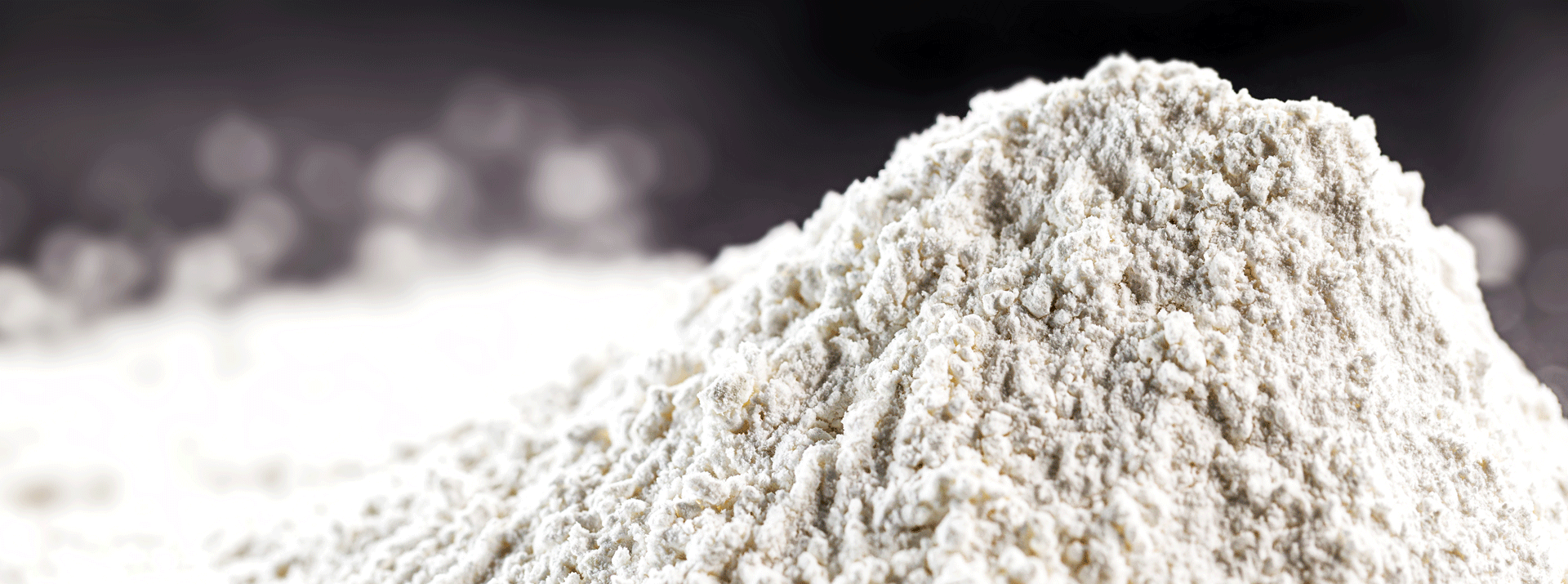
- 要素技術
スパッタリング用ターゲット材料の製造プロセス
目次
ターゲット材料の2つのタイプ
素材の表面に緻密な薄膜を形成する技術、スパッタリングでは、薄膜のもとになる材料として「ターゲット」と呼ばれる製品を使用します。この記事では、デクセリアルズが生産する各種のターゲットの製造プロセスについて説明します。
以下のイラストは、ターゲットの製造プロセスを示した流れ図です。ターゲットは大きく2種類に分かれます。1つはアルミニウムやチタン、銅などの金属材料から作られるタイプです。それらの元となる素材は、「ビレット」と呼ばれる長い棒のような状態で母材メーカーから納品されます。ビレットはプレス・圧延加工をされてから次の工程に進みます。
