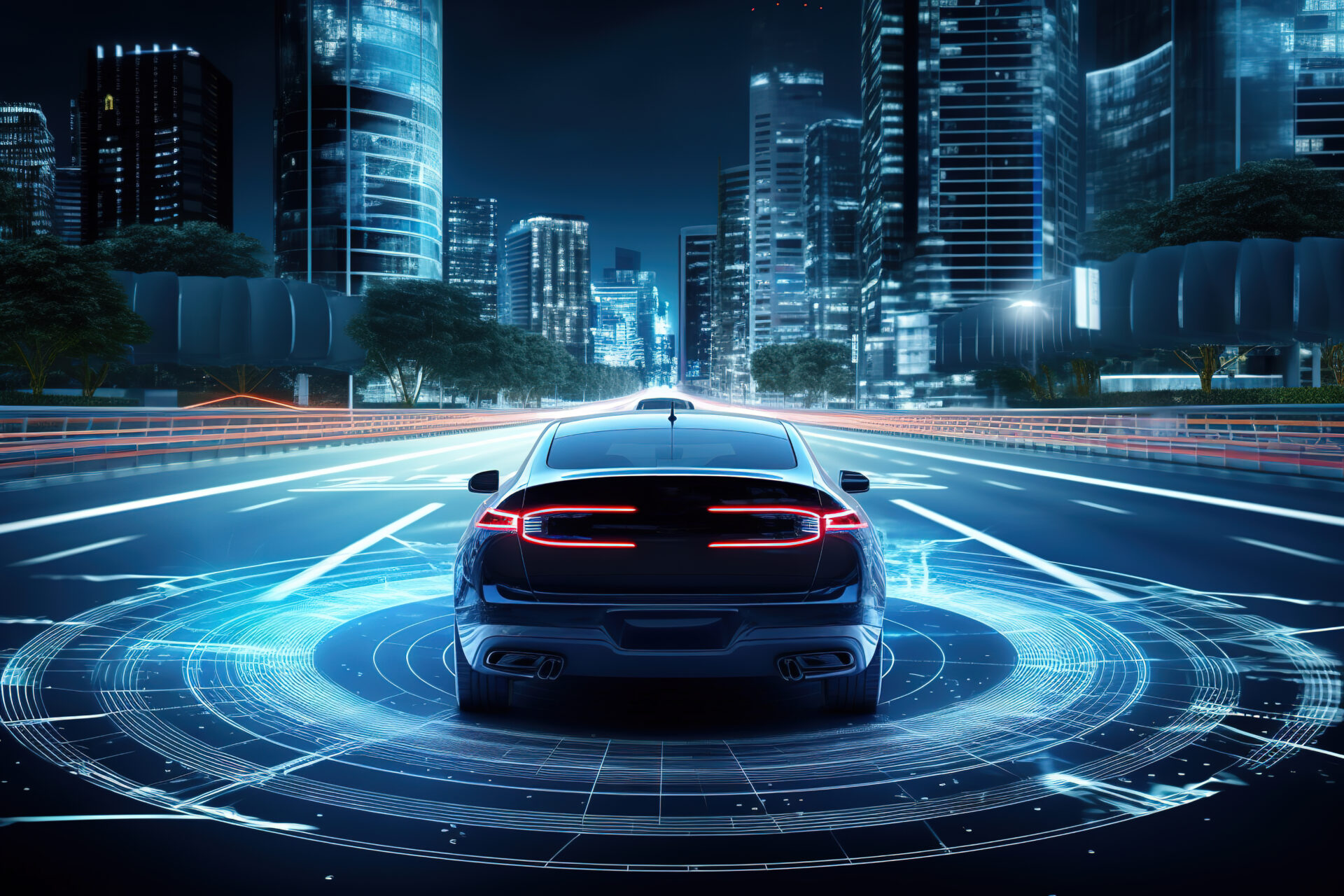
- Optical Products
Five Dexerials Technologies to Enable Smaller, High-Performance LiDAR
Contents
- 1 The expanding market for autonomous driving technology
- 2 The advantages of LiDAR sensor systems
- 3 Working toward wider LiDAR adoption
- 4 High-precision parts fixing technology adopted by many manufacturers
- 5 Anti-reflection film (moth-eye type) to reduce unnecessary reflectivity
- 6 Light-absorbing black adhesive and black coating technology
- 7 Inorganic diffusers to disperse laser light in a desired range
- 8 Anisotropic Conductive Film (ACF) that can contribute to LiDAR miniaturization
- 9 Contributing to the next generation of LiDAR with Dexerials technology and products
The expanding market for autonomous driving technology
As of 2024, automakers around the world are working to develop technology to enable autonomous driving. While Level 1 and Level 2 vehicles that support the human driver are already commercially available, anticipation is high for full-scale market launches of vehicles with Level 3 and above where the system replaces the human driver in the primary role. From a safety perspective as well, anticipation for Level 3+ autonomous vehicles increases each year.
