
- 光学関連
耐光性を持つ反射防止フィルムが実現する、自動車の新しいインテリアデザイン
耐光性に注目した反射防止フィルムの開発
街中を歩いていて、ヘッドライトが黄ばんでいる車を見かけることがありますがこれは紫外線による劣化が原因です。ヘッドライトのカバーに使われているポリカーボネートなどの樹脂が、紫外線に長期間さらされることで化学変化を起こすのです。こうしたことからインテリアにおいても紫外線対策はとても重要です。
自動車のカーナビゲーションなどに使われるディスプレイも、紫外線によって外観が変化する可能性があります。そのため、直接太陽光が当たらないよう、日除けを設けたり、設置位置や角度を調整するなど、デザイン面で工夫がされています。
デクセリアルズは、車載ディスプレイ向けに反射防止フィルムを提案しており、太陽光の反射を抑え、視認性の向上を訴求しています。それによって、日除けを小さくできたり、設置位置や角度の許容度を拡げるなど、インテリア設計がより自由になるためです。また、デクセリアルズでは、ディスプレイがラグジュアリーな車のインテリアに採用される「ピアノブラック」の質感に溶け込むことも大切だと考えています。デザインの一体感はもちろん、紫外線にさらされる状態でも質感を保ち続けることが重要だからです。
そこで今回は、反射防止フィルムの粘着層への技術的アプローチに焦点を当てて説明します。粘着層はディスプレイにフィルムを密着させる重要な層です。従来、透明性と耐光性をあわせ持つ、接着力の開発に重点が置かれていましたが、デクセリアルズでは、インテリアとの一体感をさらに向上させる試みとして、この粘着層を黒系色素で着色しました。もちろん、視認性を確保するため真っ黒にすることはできませんが、実用上問題のない範囲で透明性を少し落とすことで、インテリアとの一体感を上げることができると考えたからです。一方、着色した粘着層が紫外線によってヘッドライトのように黄ばんだり、色あせ(退色)しないか懸念されました。
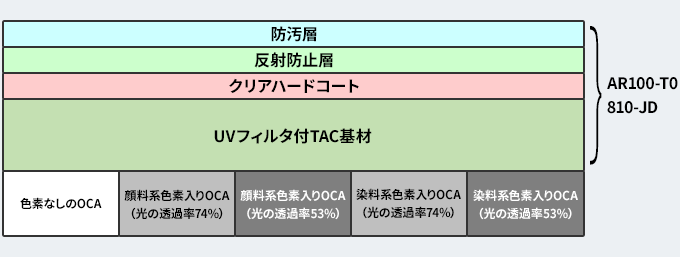