もう1つは、金属や酸化物、セラミックなどの原材料粉末から作られるタイプです。こちらは目的に合わせて、何種類かの材料粉末を一定の成分比率で混ぜ合わせ、板状に焼き固めてから加工を行います。デクセリアルズでは現在、こちらの焼結タイプのターゲット生産に力を入れています。
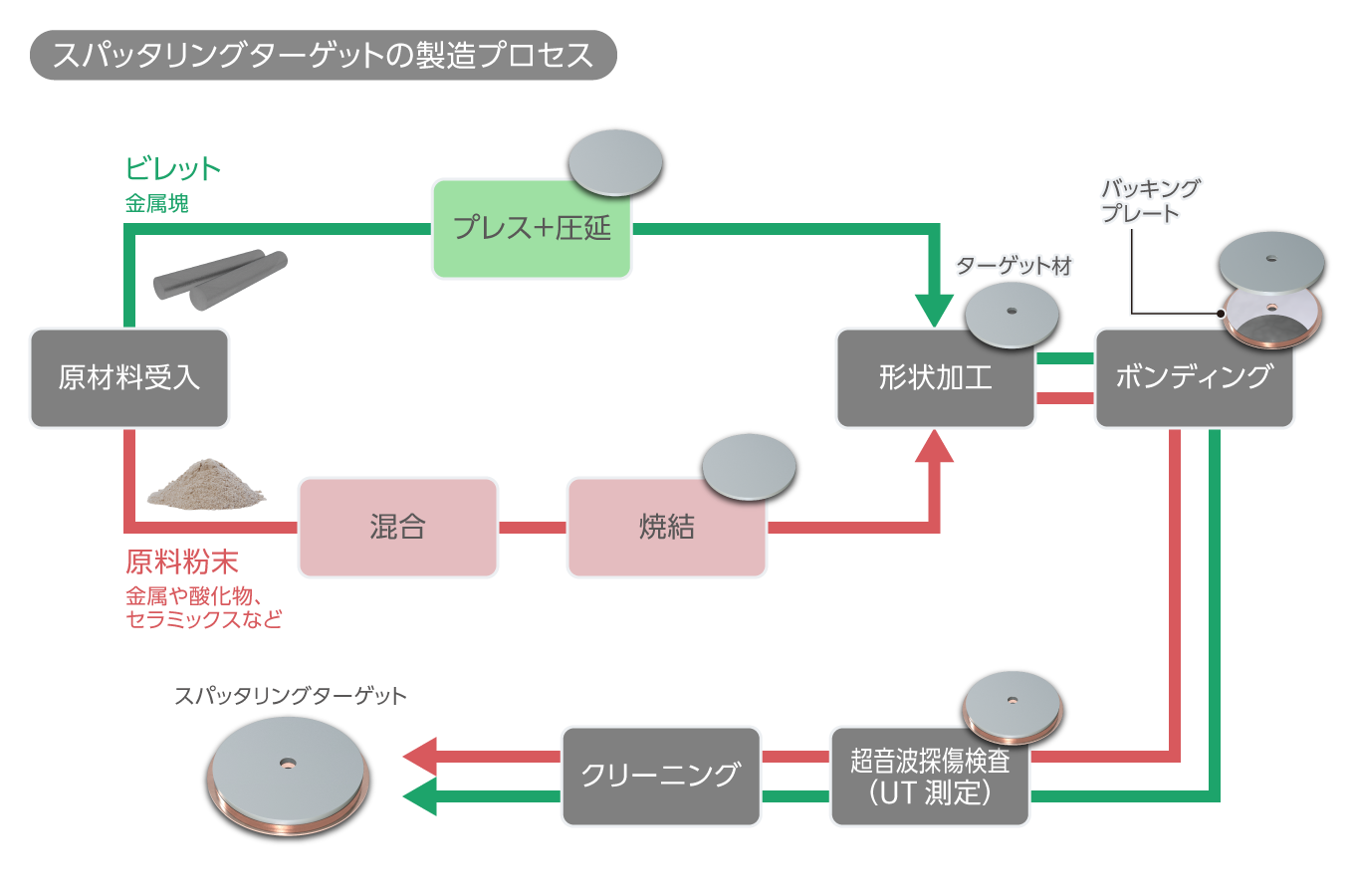
次に各工程のポイントについて解説します。
金属の結晶粒径を小さくする(プレス+圧延)
アルミなどの金属材料をターゲットへと加工するプロセスでは、まず初めにビレットを2000トンプレス機にかけて薄く平らにした後に、圧延機にかけて必要な直径まで広げます。
金属材料をターゲットに加工する上で気をつけなくてはならないのが、金属の結晶粒の大きさです。ビレットの状態のときは金属結晶の粒度は数ミリ程度と大きいのですが、圧延機で潰すことで結晶構造が破壊され不揃いになります。
