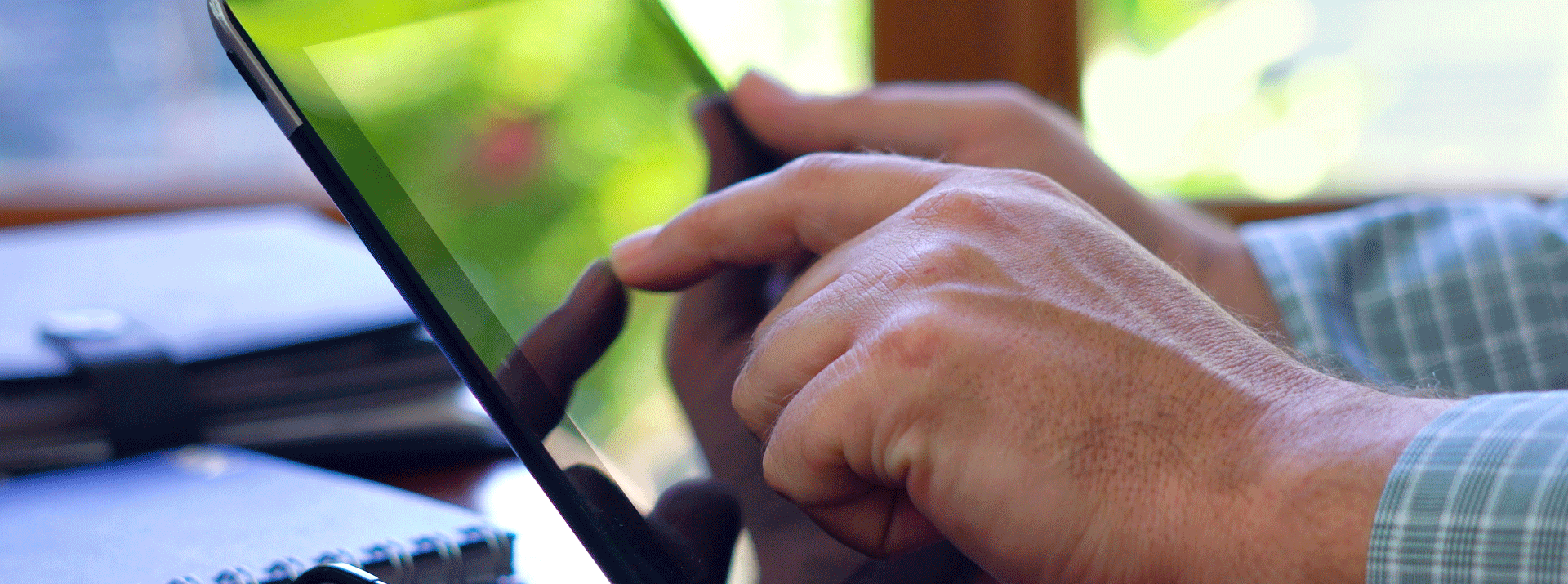
- 光学関連
耐久性が40倍以上に!反射防止フィルムの新技術とは
圧倒的な耐久性を実現した「ARフィルム HDシリーズ」
デクセリアルズは2020年7月、最表面の防汚層を真空蒸着法で形成することにより、耐久性を当社従来品よりも40倍以上に向上させた反射防止フィルム「ARフィルム HDシリーズ」を開発しました。はじめに、その開発の背景をご説明します。
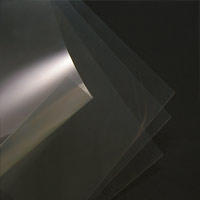
デクセリアルズの反射防止フィルムは、スパッタリング技術によって金属酸化膜をナノ単位の精度で表面に形成することで、ディスプレイに貼ることで優れた低反射性能を実現する製品です。大手メーカーのノートPCや多くの車載ディスプレイに採用されており、その表面には指紋や汚れをつきにくくし、容易に拭き取れるようにフッ素系樹脂を用いた防汚層を設けています。
防汚層に求められる重要な機能の一つが、「こする力」に耐えることを意味する「耐摺動性」です。スマートフォンやタッチパネルを搭載したノートPC、タブレットPCでは、ディスプレイを指やスタイラスペンで頻繁にタッチしたり擦ったりします。その度に表面の反射防止フィルムには摩擦による力が加わり、目に見えない小さなこすれ傷が発生することがあります。その傷が重なっていくと、防汚層が劣化して指紋がつきやすくなったり、反射防止フィルム層まで削られて視認性が悪くなる可能性があります。
また、ノートPCの軽量化や薄型化を図るために最近では、カバーガラスを反射防止フィルムで代替する製品や、車載ディスプレイのより一層の高耐久性を実現したいというお客さまのニーズも増えています。こうした背景から、反射防止フィルムの防汚層の耐久性をさらに向上させることが必要となり、デクセリアルズでは研究開発を進めてまいりました。