反射防止フィルムの耐光性についての実験
そこで、デクセリアルズでは反射防止フィルムの耐光性を調べるために、強い紫外線を300時間にわたって投射する加速劣化実験を行いました。比較したのは次の5つのサンプルです。①色素なしの粘着層、②黒色の顔料系色素を混ぜた粘着層、③黒色の染料系色素を混ぜた粘着層、④⑤さらにその濃度を変え透過率を変化させた粘着層です。実験では、光の透過率が74%と53%になるよう色素の添加量を調整しています。
色素を顔料系と染料系に分けた理由は、素材に添加されたときの粒子の広がり方が違うためです。顔料系色素は大きめの粒子が拡散するように広がるのに対し、染料系色素は砂糖が水に溶けるように樹脂に溶解して広がります。
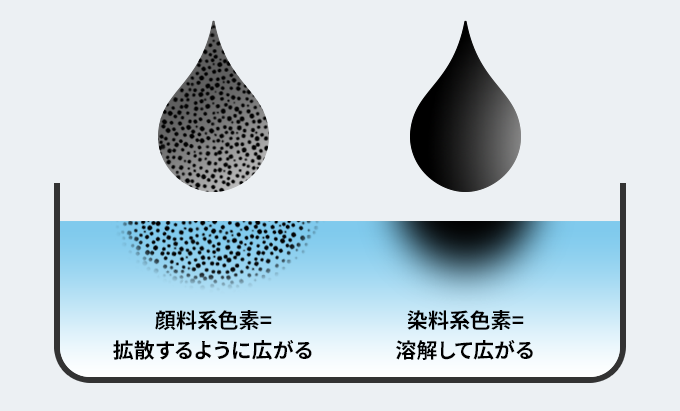
また、透過率を74%と53%の2種類に分けたのは、黒色の濃さによって色の変化の度合いがどう変わるかを見るためです。
試験にあたっては、欧州の自動車メーカーで広く規格として採用されている「DIN75220」の耐光試験の条件に依拠し、紫外線を約4倍の強度で投射しました。サンプルに300時間、強い紫外線を投射し、100時間ごとに取り出して評価を行いました。
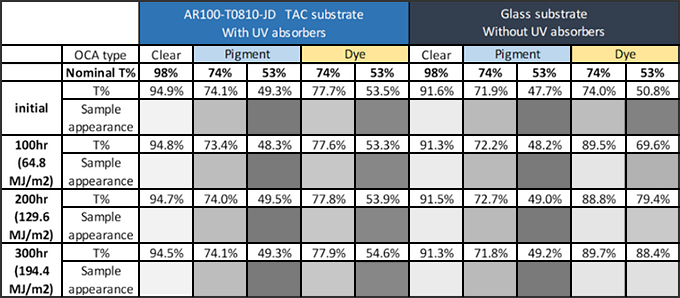
左側半分が反射防止フィルム(TAC基材、UV吸収剤あり)、右側半分がガラス基板(UV吸収剤なし)での結果になります。それぞれに、色素なし粘着材、顔料系粘着材(2種)、染料系粘着材(2種)が付いています。%の数字は「光の透過率」を表しています。%の数字が大きくなるほど、透明度が上がっていることを示し、黒い色素が退色していることを表しています。
車内のインテリア以外にも広がる可能性——ディスプレイの未来
表右側のガラス基板の結果からわかるように、顔料系色素を入れた粘着材はほとんど色味(透過率)に変化がありませんが、染料系色素を入れた粘着材は紫外線によって退色して白っぽくなってしまいました。