その後、熱処理を行うと金属は再結晶化し、粒度の平均が10〜20ミクロン程度と小さくなります。特に半導体の回路製造で行われる膜処理では、ターゲットの結晶粒の粒度をできるだけ小さくする方が成膜中のダスト発生が抑えられることから、結晶粒度のコントロールが重要となります。
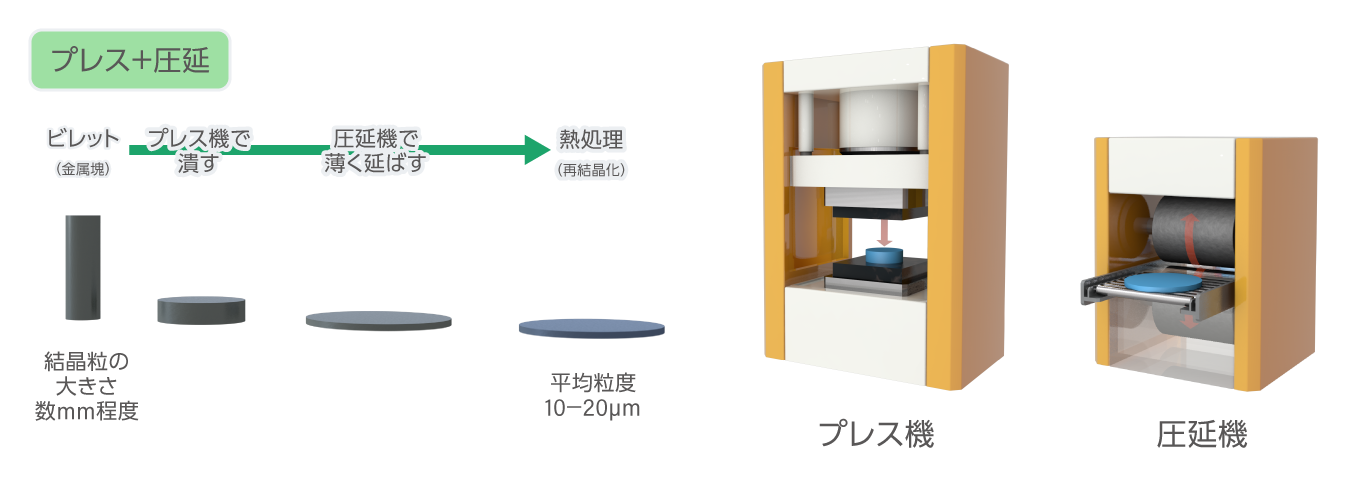
均一な粉末材料を得る(混合)
金属や酸化物、セラミックスなどの粉末材料から作られるターゲットでは、まず数種類の原材料の粉末を秤量してボールミルに入れて、回転させることで混合します。分散性をよくするとともに粉の粒度を揃えるために、ボールミルにはステンレスやジルコニアでできたボールを入れて回転させます。
混合には粉末が乾いた状態のまま混ぜる「乾式混合」と、アルコールなどの溶剤を入れて混ぜる「湿式混合」があり、材料物性(硬い、柔らかい)や粒度に合わせて適切な混合方式を採用します。