(For details on LiDAR technology, please see The Basics of LiDAR, the Next Generation of Automotive Sensors.)
The advantages of LiDAR sensor systems
LiDAR (light detection and ranging) sensor technology is expected to play a key role in Level 3+ autonomous driving systems. LiDAR uses laser light such as near-infrared to accurately measure the positions of surrounding objects and terrain. It is beginning to be used as the core of autonomous vehicles’ sensor systems. Five advantages of LiDAR sensor systems are:
- High-precision environmental perception
LiDAR collects sensor data in a 360-degree range in real time, providing point cloud data that forms the basis of high-precision 3D maps. These real-time 3D maps enable autonomous vehicles to perceive the ever-changing surrounding environment and accurately recognize streets, pedestrians, other vehicles, and more. - Accurate distance measurement
LiDAR can accurately measure the distance to an object. This distance information is indispensable for allowing an autonomous vehicle to travel at an appropriate speed and apply the brakes at the appropriate time. Especially on highways and in complex urban environments, accurate measurement of distances to moving vehicles, people, and obstacles is critical to safe driving. - Data granularity
LiDAR can provide high-resolution point cloud data to the vehicle’s on-board computers. The data represents object shapes and position in extreme detail, making it useful for the categorization and recognition of objects and enabling the differentiation of pedestrians from bicycles and road signs from obstacles. - Map creation and localization
LiDAR is also used to create accurate 3D maps and determine the vehicle’s precise current location (localization). This allows an autonomous vehicle to compare real-time sensor data against map data obtained in advance to safely navigate while determining its location.
For the reasons above, LiDAR technology is considered indispensable to improving the safety, reliability, and efficiency of autonomous vehicles.
Working toward wider LiDAR adoption
While LiDAR has many excellent characteristics like those discussed above, it is currently only found on certain high-end vehicles. This is because high-performance LiDAR used on autonomous vehicles is extremely expensive and challenges remain in miniaturizing the devices.
Moving forward, cost and size reduction through technological innovation will be necessary to drive widespread adoption of LiDAR. At Dexerials, we believe that we can contribute to higher performance and miniaturization by taking technology we have honed over many years such as high-precision part fixing and material for free manipulation of light and applying it to LiDAR development. The table below shows the product categories we can provide as solutions to each challenge.
In the section that follows, we will discuss each product type separately.