「ウェット工法」による防汚層形成の課題
従来のデクセリアルズの反射防止フィルムは、「ウェット工法」と呼ばれる方式で最表面の防汚層を形成していました。以下はその模式図です。
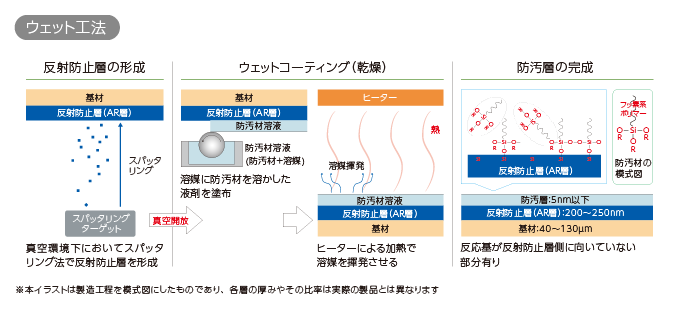
反射防止フィルムの防汚層を形成する防汚材はフッ素系樹脂が材料です。ウェット工法では、反射防止層を形成した基材の表面に防汚剤を溶かした溶液を塗布し、ヒーターによる加熱で溶媒を揮発させることで、防汚層を形成します。
防汚剤は反射防止層の表面にあるシリコンの反応基と、防汚剤を構成するフッ素系樹脂のポリマーが、「シロキサン結合」と呼ばれるガラスや石英の分子構造と同様の強い化学結合で結びつくことで、高い耐摺動性を発揮します。
しかしウェット工法には、原理的に解決が難しい課題がありました。上の図の右はウェット工法で形成された防汚層をミクロの目で見た模式図ですが、液体を塗布するという工法上、防汚剤の反応基が反射防止層側のシリコン側に向かず、どうしてもうまく結びつかない部分が発生してしまうのです。
防汚層の強度を飛躍的に高めた「真空蒸着法」
それに対して、今回デクセリアルズが新たに開発した技術では、防汚層を「真空蒸着法」と呼ばれる方法で反射防止層の上に形成します。下記がその工法の模式図です。

真空蒸着法に使う防汚層の材料は、ウェット工法と同じフッ素系樹脂ですが、それを塗布するのではなく、高温に加熱して気化することで、表面に蒸着させます。表面に余計な分子が入り込まないよう、蒸着は真空が保たれたチャンバー内で行われます。この方法をとることにより、反応基が反射防止層側へ向き、かつ均一に配列することで、ウェット工法よりも緻密で強固な結合が可能になります。
今回新たに開発した防汚層を持つ反射防止フィルムは、反射率0.5%以下、透過率95%以上という従来品の優れた光学特性はそのままに、防汚層は非常になめらかな低摩擦の物性を実現。摺動耐久性も従来品に比べて40倍以上、向上しています。