湿式混合は混ぜたあとで乾かす工程が必要ですが、それに時間がかかると比重が重い物質が下に沈み、混ぜた材料同士が分離してしまうため、デクセリアルズは独自の技術で均一となるような工夫を行っています。混合のあとは、均一に材料が分散していることを確認するため、ICP発光分析装置で組成分析を行います。
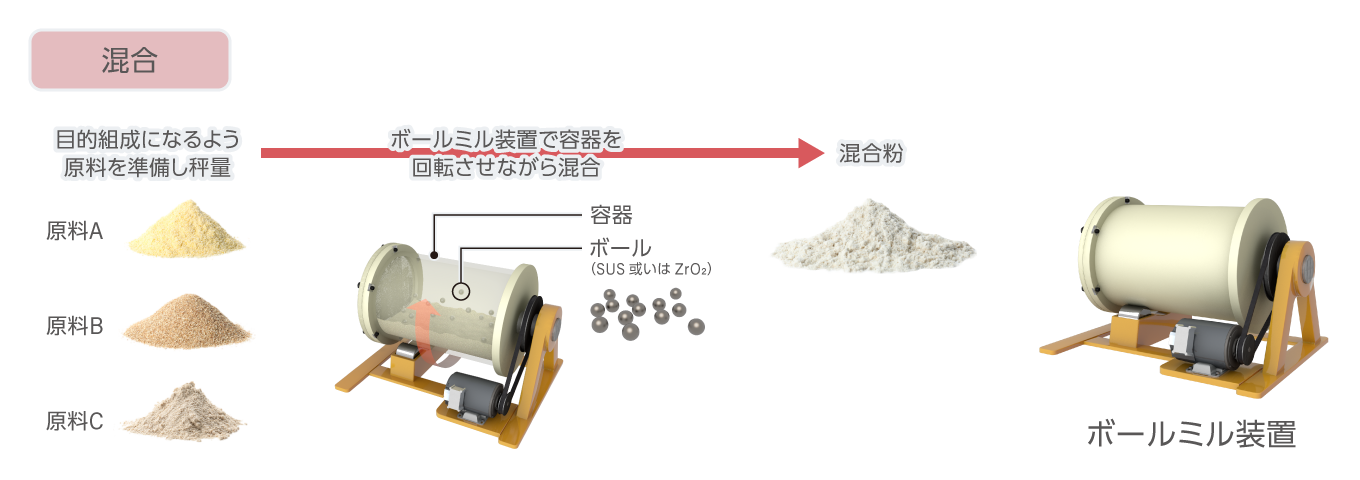
材料粉末を固める(焼結)
混合された粉末は、カーボン製の型に充填され、ホットプレス機を使って高温・高圧下で焼き固められます。原料の粉末は、低温で焼き固まるものもあれば、高温が必要なものもあり、焼結性は大きく変わります。また一定以上の温度になると溶けてしまう材料を、高温が必要な材料と組み合わせることもあります。