Challenge | Product | Solution |
---|---|---|
Performance improvement | Adhesives | Quick high-precision fixing |
Black adhesives | Optical noise suppression | |
Anti-reflection film moth-eye type | Reduction in IR-range optical reflection and power consumption | |
Inorganic diffuser | Diffusing light in a target range | |
Miniaturization | Anisotropic conductive film(ACF) | Substitution for connectors |
High-precision parts fixing technology adopted by many manufacturers
The first technology that can contribute to improved LiDAR performance is our high-precision parts fixing technology. Dexerials has developed smart precision adhesives (SA series) cured by heat, UV, etc. for high-precision bonding of parts that make up high-performance cameras for digital cameras and smartphones, and they have been adopted by many customers. In the case of digital cameras, a circuit board with the CMOS image sensor is bonded to the lens unit to form a camera module. Shifts in position or orientation during the bonding of these optical parts lead to image blurring and decreased image quality, so it is necessary to suppress heat stress such as curing shrinkage during bonding. Our smart precision adhesives are designed for fast, low-temperature adhesion to address these challenges. We believe that many customers have adopted them because these characteristics lead to production efficiency improvements in their processes.
As LiDAR sensors detect objects by using light, high-precision bonding of optical parts leads directly to improved performance just like in the case of cameras. The diagram below shows the process for high-precision bonding of sensors, known as active alignment. In active alignment, epoxy cation-type black adhesive with a low shrinkage rate is used to minimize shifting after optical axis adjustment is complete. The lens unit’s position and angle are adjusted while measuring sensor output, and infrared and UV light is used to quickly cure the adhesive when parts align for the highest performance.
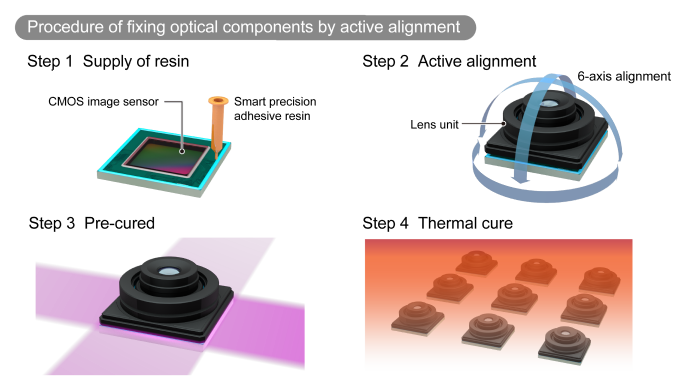
For details on adhesive technology for automotive sensing cameras, please see High-Precision Adhesives Used in Automotive Camera Sensors.
Anti-reflection film (moth-eye type) to reduce unnecessary reflectivity
The second Dexerials technology to enable high LiDAR performance is anti-reflection film (moth-eye type). The diagram below shows how it can be applied inside the front cover of the main unit in a LiDAR system.
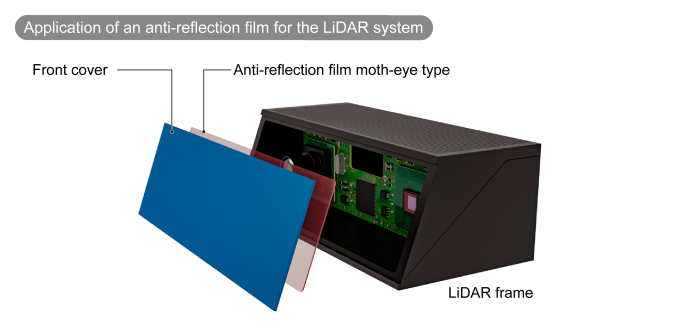
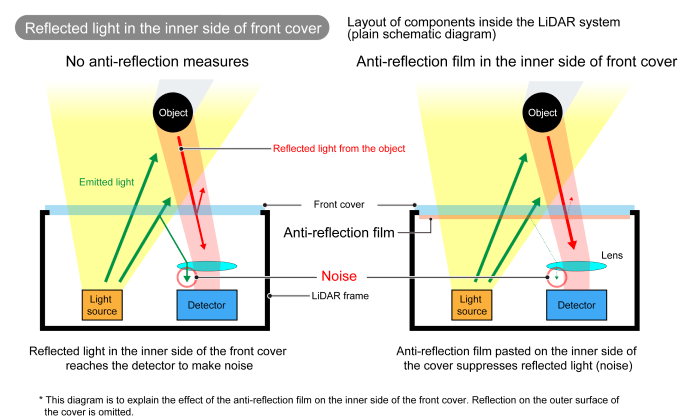
A LiDAR system emits light, detects the light that reflects off an object with its sensor, and calculates the distance to the object based on the time differential. As a result, minimizing the amount of light prevented from reaching the sensor leads to improved performance. The anti-reflection film developed by Dexerials minimizes light reflection to suppress noise caused by reflected light.
