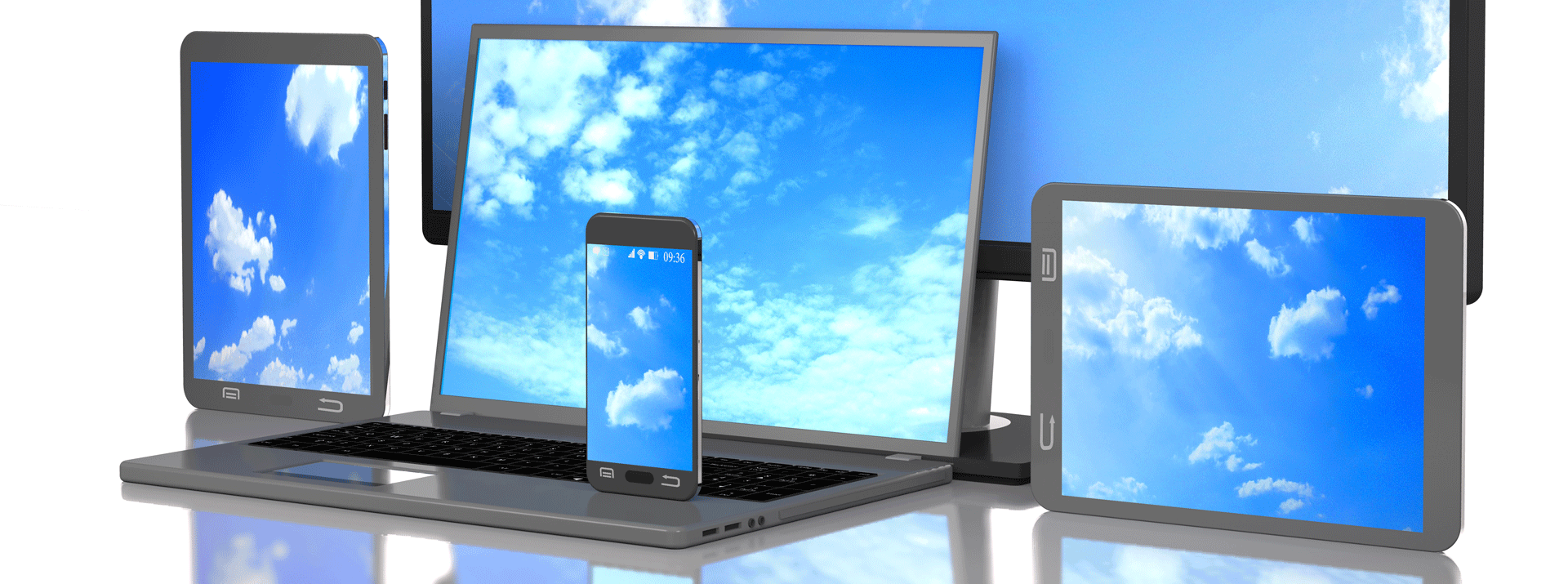
- Optical Products
Optical Bonding Processes for SVR (Optical Elastic Resin) Application
Contents
The importance of selecting the appropriate SVR
Dexerials’ Optical Elastic Resins (SVRs) and Hybrid Optical Elastic Resins (HSVRs) fill the air gap between substrates (e.g. top plate and display module) to reduce glare and improve screen visibility. They are used in a variety of electronics products, including smartphones, camera LCD screens, tablets, and large-screen TVs. Recently, they have also been utilized in automotive in-vehicle displays. As the applications of SVRs continue to expand, it is important to note that the application of SVR depends on the two bonded substrate materials (adherents). The table below explains details.