耐摺動性試験で優れた性能を実証
以下は、真空蒸着法によって製造された「ARフィルム HDシリーズ」と、ウェット工法による従来品に対して耐摺動性試験を行った結果のグラフです。試験では不織布製のワイパーで表面を何度もこすり、表面についた水滴の接触角を観察しました。

従来品は摺動回数が500回を超えると水接触角が100°未満になり、2000回を超えたあたりで90°以下まで低下しています。これはつまり、表面についた水が広がり、汚れがつきやすくなることを示しています。それに対して真空蒸着法によって作られた製品は、初期の水接触角120°を実現し、かつ摺動回数が20,000回を超えても110°を維持しており、水を弾きやすく汚れがつきにくいことがわかります。
デクセリアルズではこの新しく開発した「ARフィルム HDシリーズ」を、2021年春に量産体制を整え、販売を開始していく予定です。コロナ禍によってリモートワークが一般的になった現在、タッチパネルを用いたPCやタブレットPCの供給およびその使用機会は以前よりもさらに増大しています。当社では、今回開発した「ARフィルム HDシリーズ」でこのトレンドに応えられると考えております。私たちはこれからも、世の中の変化に対応した製品の開発を続けてまいります。
関連記事
- SHARE
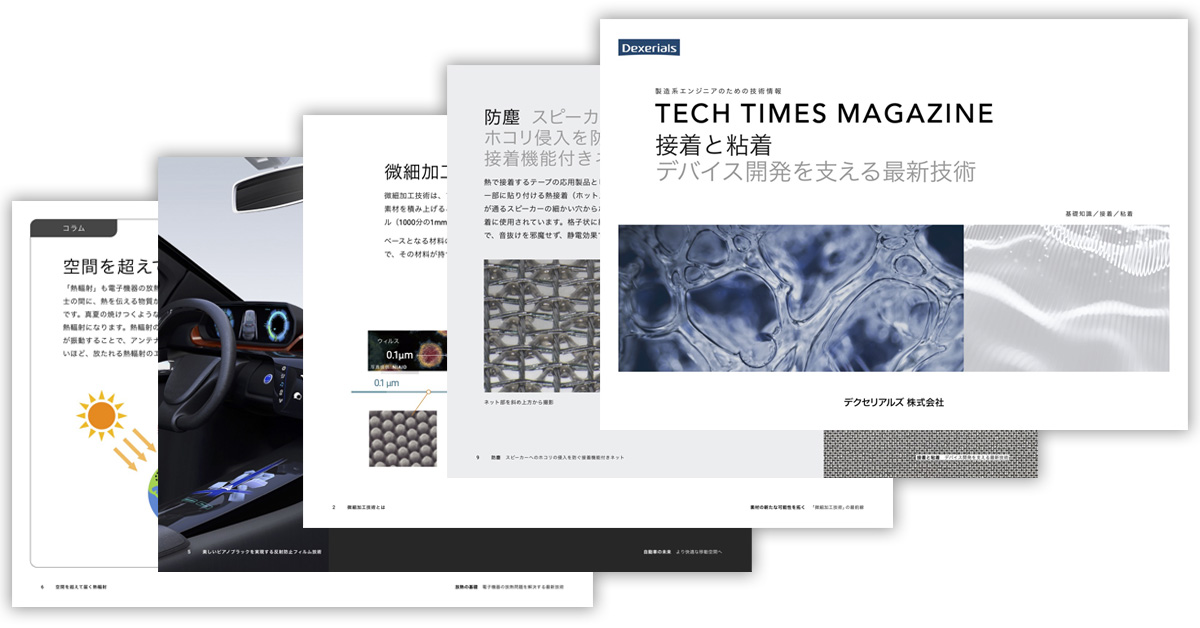
当社の製品や製造技術に関する資料をご用意しています。
無料でお気軽にダウンロードいただけます。
お役立ち資料のダウンロードはこちら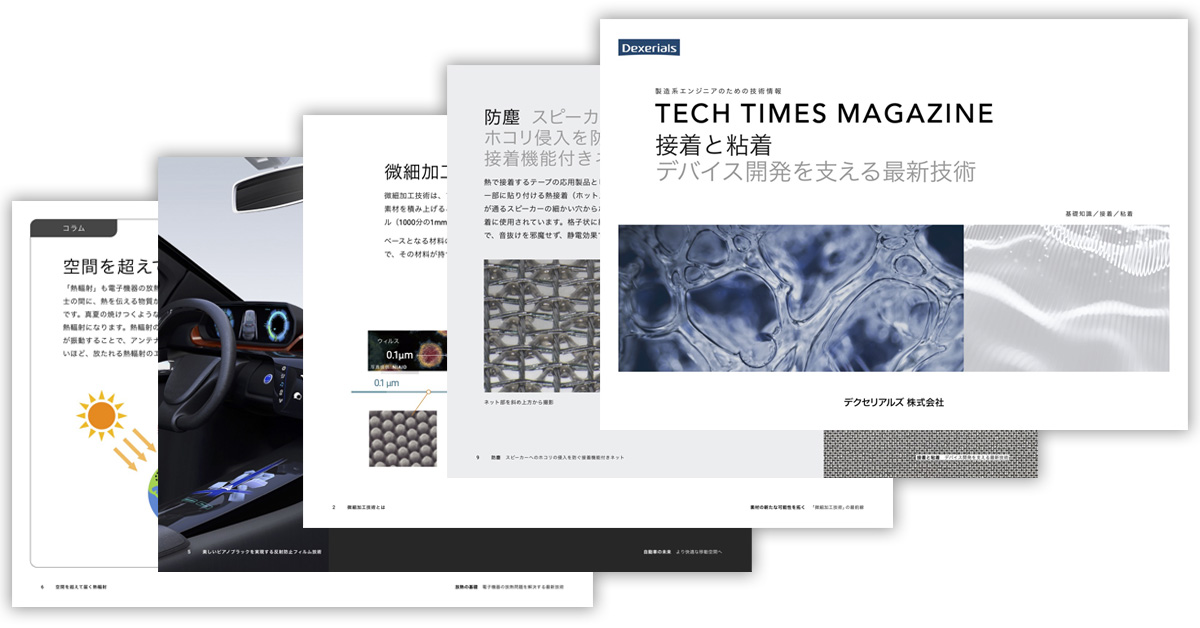
当社の製品や製造技術に関する資料をご用意しています。
無料でお気軽にダウンロードいただけます。
お役立ち資料のダウンロードはこちら