The moth-eye type reproduces the surface structure of the eye of a moth, an insect that can fly freely in the darkness of night, on film to create what can be called the ultimate anti-reflection film. Anti-reflection film for displays is intended to control visible light, but Dexerials has created technology to prevent the reflection of invisible light such as near-infrared used by LiDAR as well. By combining LiDAR with anti-reflection film, it becomes possible to improve the precision of sensor systems.
We are also developing anti-fog moth-eye type anti-reflection film that prevents fogging from water vapor, etc. In LiDAR for autonomous vehicles, temperature differences between the outside environment and LiDAR internals or weather such as snow can lead to fogging inside the LiDAR structure and decreased performance. It is thought that heaters are necessary to warm covers like door mirrors to prevent this. But by applying moth-eye type anti-reflection film with anti-fog properties to the cover, we believe it will be possible to suppress performance degradation due to fogging without supplying electrical power.
For details on moth-eye structures, please see Anti-Reflection (AR) Film with Moth-Eye Structure for In-Vehicle Displays Application.
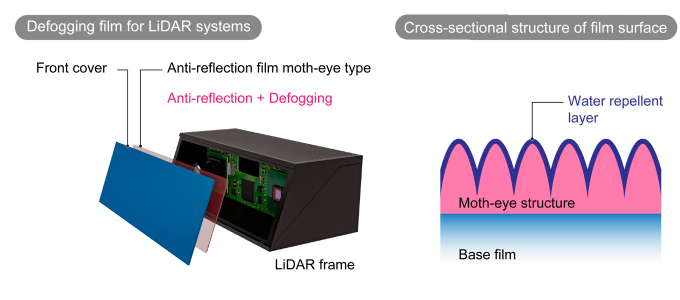
Light-absorbing black adhesive and black coating technology
The third technology that can contribute to high LiDAR performance is Dexerials’ own black adhesives and black coating. When light enters a LiDAR structure and is reflected and scattered inside, it becomes noise that lowers measurement precision. As a result, it is necessary to make as much as possible of the inside surface pitch-black to absorb light and reduce reflection within the structure. In addition to developing high-precision fixing technology for digital cameras, Dexerials has created black adhesive and black coating technology to maximize light absorption that can be applied to LiDAR sensors.
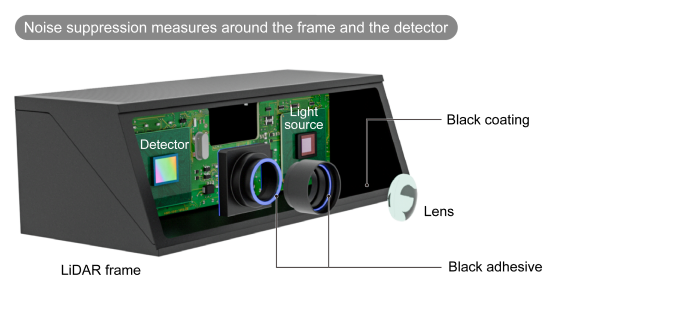
Inorganic diffusers to disperse laser light in a desired range
The fourth Dexerials product that can contribute to next-generation LiDAR development is the inorganic diffuser. Currently, the primary form of LiDAR uses the “mechanical method,” where the parts that emit laser light are rotated with a motor to measure distance to objects in a wide range. But in recent years, LiDAR development has progressed on the “flash method,” which aims to improve performance by dispersing laser light over a wide range to measure distance to objects. Dexerials has developed inorganic diffusers to disperse laser light on projectors such as those used for corporate presentations, and we can apply that expertise to LiDAR light sources to disperse sensor light to the desired range.