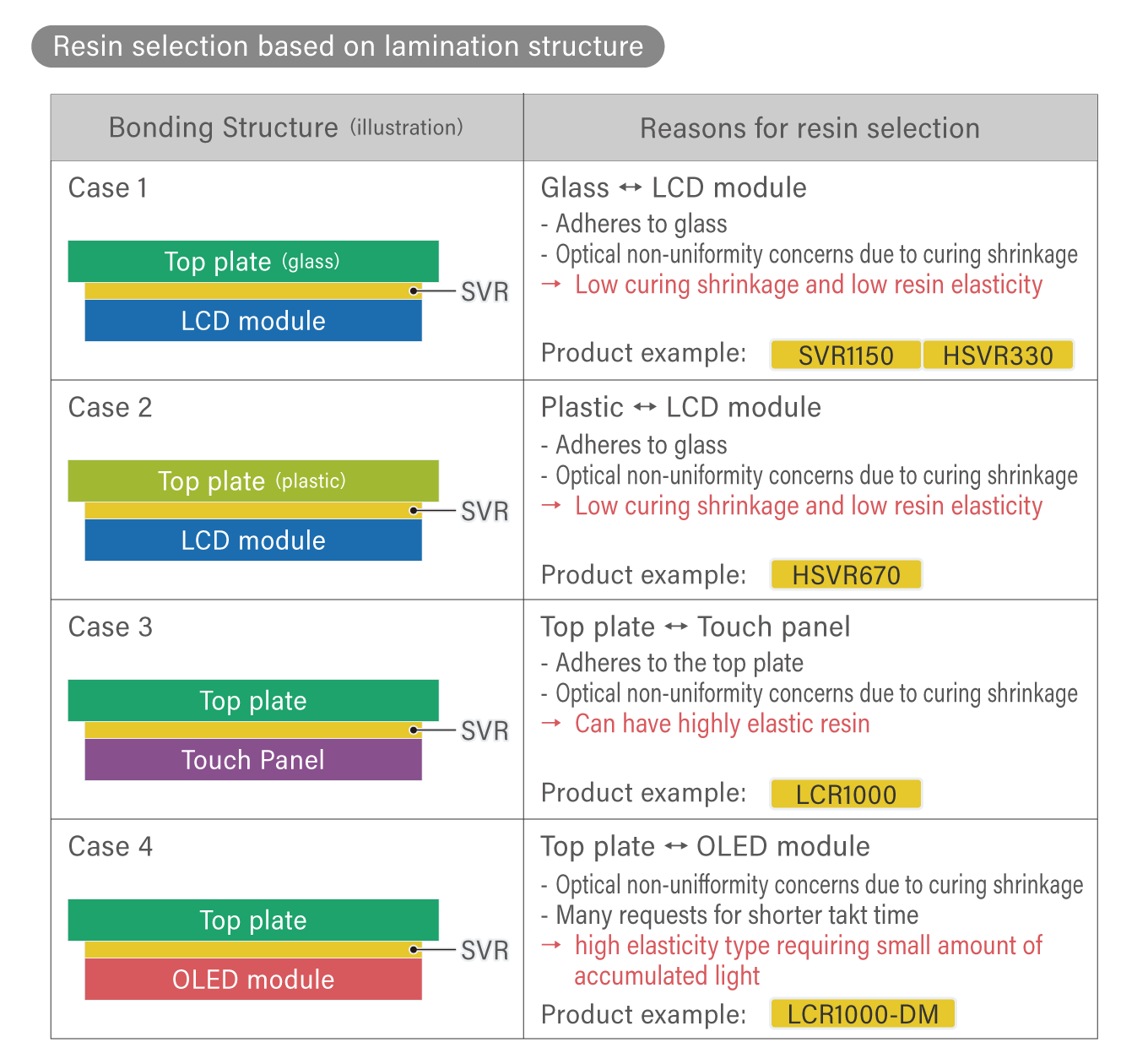
When selecting the appropriate SVR, the bonded substrates could be the following:
- Substrate #1: Top plate (glass or plastic)
- Substrate #2: Liquid crystal display (LCD) module, a touch panel, or an organic light emitting diode (OLED) module
It is also important to select SVRs considering properties including but not limited to, the shrinkage and elasticity during curing, and the amount of UV irradiation required for curing. Furthermore, the amount of labor (hours) and the process cost can affect the choice.
There are several methods for bonding top plates with display modules. Which method to choose depends on product specifications, equipment used for bonding, processes, and desired production efficiency. Below describes three typical SVR and hybrid SVR bonding processes
(1) The Dispense-and-Flip Bonding Method
The first is the most conventional method of bonding, called dispense-and-flip bonding. The steps are explained and shown in the below diagram.