求められる製品を作るべく、原料の組成に合わせて最適な温度や圧力の条件を見出すことが重要となります。また材料に熱を加えることで反応し、結晶構造にも大きな変化が起こるため、それを見越した組成にする必要もあります。この組成や焼結条件に関するノウハウがデクセリアルズの大きな資産となっています。
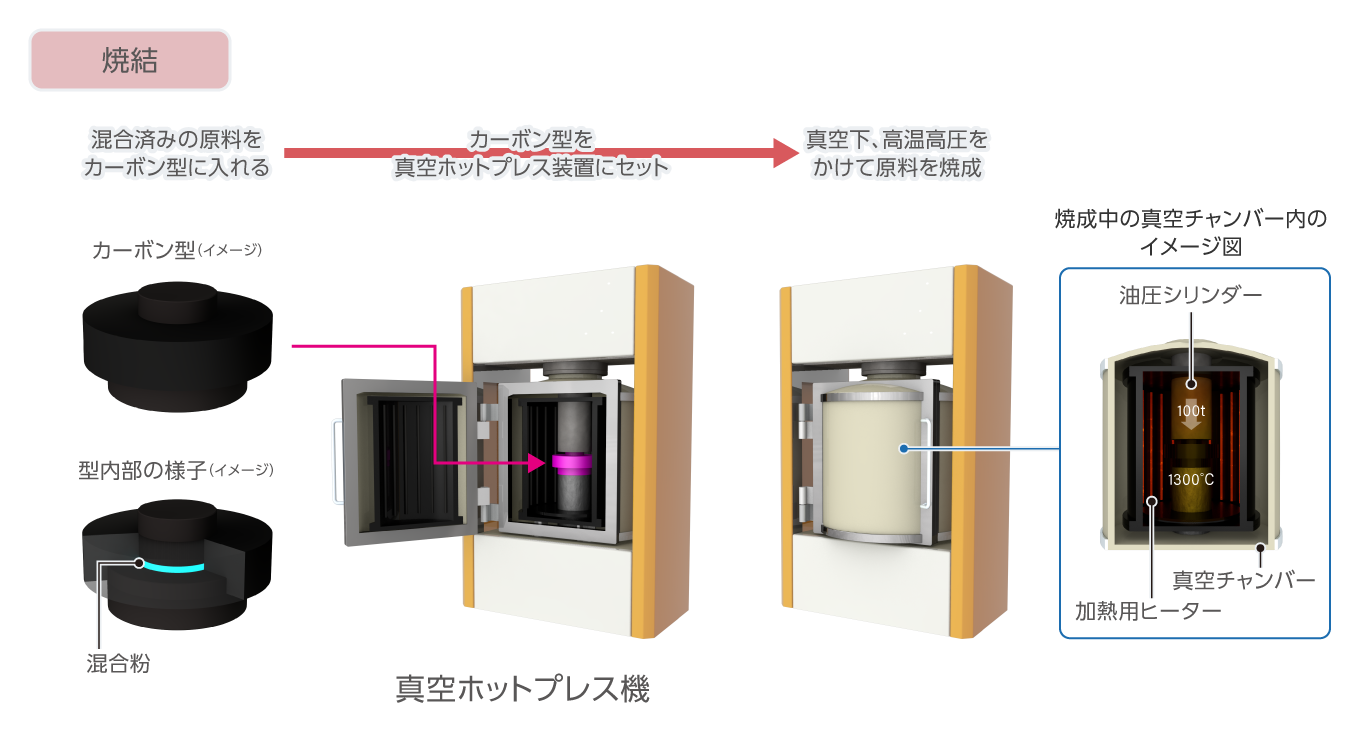
必要な形に整える(加工)
プレス・圧延や混合・焼結されたあとの素材の形は、ある程度整っていますが、細かく見るとかなりのバラツキがあります。そこで次の切削・研削工程で形を整えます。
ターゲット表面の状態が粗いままだと、スパッタリング時の放電に影響を与え、成膜が上手くいかないことがあるため、表面を削って整えます。金属材料から作られるターゲットは刃物による切削加工を行い、粉末材料から作られるターゲットは焼結した後で砥石を用いた研削加工を行います。材料は多種多様にあり、また硬軟、脆さなども製品ごとに違うため、加工もそれに合わせて最適な方法で実施します。
