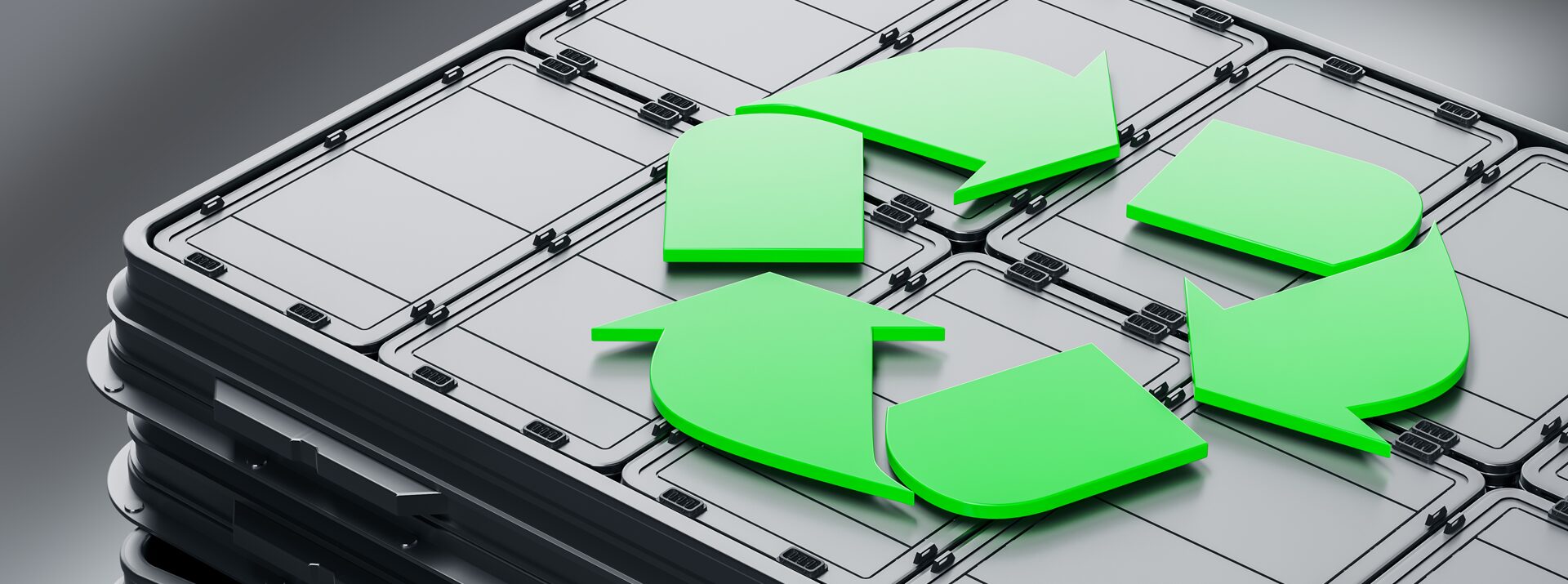
- Electronic Components
Towards a Sustainable Society: The Recycling and Reuse of Lithium-ion Batteries and Dexerials’ Protective Devices
Contents
Towards a sustainable society
Efficiently processing used lithium-ion batteries and reusing the resources from them present a significant challenge in protecting today’s global environment. This article explores the landscape of lithium-ion battery reuse and recycling, and related efforts, using the following definitions:
– Recycle: Dismantling and repurposing batteries
– Reuse: Utilizing batteries in their existing form
Additionally, this article highlights the European Union (EU) battery passport system, set to launch in 2024, and Dexerials’ protective devices.
Current landscape of lithium-ion batteries
To achieve the Sustainable Development Goals (SDGs), there has been increasing adoption of electric vehicles (EVs) and renewable energy sources in a variety of applications, leading to a sharp increase in the use of lithium-ion batteries. To efficiently utilize the precious resources from these batteries, attention is turning to urban mining, which involves extracting rare metals from used batteries for recycling, and repurposing large EV batteries for other applications.