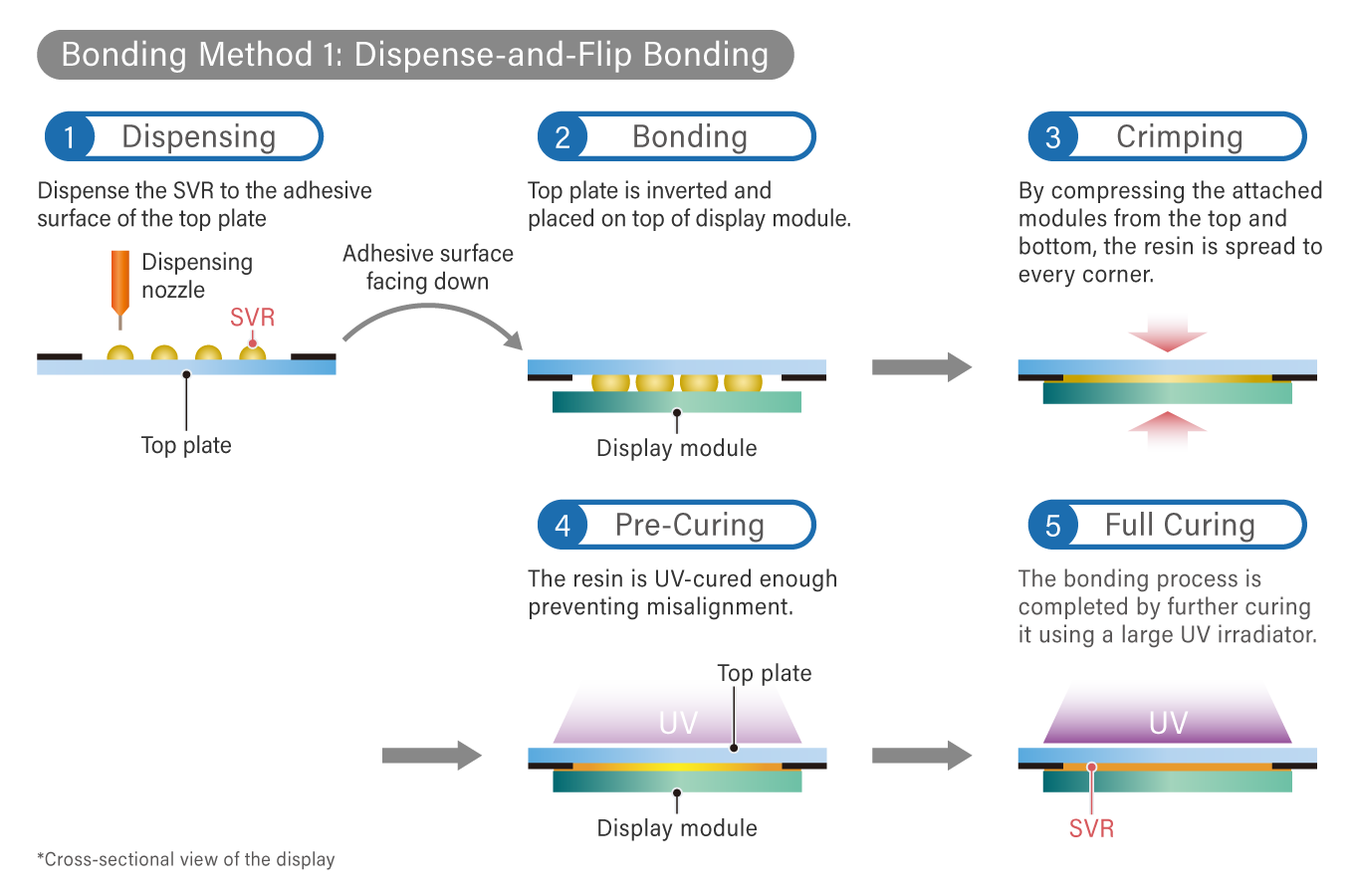
Step 1: Dispensing resin
Dispense the SVR on the bonding surface of the top plate (glass or plastic). To prevent the resin from overflow, a dam can be applied around the perimeter in advance.
Step 2: Bonding
Flip over the top plate with the SVR coating. Attach the plate to the display module with the SVR side facing down.
Step 3: Crimping
Compressing the attached modules from the top and bottom, the liquid SVR is spread to every corner of the adhesive surface.
Step 4: Pre-curing
The resin is pre-cured by exposing ultraviolet (UV) light from the top, sides or back of the module. This process prevents the module’s adhered surfaces from misalignment and enables a smooth transition to the main curing process in step 5.
