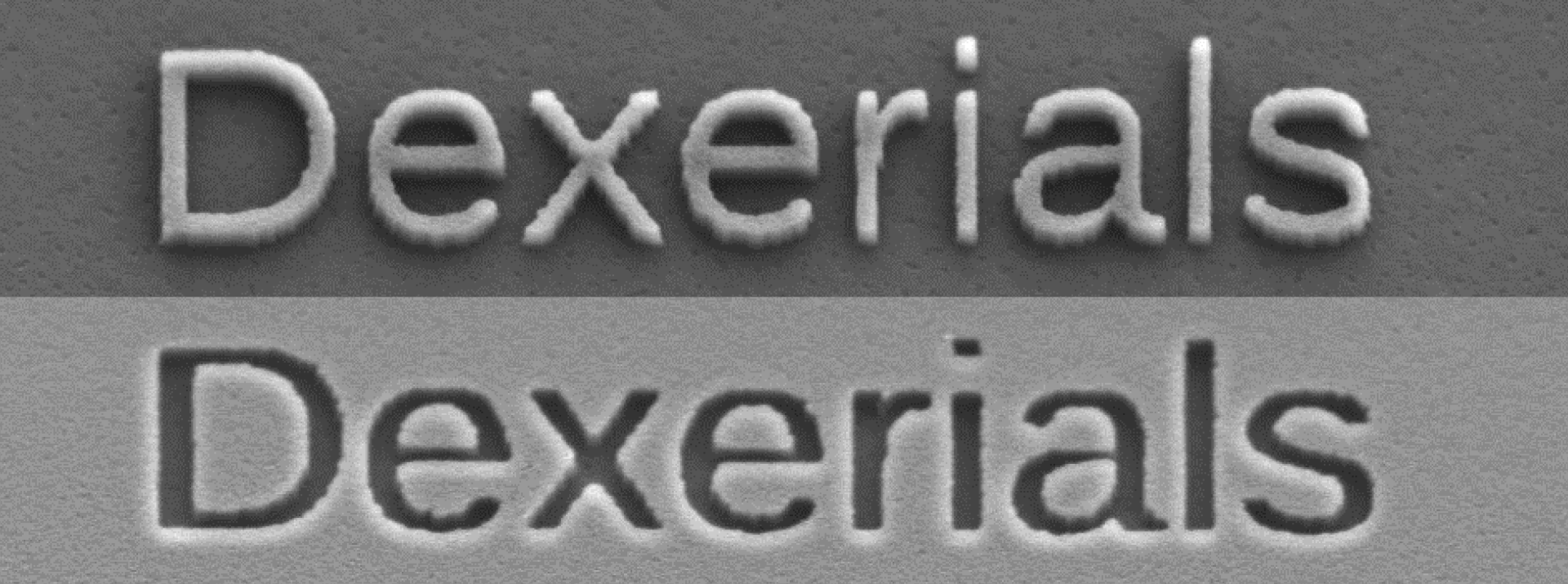
- Optical Products
Transparent anti-reflection film – the latest in microstructure technology
Contents
Highly transparent moth-eye type film
Dexerials has developed a number of innovative materials and components, mainly in the electronics field. One of many is an anti-reflection film that with microstructures inspired by nature.
The surface of a moth’s eye is lined with bumps that are smaller than the wavelength of incoming light (380 nm to 780 nm). The area around the tips of these small bumps does not reflect light entering the moth’s eye (i.e. eliminates glare). It is believed that the moths acquired the feature to minimize the reflection of light on their eyes as an evolutionary process to avoid the risk of being detected by predators.
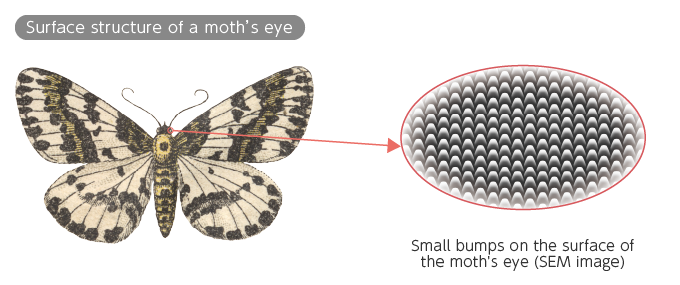
Dexerials’ moth-eye type anti-reflection film has a similar uniform nanometer-sized bumps structure. Due to this structure, it has immensely lower external light reflectance and higher light transmittance than conventional film. Because of its low reflectance, it is used in various applications such as displays and medical shields. Let’s take a look at its manufacturing process below.
