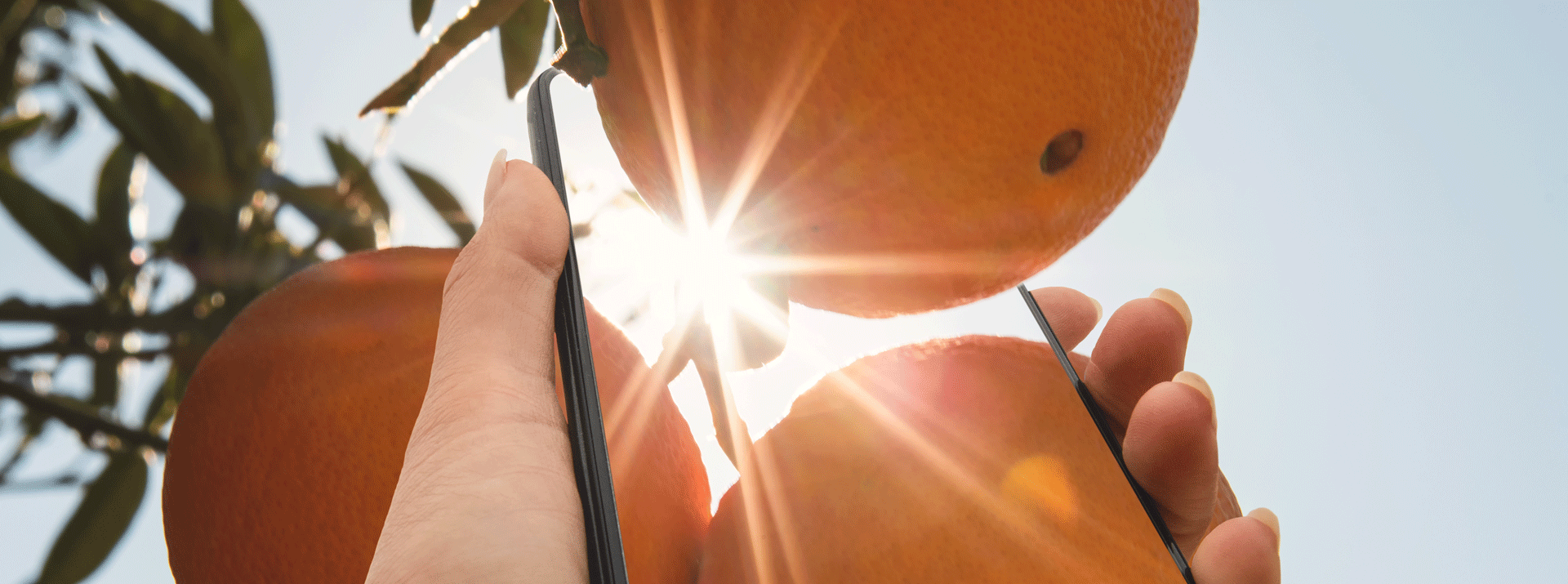
- Optical Products
Head out with your phone! Weather-resistant anti-reflection film
Contents
- 1 The structure of anti-reflection film and the role of each component
- 2 Demand for weather-resistant film increases with the spread of mobile devices
- 3 Two methods to strengthen adhesion between inorganic and organic materials
- 4 Greater ‘anchoring effect’ by roughening the surface by tenfold
- 5 Significantly improved weather resistance of anti-reflection film
The structure of anti-reflection film and the role of each component
Anti-reflection film is a material that can be applied to laptops, monitors, and TVs to prevent screen glare and improve visibility. As shown in the illustration below, its structure is divided into the following components: an anti-smudge layer to make it easy to wipe off fingerprints and other smudges, an anti-reflection layer to reduce the reflection of outside light, a hard coat layer to protect the film from scratches, a base film to support the film, and an adhesive layer to be able to apply the film to a substrate.