Step 5: Full curing
During the full curing step, the modules are lined up on a conveyor belt UV irradiation machine and irradiated with UV light. The bonding process is now complete.
The Development and Advantages of Dispense-and-Flip Bonding
The advantage of this method is preventing formation of air bubbles in the resin. Below is a diagram of a top plate and display module with dispensed SVR. The liquid SVR applied to the top plate drips down from a single point due its own weight, as shown in the illustration. The SVR in contact with the module spreads outward from that single point, preventing formation of air bubbles. If the SVR side is placed upright, the surface of the applied resin will be slightly uneven. When the module is then placed over it, the air between the substrate and the resin surface will get trapped causing optical defects and potential delamination.
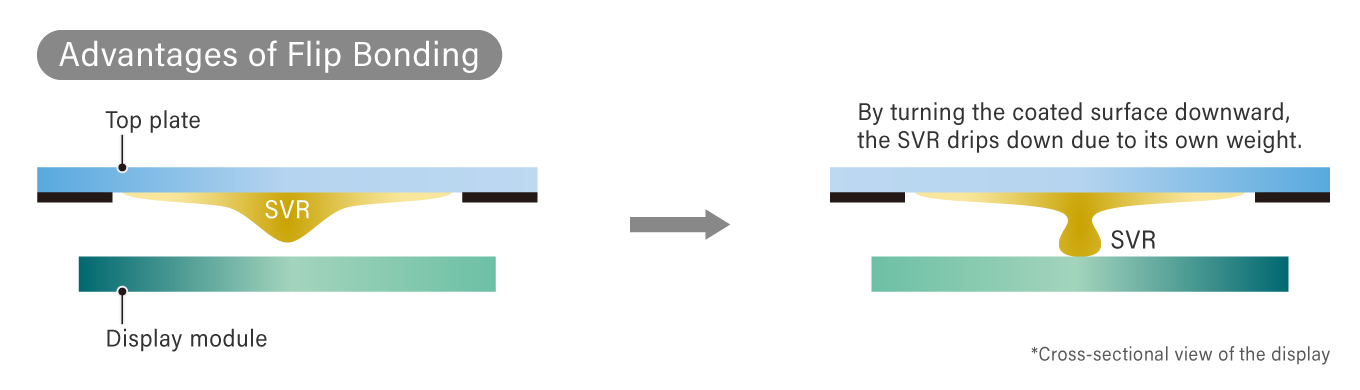
Air bubbles were the major issue in optical lamination. It was a coincidence that led to the discovery of this method when a mistake was made during an experiment. A glass plate coated with SVR slipped from the researcher’s hand and fell backwards onto a panel that happened to be underneath. It was then discovered that there were no air bubbles in the glass, and the SVR spread out evenly. This accidental discovery led Dexerials to establish and patent the SVR process that prevents air bubbles, and to successfully launch the product in 2007.
(2) The Hybrid SVR (HSVR) Method
Next is the bonding process using a product called the hybrid SVR (HSVR), an improved version of SVR. The dispense-and-flip bonding technique described above involves applying liquid SVR with a dispenser followed by UV curing. This causes the liquid to overflow at the edge of the bonding surface when it is crimped, which sometimes requires an extra step to remove the overflow after the UV curing process. Recently, the narrow bezel trend in smartphone design requires a tighter control of resin overflow.
To solve the overflow problem, Dexerials developed a product called hybrid SVR (HSVR). The HSVR is first applied to the surface of a top plate using a slit coater.
Once applied, the HSVR achieves 60-80% curing rate after UV pre-curing process. The resin hardens to the extent that there is no overflow at the edge of the panel. This method creates a “double-sided tape” on the top plate to adhere it to the display panel. Below is a diagram of the HSVR method.