Application of Blu-ray disc technology
There are several ways to create moth-eye structures on a film. One of the methods used by many manufacturers is called “anodic oxidation.” In this method, an aluminum plate is dipped in an acidic solution. As electricity passes through it, a chemical reaction occurs, creating numerous microscopic holes on the entire surface of the plate. When a resin film is applied on the aluminum plate, the resin fills the holes and forms bumps.
Dexerials is using a different method originating from the development of Blu-ray Discs to create microstructures, such as the moth-eye structure, on a film.
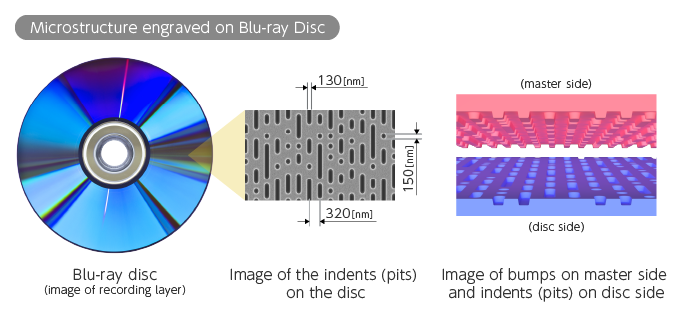
Optical discs, such as Blu-rays and DVDs, record information through a series of small indentations (pits) on their surface. These pits are formed by a master disc with a “bumpy” surface. In the manufacturing process of anti-reflection film with microstructures, the first step is to prepare a cylindrical master mold that will imprint such bumps.
Dexerials manufactures master molds, in which small bumps are systematically engraved on cylindrical material using laser lithography technology.
In this section, the manufacturing process of the cylindrical master molds used for microstructure film will be explained. The master mold rotates cylindrical material while a laser beam is moved in the axial direction of the cylindrical material, engraving a pattern. The position and movement of the laser are computer-controlled with nano-unit precision using a proprietary mechanism. Inputting the data in advance allows more control over the engraved patterns.

Next, the master mold with the engraved microstructure is used to imprint the inverse pattern of the bumps onto the film surface. UV-curable resin is dispensed on the surface of the base film and exposed to UV light while adhering to the rotating master roll. The resin instantly cures and forms a moth-eye structure on the film’s surface. This technology is called “nanoimprinting”.
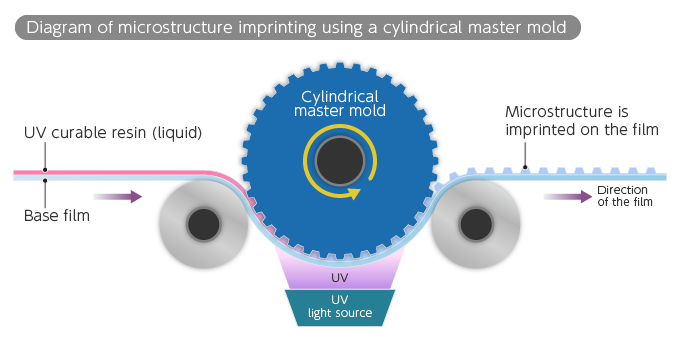
High degree of freedom with pattern design
The anodic oxidation method introduced previously can efficiently deposit microstructures of approximately the same size. However, it is not possible to freely customize the size and shape of the pits on the microstructure of the master roll. The biggest advantage of Dexerials’ microstructure technology is the ability to create accurate and continuous creation of microstructure patterns on master rolls based on pre-programmed designs.
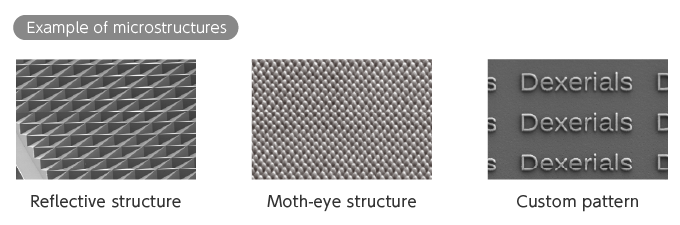
Furthermore, by developing unique lithography and nanoimprinting technologies, Dexerials’ has succeeded in commercializing highly functional film that combines excellent anti-reflection performance and high light transmittance over a wide wavelength range, which is difficult to achieve with other thin optical films.
Although this article is focused on explaining this technology from a manufacturing technology, the ability to achieve the optimal shape for the required function and performance is also essential. That is why Dexerials also prioritizes optical design, including optical simulation, to meet customer needs.
In addition to moth-eye structures, various research is conducted to add new optical functions by creating microstructures on film surfaces. Dexerials will continue exploring the possibilities for new applications.
- SHARE