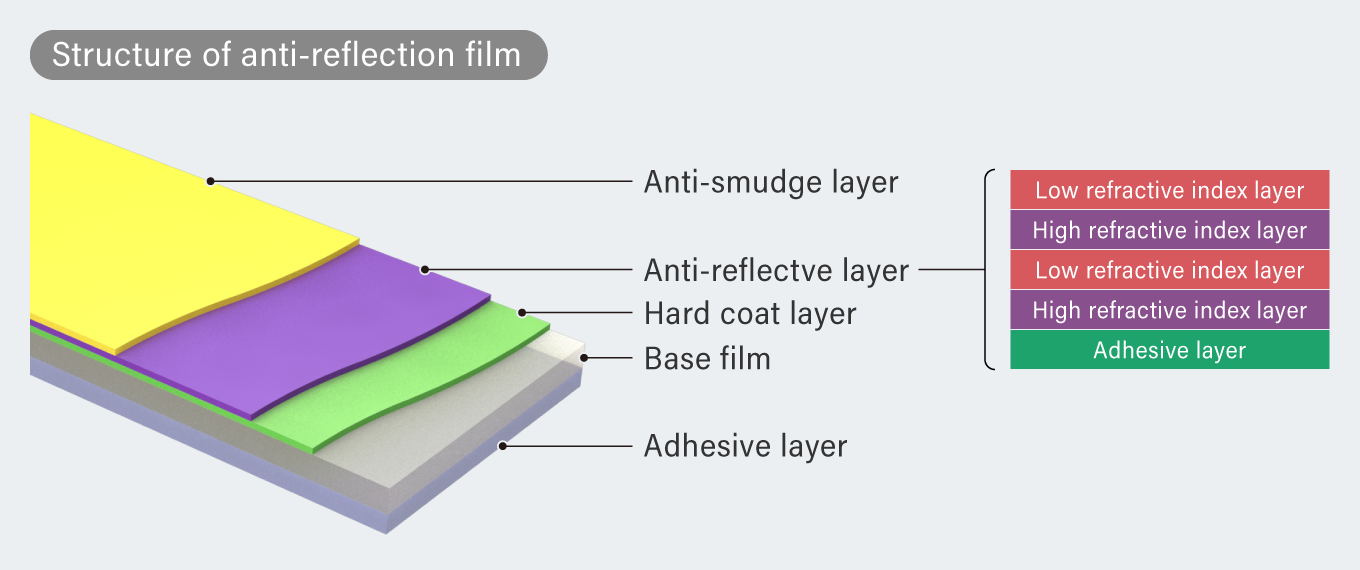
Demand for weather-resistant film increases with the spread of mobile devices
With the advent of smartphones and tablets, weather-resistant anti-reflection film has become more important than ever. Compared to PC monitors that are typically used indoors, smartphones and tablets, as well as displays used in car navigation systems and cluster panels, are frequently exposed to sunlight.
One may notice deteriorated plastic bottles on the beach due to prolonged exposure to sunlight. Since some layers of anti-reflection film also contain organic materials, they deteriorate at the nanoscopic level when exposed to strong ultraviolet rays, causing delamination. For this reason, Dexerials has been developing an anti-reflection film with greater weather resistance capabilities.
The interface of anti-reflection film that peels off due to ultraviolet rays is located between the anti-reflection layer made of inorganic material and the hard coat layer made of organic material. Inorganic and organic materials are naturally difficult to stick to each other due to their different physical properties. In the past, it was not necessary to have strong adhesion of the film for devices intended for indoor use as long as they could withstand soft natural light or indirect lighting. However, this is not the case with mobile devices used outdoors. Even when exposed to strong midsummer rays, the inorganic and organic layers must be able to sustain adhesion.
Two methods to strengthen adhesion between inorganic and organic materials
As mentioned above, the two layers delaminate when exposed to ultraviolet rays due to the deterioration of the adhesive between the organic and inorganic material. One solution to improve adhesion is to add silica filler, an inorganic material, to the organic material. The other solution is to roughen the surface of the hard coat layer to make it physically more adherent.
Unlike organic substances, inorganic substances like glass are largely unaffected by sunlight. In addition, inorganic substances can bond to other inorganic materials easily and for a long period of time. Below is a diagram comparing a conventional bond between an anti-reflection layer and hard coat layer (left) and Dexerials’ bonding technology for greater weather resistance (right).