「顔料系色素の変化がほぼないのは、色素が無機物のために紫外線による影響が少ないことが理由と考えられます。一方、有機系の染料粒子は、紫外線の影響によって化学構造の変化が起こりやすいことが示されました」(デクセリアルズ株式会社オートモーティブソリューション事業部 豊田倫由紀)
一方、反射防止フィルム側は、染料系であっても透過率はほぼ変わらず、紫外線による退色を防ぐ効果があることがわかりました。
「実験では、染料系色素が紫外線に弱いことがわかりました。しかし『ピアノブラック』のディスプレイを実現するために、顔料系色素で着色した粘着材と、染料系色素で着色した粘着材、どちらが良いかは、簡単には答えが出せません。顔料系色素は、粒子の粒が大きいため、素材の内部に入ってきた光が当たるとそれを散乱させてしまいます。一方、染料系色素を用いた粘着材は光を散乱させないため、深みがあってつややかに見えるのです」(同、豊嶋匡明)
従来、自動車のディスプレイは紫外線の影響を避けるため、直接太陽光が当たりにくいダッシュボードの奥側に設置されることが普通でした。
「しかしこの実験結果によって、反射防止フィルムと染料系粘着材を組み合わせれば、十分な日射耐性を持つ『ピアノブラック』ディスプレイを実現することが可能であるとわかりました。直接日光が当たる場所にもディスプレイが搭載できるようになれば、車内のインテリアデザインの可能性は大きく広げることに貢献します」(豊田)
誰も予想しなかった場所にディスプレイが使われるようになる。デクセリアルズは、そんな未来を楽しみに、研究開発を続けています。
関連記事
- SHARE
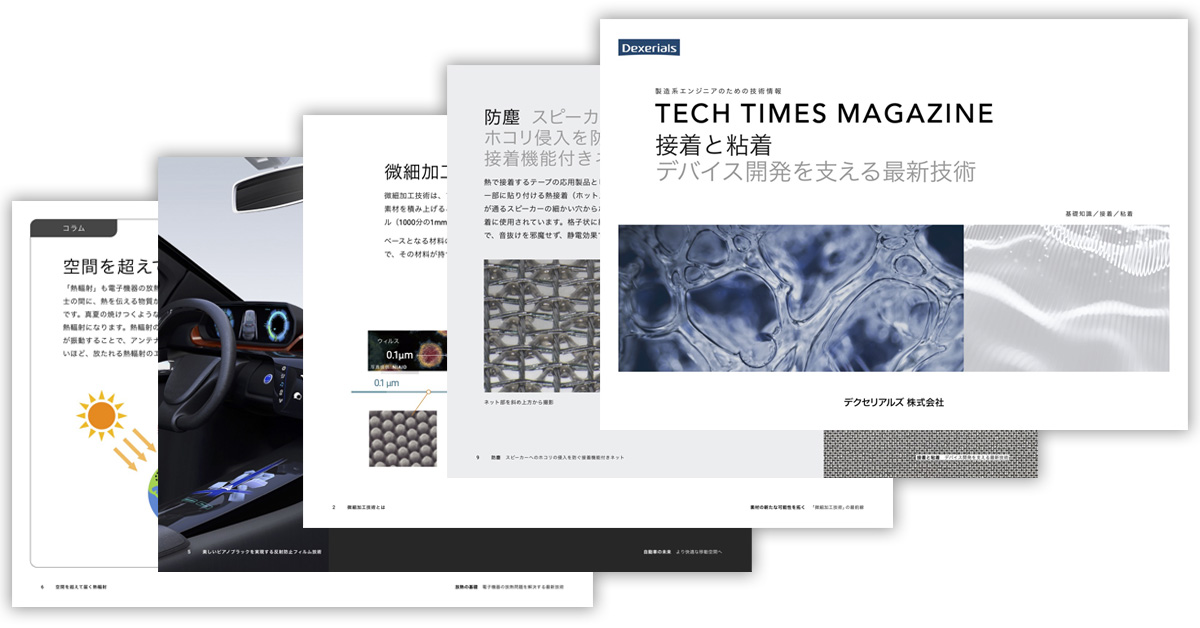
当社の製品や製造技術に関する資料をご用意しています。
無料でお気軽にダウンロードいただけます。
お役立ち資料のダウンロードはこちら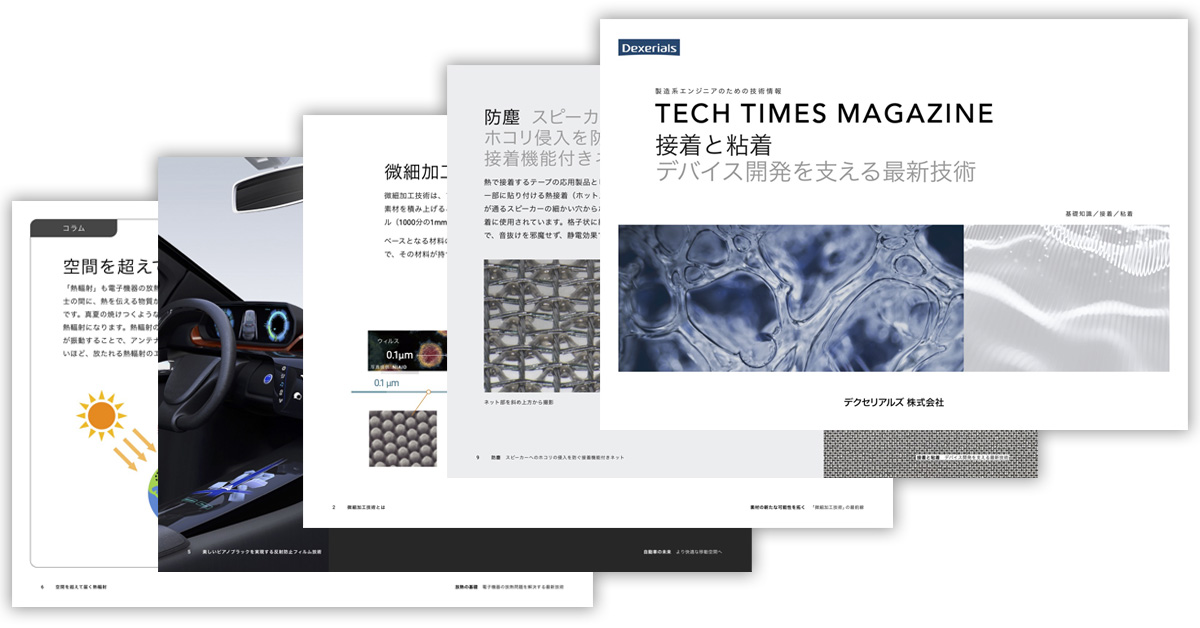
当社の製品や製造技術に関する資料をご用意しています。
無料でお気軽にダウンロードいただけます。
お役立ち資料のダウンロードはこちら