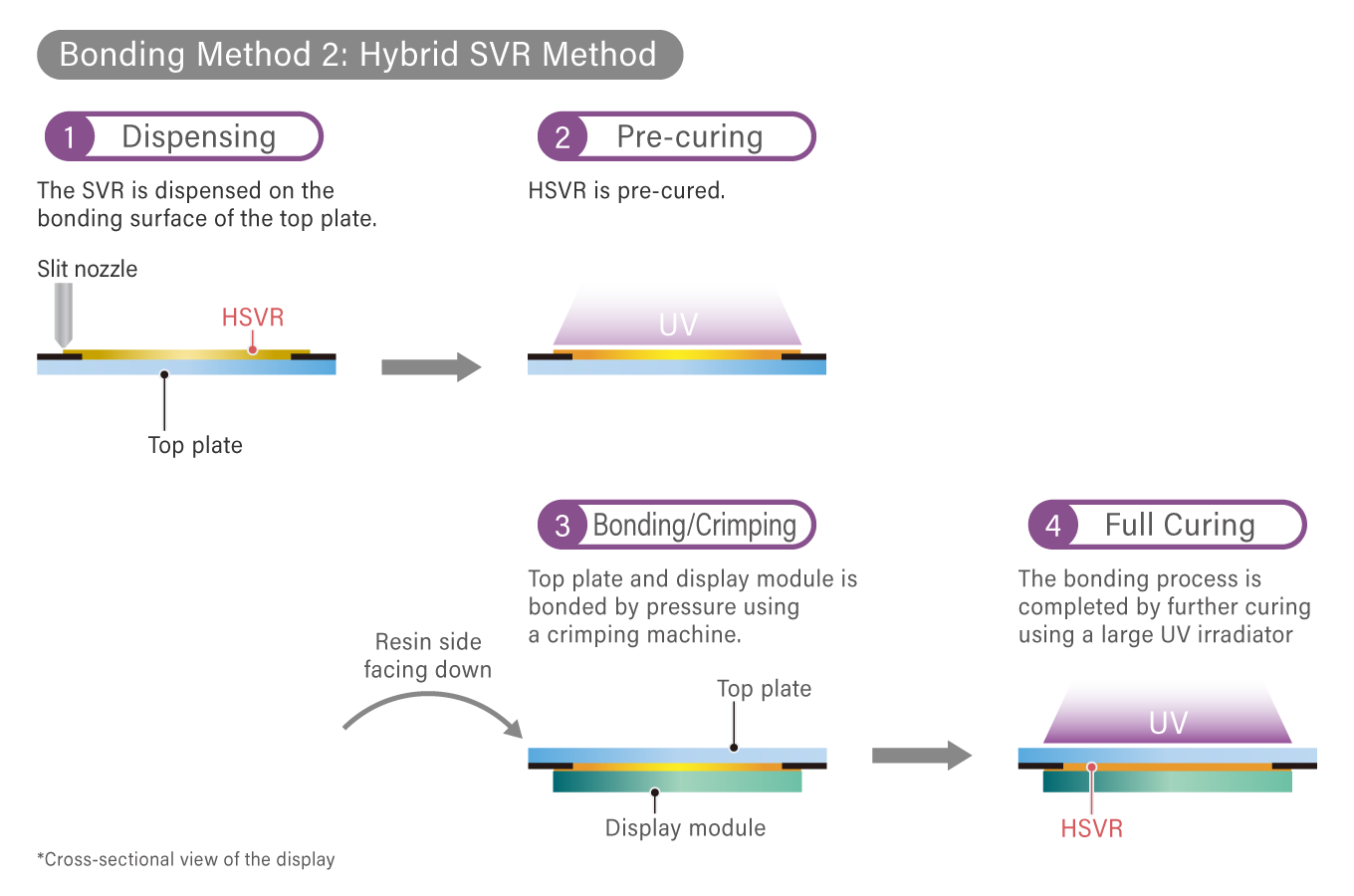
Compared to SVR, another benefit of the HSVR is that it reduces display panel non-uniformity. One of the main causes of a non-uniformity is the resin shrinkage. Due to pre-curing process of the HSVR, the resin shrinkage during the main curing process is substantially reduced.
(3) The Dam & Fill Method
The last method is called the dam & fill method. Like the HSVR method, this bonding process was developed to prevent the SVR from overflow.
In the dam & fill method, resin is applied around the perimeter of the top plate to create a “dam” that holds back the SVR, as shown in the illustration below. The SVR is then applied by the conventional method (dispense-and-flip bonding) and bonded to the display module.