However, in many countries, discarded lithium-ion batteries currently end up in landfills. In Japan, a recycling process for small batteries has been mostly established. Globally, the recycling rate as of 2022 remains low at around 5%.
Recycling small lithium-ion batteries
To recycle used small lithium-ion batteries, appropriate collection methods are essential. In Japan, many municipalities have established rules for collecting lithium-ion batteries separately from other waste, requiring specific collection methods and routes.
Once collected, the batteries are processed in vacuum heating furnaces, followed by acid leaching, solvent extraction, and electrolysis to extract and recycle rare metals such as cobalt and nickel. During these processes, it is crucial to implement proper safety measures against flammable electrolytic solutions and the generation of harmful gases.
However, lithium is usually treated as slag because it offers few economic benefits when recycled. Additionally, the extracted rare metals are not always repurposed as battery materials.
Battery manufacturers are improving recycling efficiency by labeling the metals contained in cathodes (positive electrodes from which current discharges). Recycling facilities then sort the used batteries by type based on this information, ensuring their proper processing. These efforts are important for the more efficient recycling of batteries and the sustainable use of rare metals.
Recycling large lithium-ion batteries
Recycling large lithium-ion batteries, such as those used in electric vehicles (EVs) and stationary storage units, presents particular challenges compared to smaller batteries. These batteries are bulky and heavy, vary in shape depending on the manufacturer and model, and are designed with sturdy casings. The increased risk of electric shock and ignition also complicates their recycling process.
Recycling methods, such as combustion, acid dissolution, and solvent extraction, can technically be employed in the recycling process to recover cobalt, nickel, and other metals. However, the challenges lie in ensuring the purity and quality of these recycled resources and keeping recycling costs below the prices of the resources. Particularly, the metals intended for repurposing as battery materials must meet extremely high quality standards.
Additionally, the costs associated with developing recycling processes, investing in facilities, and operating plants are significant factors affecting the viability of recycling businesses. The fluctuating prices of cobalt and nickel also pose a business risk.
Recycling large lithium-ion batteries is vital for sustainable energy use. Currently, it is an area of active research and exploration worldwide to achieve commercial viability. Overcoming technical and economic challenges will not only promote effective resource use but also contribute to achieving a sustainable society.
Battery passport system in Europe
With the battery passport system set to launch in 2024, the European Union (EU) aims to enhance the transparency and traceability of information throughout the entire battery life cycle. This system will apply to industrial and electric vehicle (EV) batteries with a capacity of over 2 kWh, including those imported for use within the EU. It is designed to ensure transparency at every phase—from the mining of raw materials and manufacturing to usage, recycling, reuse, and eventual disposal—by managing information on the entire value chain through a unified digital platform.
The system will require batteries to be labeled with QR codes, ensuring that passport information is readily accessible. These labels enable consumers and related business operators to easily obtain details on batteries.
The specifics of the information to be recorded will be outlined in technical rules to be defined by 2024. Current draft revisions anticipate recording the details enumerated below.
◆ Information to be recorded in battery passports
Mines, origins of materials, material producers, part manufacturers, cell manufacturers, module manufacturers, final product manufacturer, weight, purpose, chemical composition (material ratio etc.), recycled material content, ID, type, model, product name, performance, durability, carbon emissions during manufacturing, hazardous materials, battery health checks, carbon emission impact, directive conformity declaration, movement and collection, information related to due diligence, ownership history, life cycle carbon emissions, environmental impact through life cycle
(Source: Battery Passport (globalbattery.org))
Approximately 70% of cobalt, essential for lithium-ion battery production, used is sourced solely from the Democratic Republic of the Congo, a country grappling with frequent issues related to child labor and due diligence. Some analysts believe that European regulations concerning the origins of materials and due diligence represent a strategic move made by European countries to safeguard themselves.
