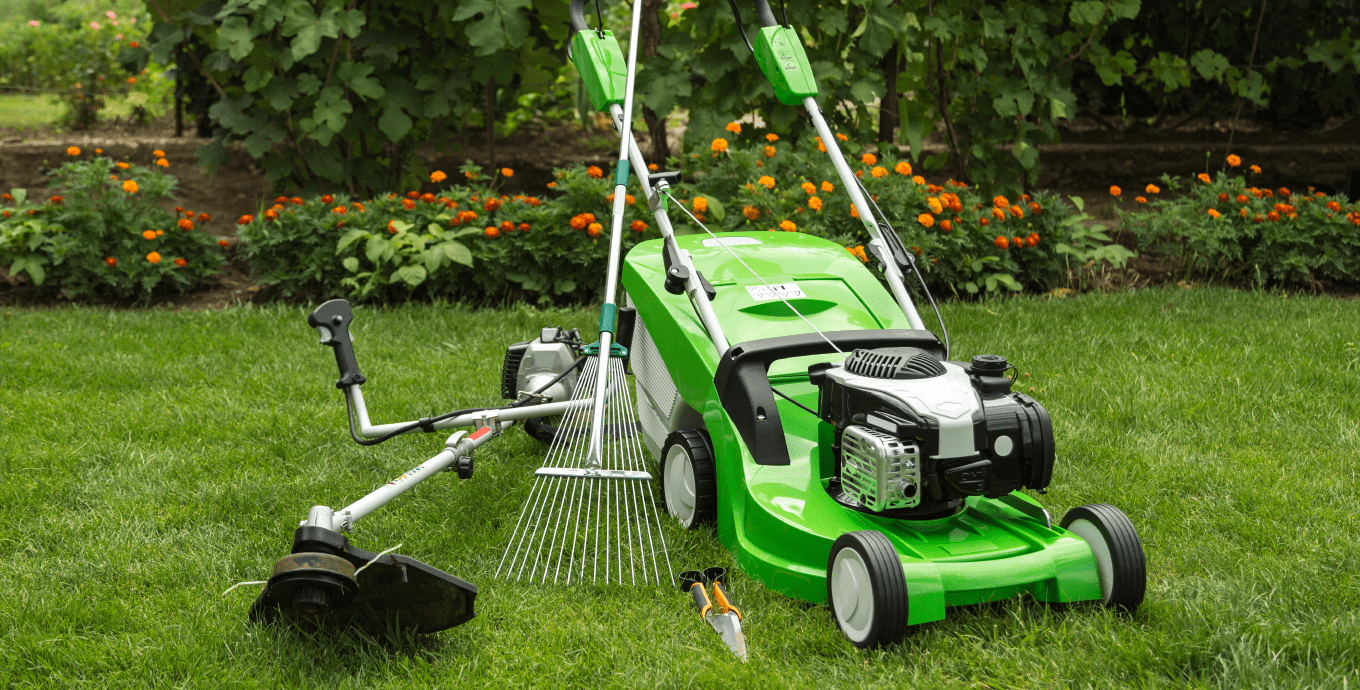
Pros and cons of engine and electric tools
A major advantage of electric gardening tools is that they are easy to use, with no need to prepare or replenish fuel or oil. In contrast, gas-powered gardening tools require engine maintenance and proper storage. For two-stroke engines, the fuel mixture is a specific ratio of regular gasoline and oil. Over time the gasoline evaporates and deteriorates. Using a degraded fuel mixture in the engine will cause it to start up poorly and can also cause the carburetor and fuel filter to clog. Additionally, if water gets into the engine due poor storage conditions, the tool may stop working. Although these engine and fuel-related maintenance needs are irrelevant for electric gardening tools, there may be some limitations as described in the table below.
Comparison of electric and gas-powered gardening tools
Electric gardening tools | Gas-powered gardening tools | |
---|---|---|
Output and usability | Slightly inferior as it may not be suitable in some high-load work. | Superior as high engine displacement enables mowing of dense areas, etc. |
Maintenance | Low maintenance, needs battery charging. | High maintenance, requires mixed fuel and maintenance of engine, fuel tanks |
Exhaust emission control | No issues | Needs to comply with emission regulations |
Run time | Usage is limited (depending on battery capacity). | Long. Can run for several hours with 1 liter of mixed fuel. |
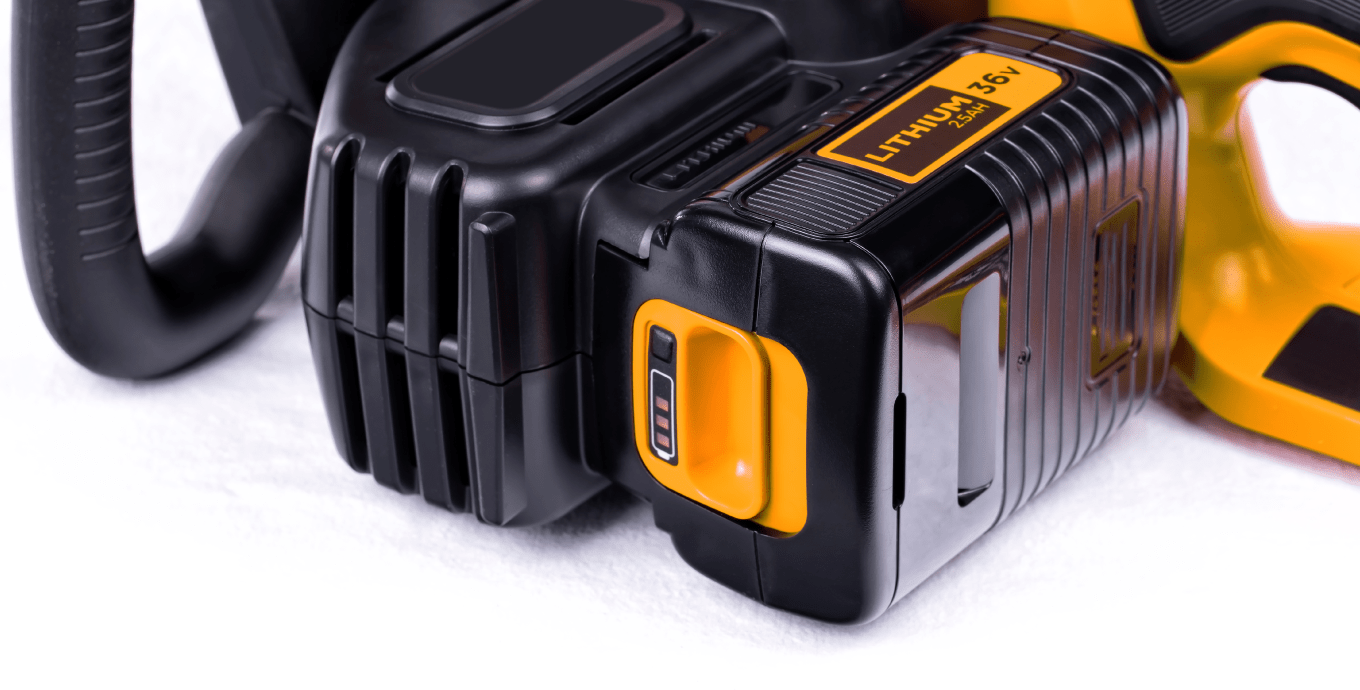
Since high output is required for gardening tools, most electric products use 36V batteries. Some manufacturers offer a series of gardening tools with an even higher battery voltage of “80V” (actually 72V). Electric mowers currently on the market have short battery life and lack power, especially when used for mowing densely vegetated areas. Therefore, it is expected that gardening tools with increased voltage will emerge eventually to accommodate such issues.
Emergence of smart power tools
With the shift from gasoline to electric tools, smart power tools are also emerging in the US and Europe. Smart power tools may be equipped with Bluetooth communication functions to enable detailed tool setting, locking functions, and cloud tracking.
Smart power tools enable the following three functions.
- Tool management for tracking and monitoring
- Customized settings for precise performance
- Theft protection
Internal IC tags enable the individual identification of each tool. Linking IC tags to smartphones and PCs enables the systemization of tool management, including confirmation of repair requests, maintenance history, and inventory management. In addition, some power tools equipped with Wi-Fi modules can be connected to a network to automatically manage and maintain torque settings. This improves traceability and displays the work process. Work that previously required artisanal experience can now use the internet to achieve higher efficiency and product quality.
Stricter safety standards as battery capacity increases