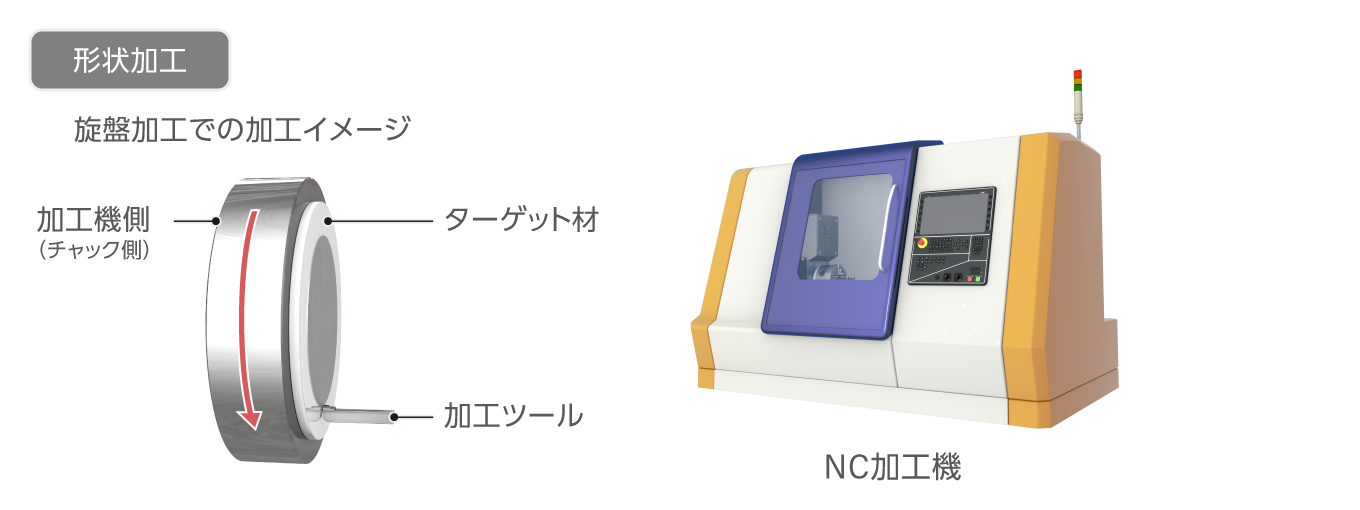
バッキングプレートに接合する(ボンディング)
ターゲット材はスパッタリング装置にセッティングがしやすいよう、バッキングプレートと呼ばれる板とはんだで接合(ボンディング)されて製品となります。ボンディングの材料は、以前は鉛を含んだはんだを使っていましたが、環境への影響から現在はインジウムに少量の錫を混ぜたはんだを使用しています。
ターゲットの上にインジウムはんだをそのまま垂らしても濡れにくく弾かれてしまうため、はんだ表面に超音波で微細な振動を与えることで濡れやすくし、接合加工を行います。超音波でははんだの濡れ性が良くならないターゲット材料の場合、ターゲットの接合面にニッケルメッキなどの接着層を成膜し、接合加工を行うこともあります。
