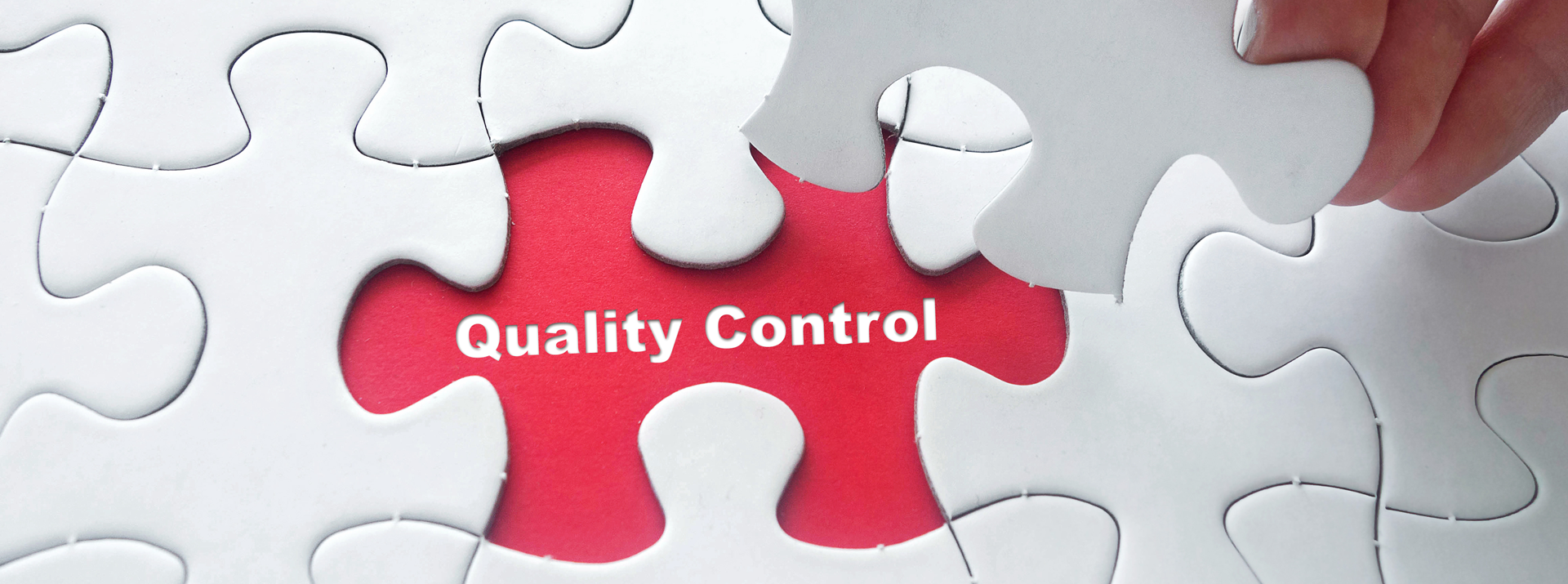
- Electronic Components
Quality control of Dexerials’ secondary protection element, providing safe Li-ion batteries
Contents
The importance of safety and security
The Self Control Protector (SCP) manufactured by Dexerials is a safety component for lithium-ion batteries as it cuts off the circuit by blowing the built-in fuse element in the event of overcharging or an overcurrent. Dexerials conducts multiple strict checks throughout the manufacturing process to ensure the product properly functions.
In the manufacturing process of food and other products, it is common to allow a certain degree of variation in the shape and size of the finished products. Even if there are some differences in shape or size, it does not make the product inedible or cause a significant change in taste. Instead, thorough hygiene controls are put in place to prevent health hazards.
When it comes to semiconductors, which are considered precision components, high-quality raw materials, advanced manufacturing equipment, and clean manufacturing conditions are necessary. This results in very high degree of process stability and integrity. Sampling inspections are the most common method of process performance inspections (while full inspections are the most common method for the functional testing of products). Since sampling inspections cost less than full inspections, they are used in the manufacturing process of many industrial products.
However, since SCPs are one-time use components, it is not possible to test their functionality (verification testing) prior to shipping. Therefore, the manufacturing process must be strictly controlled to ensure the integrity and traceability (i.e. being able to confirm when, where, and the materials and processes the product has been subject to) of the product. Dexerials conducts multi-step inspections throughout the manufacturing process and below are some examples of the testing Dexerials performs at each stage of the manufacturing process.

The diagram above provides an overview of the SCP manufacturing process and pre- / post-manufacturing inspections.
Assembly Test|Checking the bonding & attachment of the fuse element
In the assembly stage, the fuse element is mounted onto a ceramic substrate and connected to three electrodes. For it to work properly, the connections must be made correctly in this process.
After attaching the fuse element, Dexerials uses a specialized inspection machine to check the assembly, as it can impact the fuse’s capabilities.
Flux Test|Checking the flux supply
A flux is coated on the fuse element to help it melt and function properly. Since the flux material is involved in the melting of the fuse element, it can also affect the fuse’s capabilities. Therefore, Dexerials checks that it is applied and coated correctly.
Visual and electrical test|Functional testing post-cap assembly
After the flux is applied, the cap is mounted and attached.