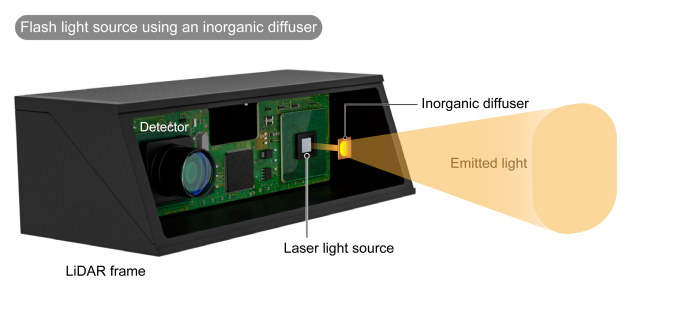
For details on inorganic diffuser functionality and characteristics, please see Inorganic Diffusers with Microlens Arrays.
Anisotropic Conductive Film (ACF) that can contribute to LiDAR miniaturization
Dexerials’ ACF technology can contribute to LiDAR miniaturization. ACFs are a film material used to secure and electrically connect electronic components such as integrated circuits (ICs) to circuit boards. Launched as a product in 1977, they are now used as a circuit adhesive in many of the digital devices sold around the world, such as smartphones, tablet PCs, and high-definition TVs.
By applying heat and pressure, ACFs sandwiched between circuit boards and IC chips can electrically connect terminals to circuits, maintain insulation between adjacent terminals, and secure IC chips to circuit boards. Compared to conventional connectors, they make connections in a small area and almost no thickness, enabling smaller circuits overall.
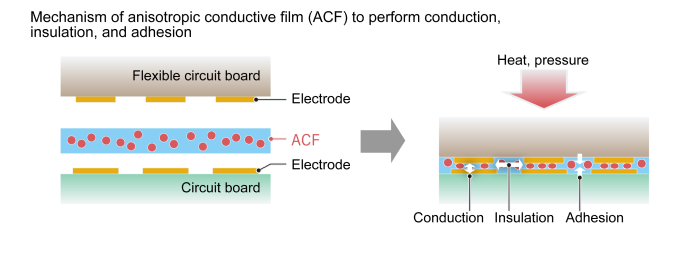
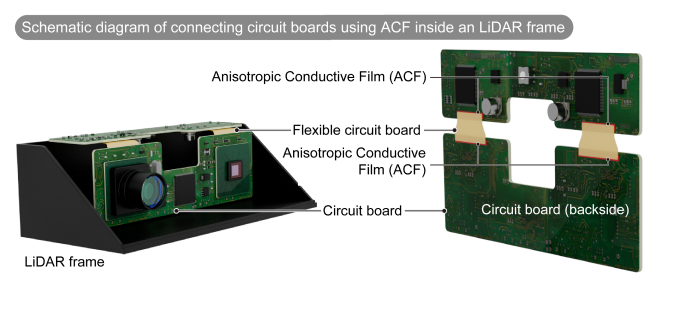
Contributing to the next generation of LiDAR with Dexerials technology and products
The Dexerials technologies and products discussed above have the potential to contribute to the development of next-generation LiDAR. Beginning with the efforts of our predecessor company, we have spent more than 60 years conducting research and development for many technologies such as high-precision parts fixing and materials to freely manipulate light. We believe that the knowledge and technologies we have built over the years can contribute in many different areas that lead to the realization of a future society based on autonomous driving. If you are involved in the development of autonomous driving technology such as LiDAR or if you are interested in our technology, please do not hesitate to contact us.
- SHARE