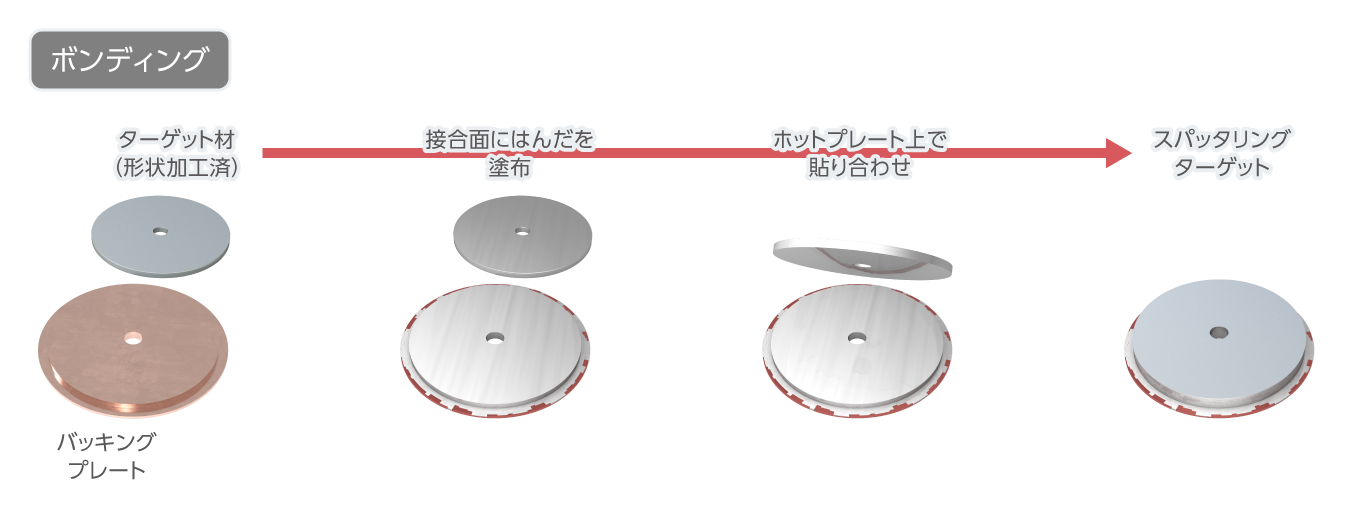
接合状態を確認する(UT測定)
ボンディングが終わったターゲットは、はんだで適切な状態で接合されているか、検査にかけられます。検査は水が張られた容器に沈められた材料に超音波を当て、その反射強度を画像化することで内部の状況がわかる超音波探傷(UT)装置を使います。はんだの内部に空気だまりが存在すると、超音波の反射強度が変わって、以下の写真のUT画像のように赤い場所が映し出されます。一定以上に赤い部分が含まれる製品はスパッタリング使用時にターゲットの冷却効率が悪化し、不具合が出る可能性があるため、不具合品として取り除かれます。