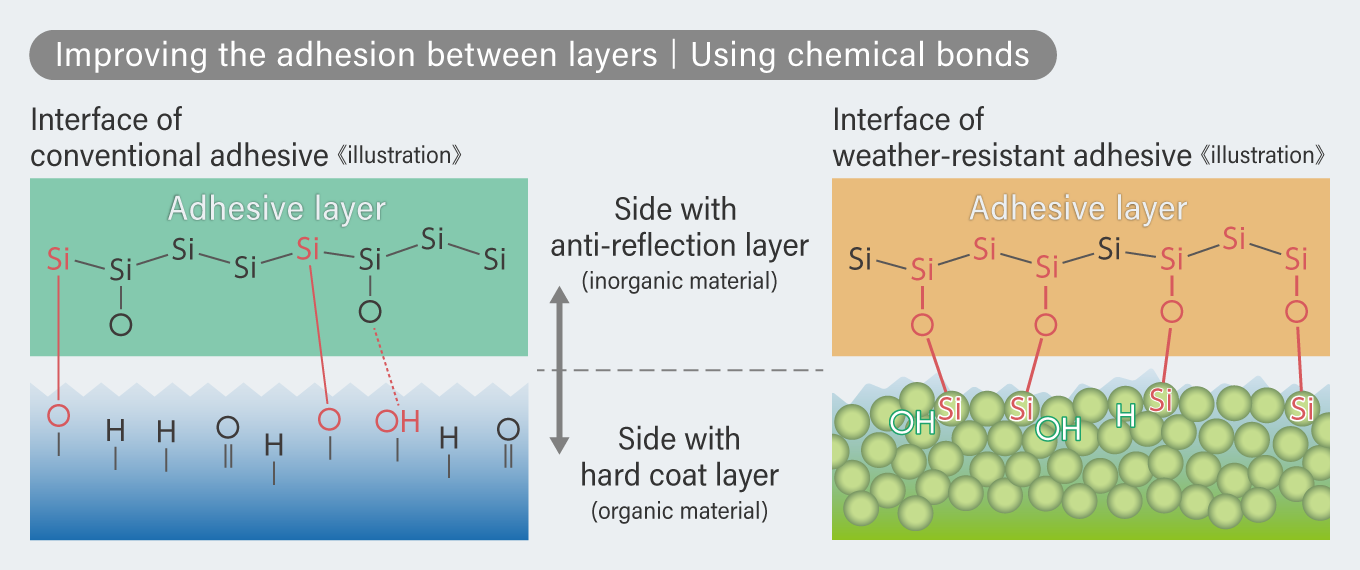
On the left, only part of the silicon (inorganic material) in the anti-reflection layer is bonded to the oxygen in the hard coat layer made of resin (organic material). On the right, however, through strong bonds called ‘siloxane bonds,’ the silicon, carbon, and oxygen are tightly bonded to the silicon in the anti-reflection layer due to the resin’s filler. Each silica filler embedded in the resin is several tens of nm in size and must be well-aligned with the surface of the resin in order to bond with the silicon on the side with the anti-reflection layer. Dexerials has independently established and patented the nanoscale control of this process. (Japan: Patent No. 6207679, Patent No. 2016-128927, Patent No. 2016-2244443. US: US10752808)
Greater ‘anchoring effect’ by roughening the surface by tenfold
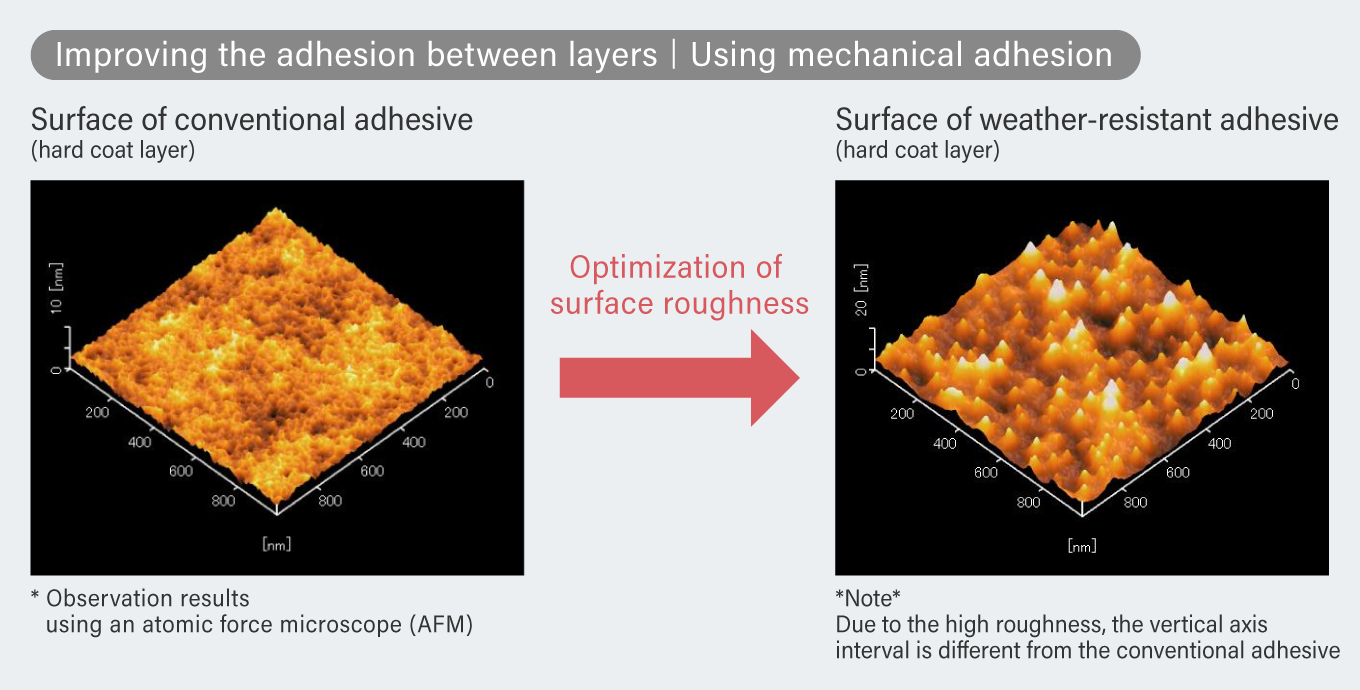