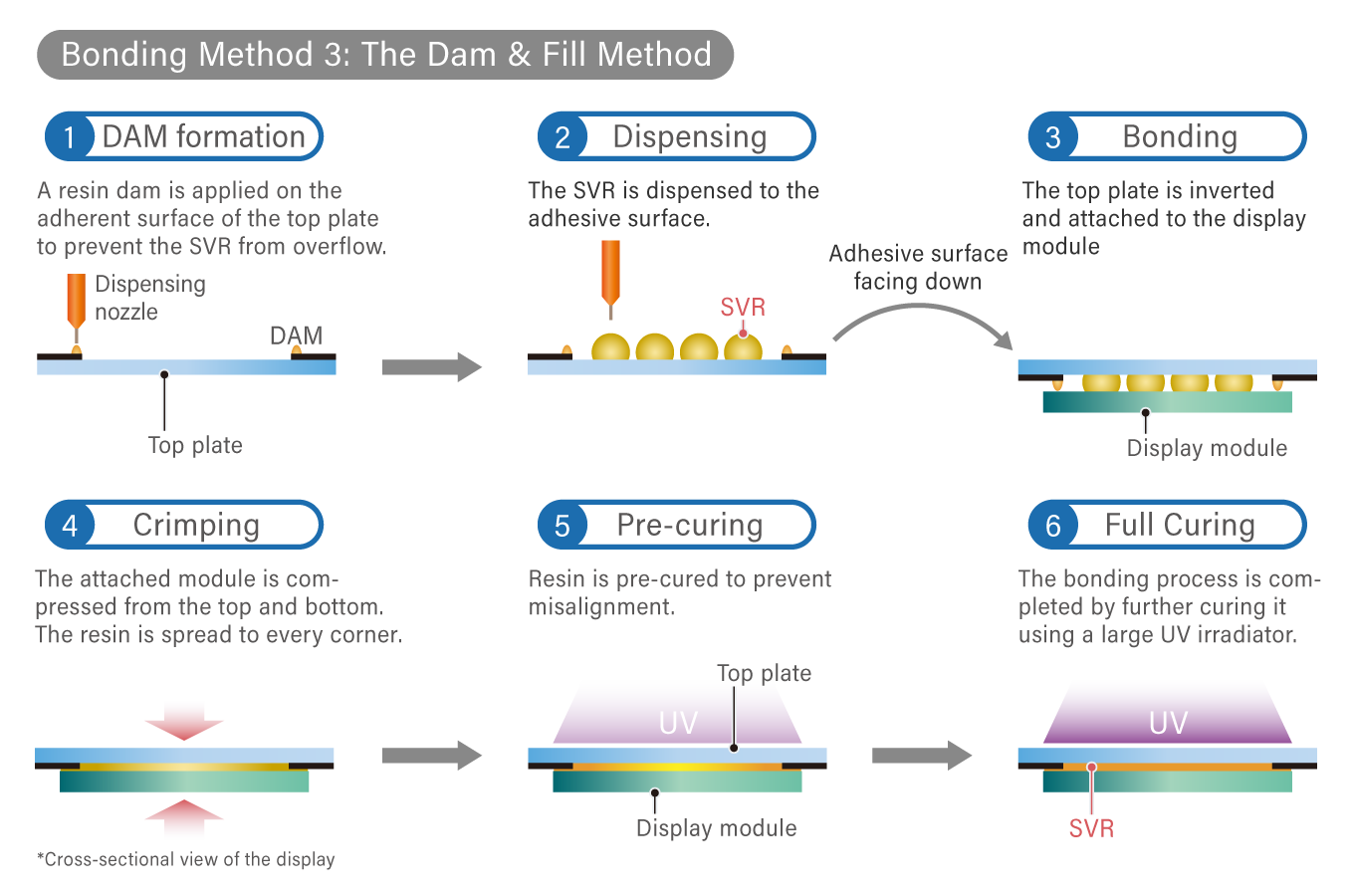
The HSVR introduced earlier is an ideal way to prevent overflow, but it cannot be applied with conventional dispensers, and requires equipment with a slit nozzle (slit coater) for surface coating.
In addition, the slit nozzle is applicable only for square-shaped application, and the size of the top plate is limited by the nozzle’s size. On the other hand, the dam & fill method uses conventional equipment and reduces overflow while also allowing a variety of coating shapes.
These are the three optical bonding methods of displays using SVRs and HSVRs. All of these methods were developed to solve the needs and issues of customers. Dexerials is committed to continue to developing materials and processes to overcome any challenges.
- SHARE