こちらの検査も、材料が多種多様に存在するため、検査条件を材料毎に最適化することが必要です。こうした数々の工程と検査をクリアしたターゲット材のみが、最終的にクリーニングで汚れを除去された後に製品として出荷されます。ターゲット材の製造には、各工程で高度なノウハウが必要であり、長年にわたる経験で培ってきた知見をもとにお客さまのご要望にお応えしています。
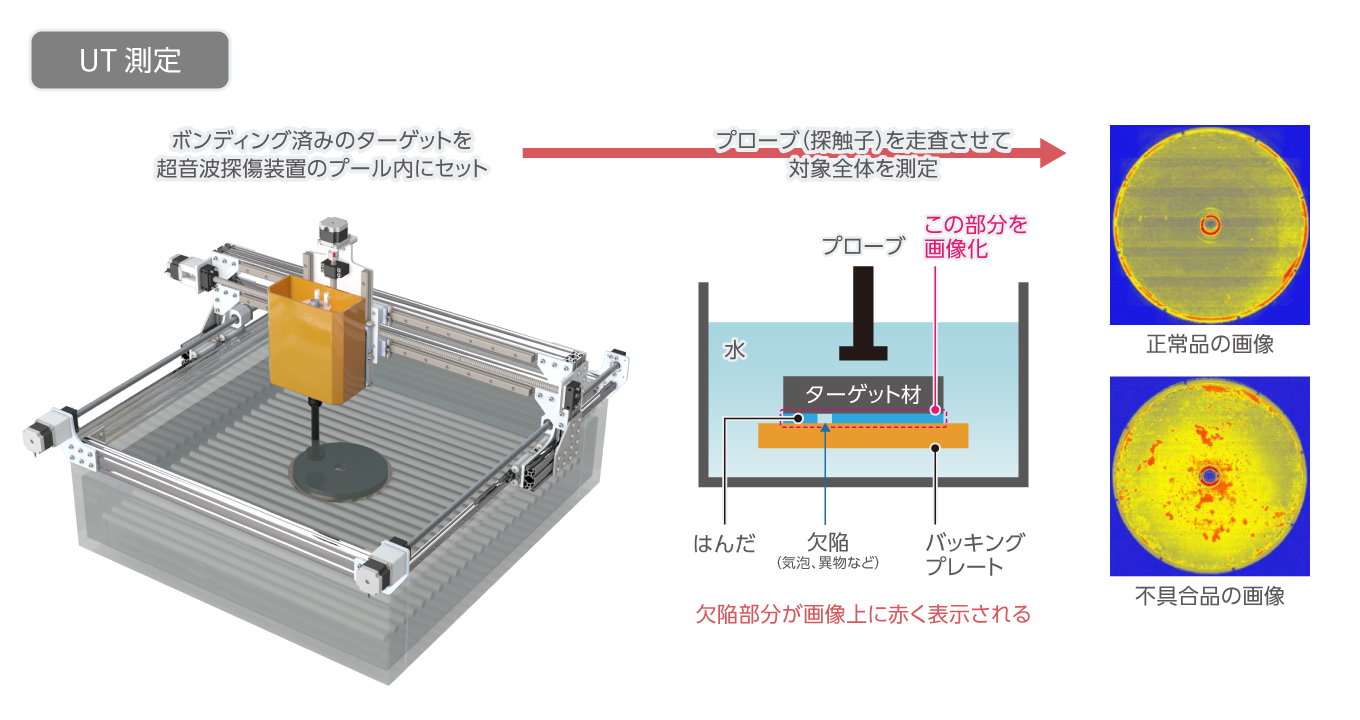
関連記事
- SHARE
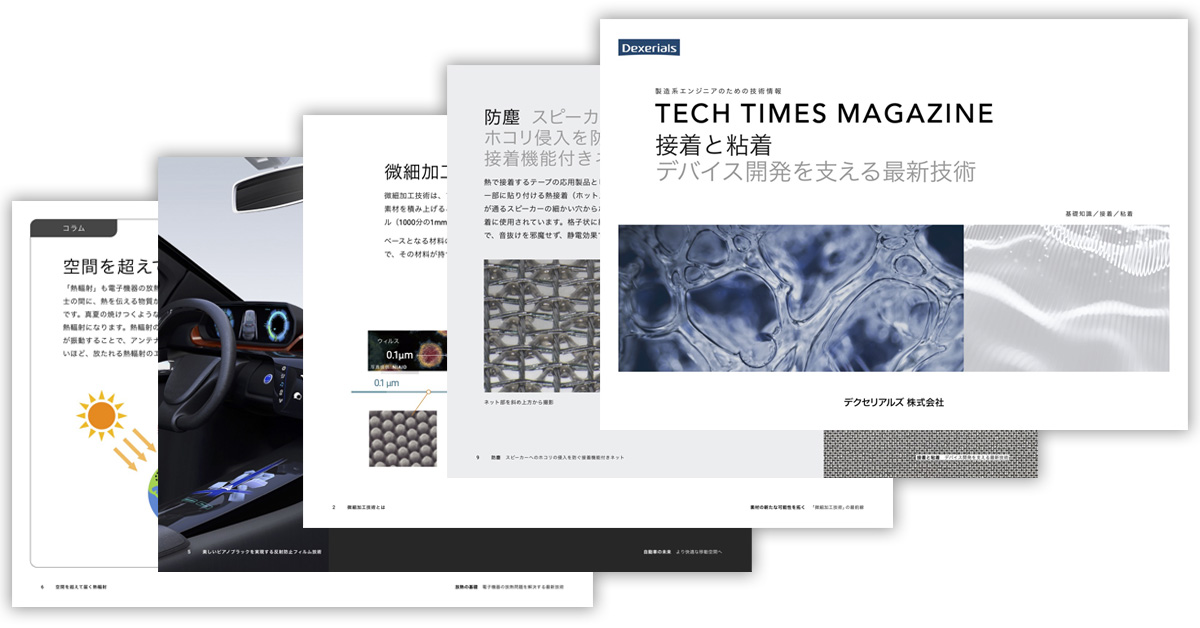
当社の製品や製造技術に関する資料をご用意しています。
無料でお気軽にダウンロードいただけます。
お役立ち資料のダウンロードはこちら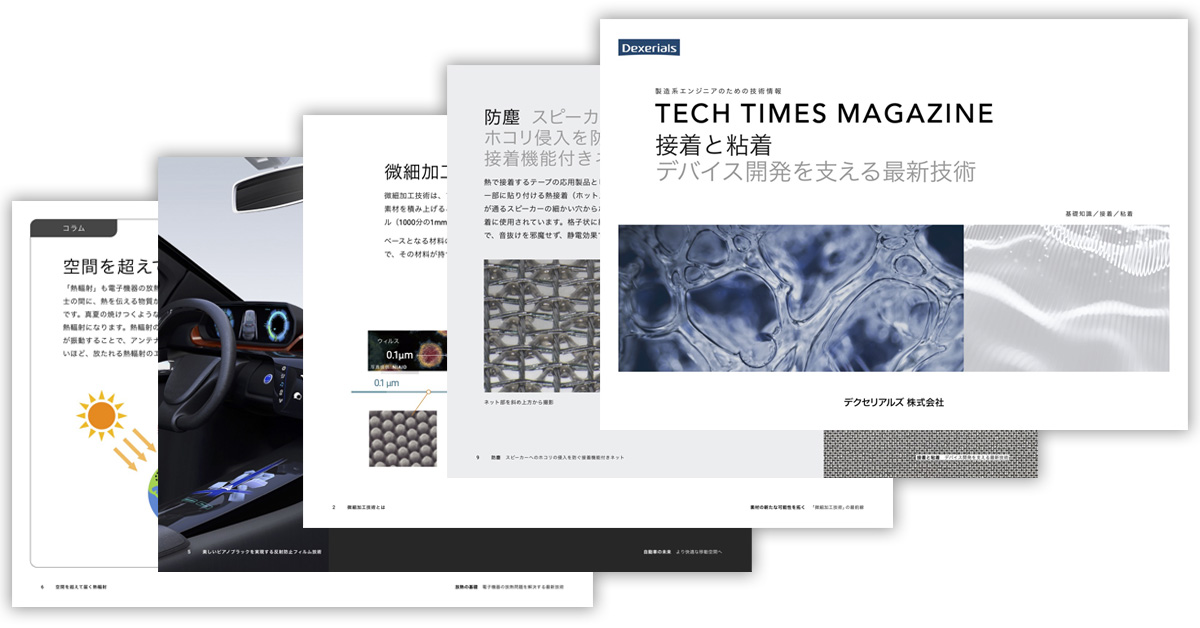
当社の製品や製造技術に関する資料をご用意しています。
無料でお気軽にダウンロードいただけます。
お役立ち資料のダウンロードはこちら