Another method that strengthens the adhesion between inorganic and organic layers is the use of a mechanical bonding due to surface structure called the ‘anchoring effect’. The photo above shows the surface of a conventional hard coat layer (left) and a weather-resistant layer (right) taken with an atomic force microscope, which can view materials at a nanoscopic level. The surface on the right is more uneven with wider spaces between peaks than that on the left.
When the surface is rough, the uneven surfaces connect to each other like an anchor. This anchoring effect is even greater when the surface is rough rather than smooth. Dexerials has succeeded in enhancing the anchoring effect by making the roughness of the hard coat layer ten times than that of conventional hard coats. If the bumps are made too rugged, however, the film loses transparency and becomes off-white. Therefore, Dexerials’ unique technology creates an optimal anchoring effect while also retaining transparency.
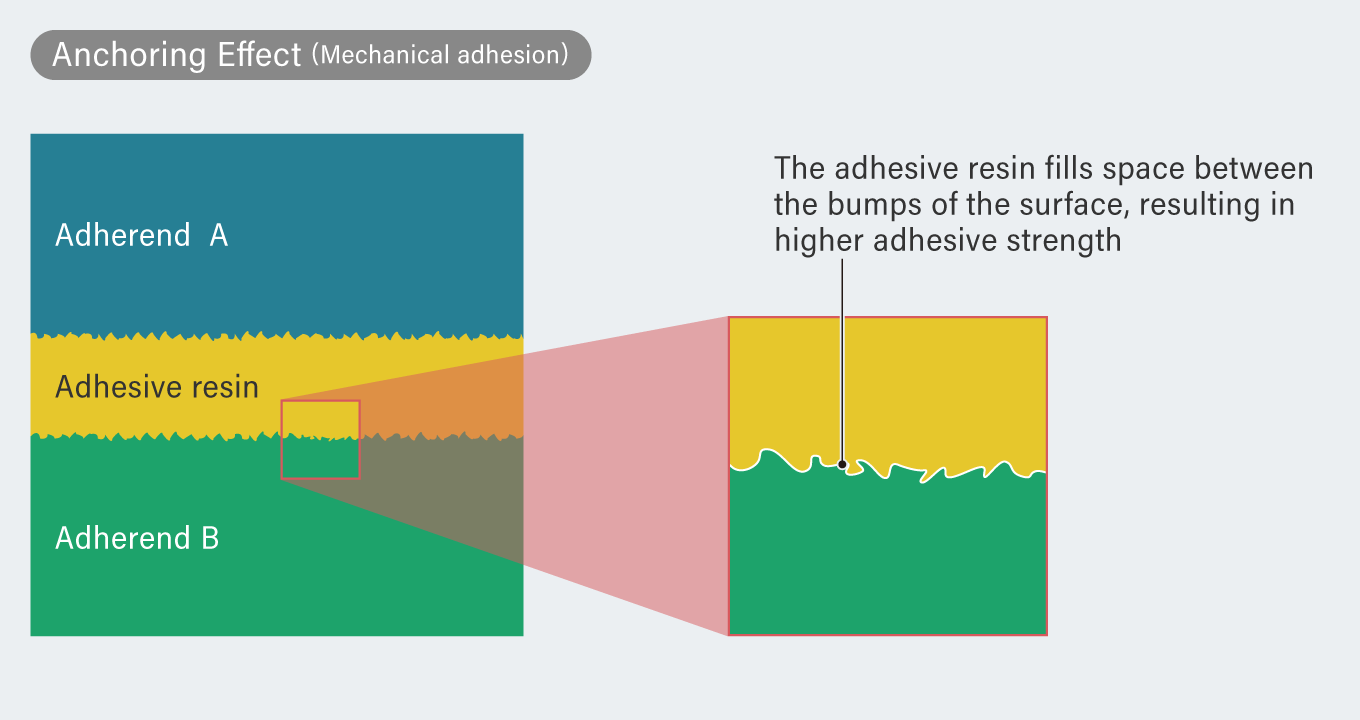
Significantly improved weather resistance of anti-reflection film
The two methods described above have greatly improved the weather resistance of anti-reflection film. Below are the results of a test in which conventional and new anti-reflection films were exposed to ultraviolet rays for a prolonged period of time (several hundred hours), and then wiped with a non-woven cloth to see if any delamination occurred. While the conventional film peeled off, the weather-resistant film did not.
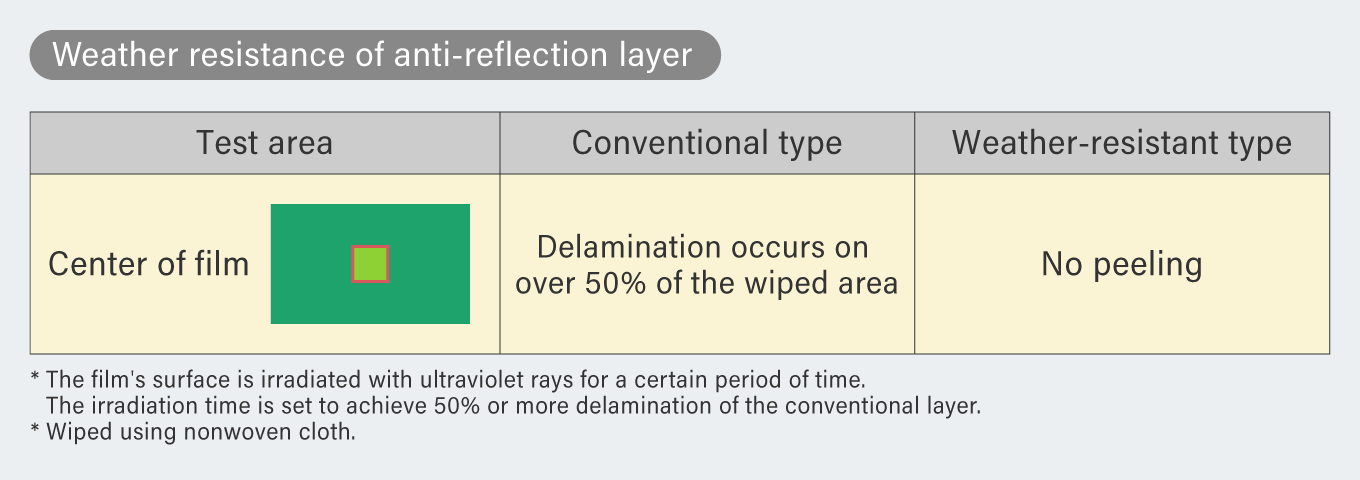
The technology outlined in this article is also used for manufacturing of anti-reflection films for digital camera LCD screens designed for outdoor use. Dexerials’ will continue developing films that can withstand a variety of applications in different environment.
- SHARE