Although the cap is primarily a cover that protects the fuse element from external elements and prevents external heat from melting or otherwise affecting the fuse element, it also has several other functions. The fuse element is a flat solid plate, when it melts and is blown by being attracted to the electrodes, its shape changes due to surface tension. For this reason, the cap must have an adequate amount of space around the fuse element. Without this space, the fuse element will not be able to operate properly because the cap will prevent melting process. The cap also serves as a tag for the product’s model and lot numbers information, which contains the manufacturing history. The lot number is particularly important for traceability explained further below.
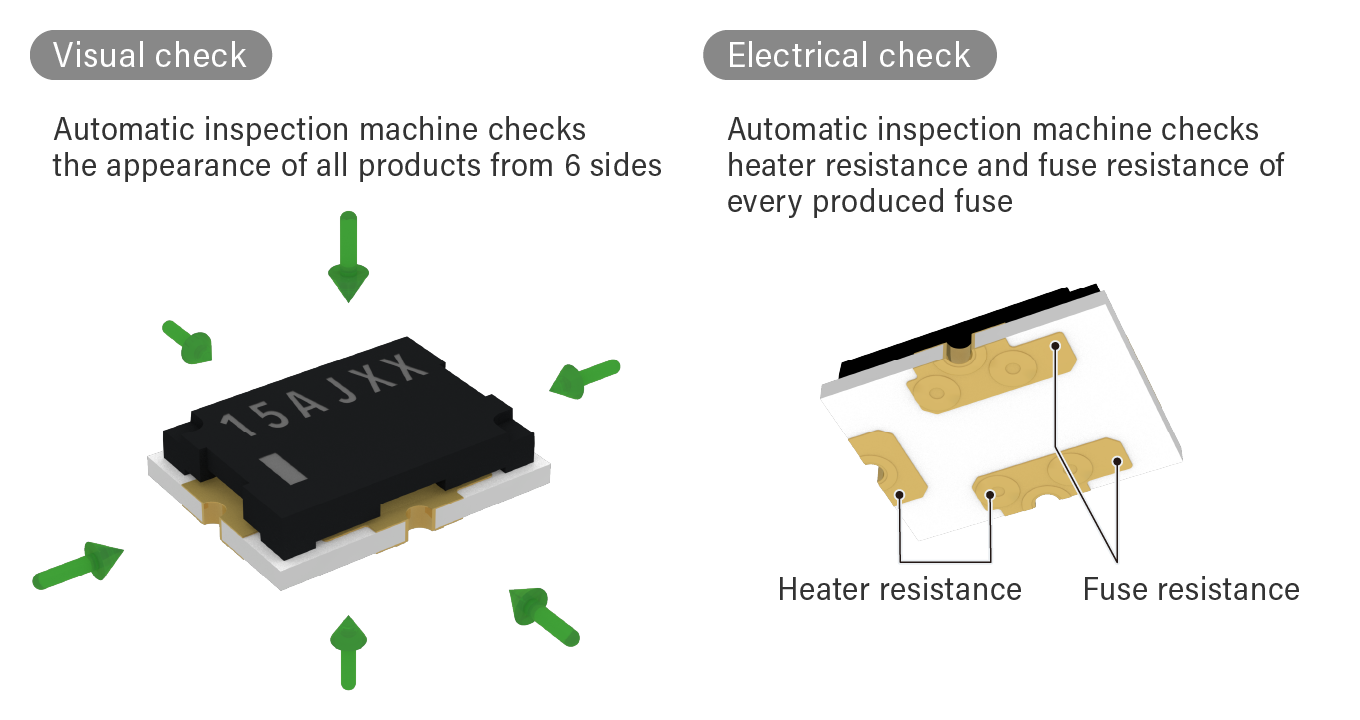
SCP’s product information such as lot numbers are printed by laser. The SCPs are then fully inspected for its appearance and resistance. The appearance of the glued caps is checked for misalignment, chipping and other defects to ensure that the cap is securely fixed. Then, the heater and fuse are inspected for resistance. During the visual test, an automatic machine checks the appearance of all six sides of the components. Due to its small size, even a small visual abnormality can hinder the automatic mounting process and affect the mounting quality. SCPs that pass this inspection are then taped, reeled and prepared for shipment.
Traceability
As a safety component for lithium-ion batteries, SCPs require strict traceability. In general, lot numbers are assigned to each industrial product unit at the time of manufacture. They are used for the quality and production quantities control. In quality control, lot numbers are used to identify a group of defective products. Tracking the history of products manufacturing dates, helps determine the scope of damage and the root cause of the defect. The lot unit is usually set independently by the manufacturer according to the characteristics and properties of the product.
SCPs are also assigned lot numbers representing the production unit. As shown on ‘code marking’ step on “Manufacturing Process” image, SCPs are assigned a tracking code for each assembled board, the smallest unit of production, to ensure rigorous tracing. Every step of the SCP manufacturing process, from assembly of the fuse element to assembly of the cap, is controlled, and all produced SCPs in the production lot are traceable. Therefore, in the unlikely event of a defect at a customer site, it is possible to investigate the history of the product and trace the date of its manufacture, as well as the materials, equipment, and manufacturing conditions.
There are not many industrial products with traceability down to the materials used in a single component, including an additional marking process (tracking code) for this purpose. Dexerials continuously pursues product safety and reliability by establishing a meticulous control system for its SCPs.
- SHARE