(Source: Battery Passport: A European Strategy for Leading the EV Market | Bright Innovation (brightinnovation.jp))
Reuse of large lithium-ion batteries
As the electric vehicle (EV) market expands globally, more attention is being directed to reusing large lithium-ion batteries for EVs. However, EV batteries are relatively new products with no established recycling methods. Conventional recycling methods used for small batteries pose technical challenges when applied to larger batteries, such as inefficiencies caused by their interconnections with harnesses, circuit boards, and cooling components.
This recycling difficulty makes a combined approach of partial recycling and reuse a viable option. Large batteries are expected to be reused for various applications, including large-scale energy storage and backup power supplies, in addition to EVs and other uses in mobility.
In fact, the EU anticipates that over 70% of EV batteries, if used for 15 years or less, will be reused rather than recycled. Despite their degradation over time, these large, high-performance batteries can still function effectively. Once EVs reach the end of their vehicle life, the installed batteries can be repurposed as replacements for other EVs, used in vehicles such as forklifts, or as stationary storage at factories or data centers. Another option is to reuse them as home storage batteries.
However, batteries used for extended periods of time are too degraded for reuse. In many cases, reused batteries are assessed for recycling potential.
For instance, a Japanese automotive manufacturer, in collaboration with a partner, has developed a system to analyze and rank battery modules removed from EVs to ensure their sustainability for reuse in EVs, stationary storage, and backup applications. These batteries can last 10 to 15 years after collection, significantly longer than traditional lead batteries used for backup.
As detailed above, the reuse of large batteries is expected to play an important role in the effective use of batteries and the reduction of environmental impact (reduction of waste).

Necessity of protective devices in the reuse of lithium-ion batteries
Dexerials’ Self Control Protector (SCP) for lithium-ion batteries is a protective device for Battery Management Systems (BMSs) that monitor the safety of lithium-ion batteries. It shuts off circuits in response to any abnormalities during charging or discharging, ensuring that the battery remains protected.
The SCP functions as a fuse that physically disconnects circuits. When activated, it leaves a trace (history) of the shutoff, indicating that the battery experienced a problem or was at risk of posing a hazard. This trace does not disappear.
Another common battery protection device is the Field-Effect Transistor (FET), which, like the SCP, detects abnormalities and shuts off circuits. The primary difference from the SCP is that the FET electrically disconnects circuits, allowing them to recover once the abnormality is resolved.
Consider a scenario where the temperature of a battery pack increases abnormally. When this occurs, the FET will shut off the circuit. As current no longer flows through the circuit, the temperature gradually decreases below the abnormal threshold.
Once the abnormality resolves, the FET restores the circuit. Both shutoff and recovery are normal operations for the FET. Even if a cell is damaged, the FET will leave no trace (history) of having encountered an abnormality.
Let’s define new lithium-ion batteries (before being recycled or reused) as the first generation. Various electronic devices, including laptops, power tools, electric bikes, and drones, use these first-generation lithium-ion battery packs. When reusing first-generation battery packs equipped with SCPs, it can be assured that the constituent cells have not experienced any conditions that could severely deteriorate the batteries, such as overcharging or overdischarging, and pose a hazard.
The second generation of batteries comprises of reused batteries. The histories (backgrounds) of the constituent cells are crucial factors for ensuring safety. Consider a car, for example: from a safety perspective, it is risky to reuse critical components removed from a car with unknown accident and repair histories. When reusing components, understanding their backgrounds is essential.
For battery packs used in energy storage facilities, assuring safety is a priority. Reused lithium-ion batteries must be equipped with new protective devices. Additionally, there is significant potential in promoting the use of protective devices in first-generation batteries that may be reused after being decommissioned.
There are already several cases where Dexerials’ Self Control Protector (SCP) has been applied to reused lithium-ion battery packs. This trend is expected to grow. As the recycling process for lithium-ion batteries is established and batteries with recycled materials are introduced, it will be crucial to equip them with protective devices to ensure safety.
Going forward, Dexerials is committed to ensuring the safety of lithium-ion batteries, supporting battery market growth and broader applications, and thereby facilitating an affluent and sustainable society.
- SHARE