The most important aspect when using power tools is safety. In particular, lithium-ion batteries used in power tools require high safety standards because of the possibility of combustion due to their operating principle.
The international safety standard (UL 62841-1) recently updated requirements for lithium-ion cells and battery systems. Currently, lithium-ion cells installed in tools are required to comply with either the UL 62133 or IEC 62133 international standards. These also address the charging of lithium-ion battery systems, and require the cells to remain within the “specified operating region” during standard charging. (see below).
a) Open circuit voltage is at least 90% of that before the test
b) Conforms to standard charging and recharging tests
c) No damage to cell vents
In each standard, power tools are evaluated as complete products including the power tool body, battery pack, and battery charger. As a result, charger and power tool manufacturers that produce their own chargers are required to be compliant with the new lithium-ion battery requirements.
When testing and evaluating power tools with lithium-ion cells, both voltage and charging current must remain within this specified operating range. Other additional requirements are the implementation of enclosure pressure tests to confirm that the battery pack will not explode or catch on fire and mechanical strength tests to confirm that the battery pack functions properly even when subjected to impact, such as being dropped.
As a matter of fundamental safety, lithium-ion charging systems must ensure that combustion or explosion never occurs even if a component enters a state of failure. If a component in the charging device fails, the cell must not exceed the upper charge voltage limit of 150 mV, and if it does, the charging device must be permanently disconnected.
Dexerials’ secondary protection element (SCPs)
Dexerials’ Self Control Protector (SCP) is used to improve the safety of lithium-ion battery-equipped power and gardening tools. The SCP is a secondary protection element component that interrupts circuits when an overcharge or overcurrent occurs in lithium-ion batteries. Since its launch in 1994, Dexerials’ SCP has been recognized as a standard component of secondary protection of Li-ion batteries. As the number of cells increases in a battery, SCPs are now required to handle higher voltages. The article on battery protection circuits for higher voltages can be found here.
There are three major advantages of adopting SCPs in electric power tools.
- Improved safety: Ensures permanent disconnection of the circuit when battery is unstable and when primary protection is not functioning properly. This prohibits reuse of abnormal packs
- Fast charging: Low fuse resistance to accommodate fast charging devices.
Control of fuse blow curve: It heats up when energized, enabling immediate shutdown in case of abnormality.
Power tool and electric gardening tool markets will continue to grow as people work remotely from home. Dexerials hope to enhance the safety of power tools and electric gardening tools with SCPs.
- SHARE