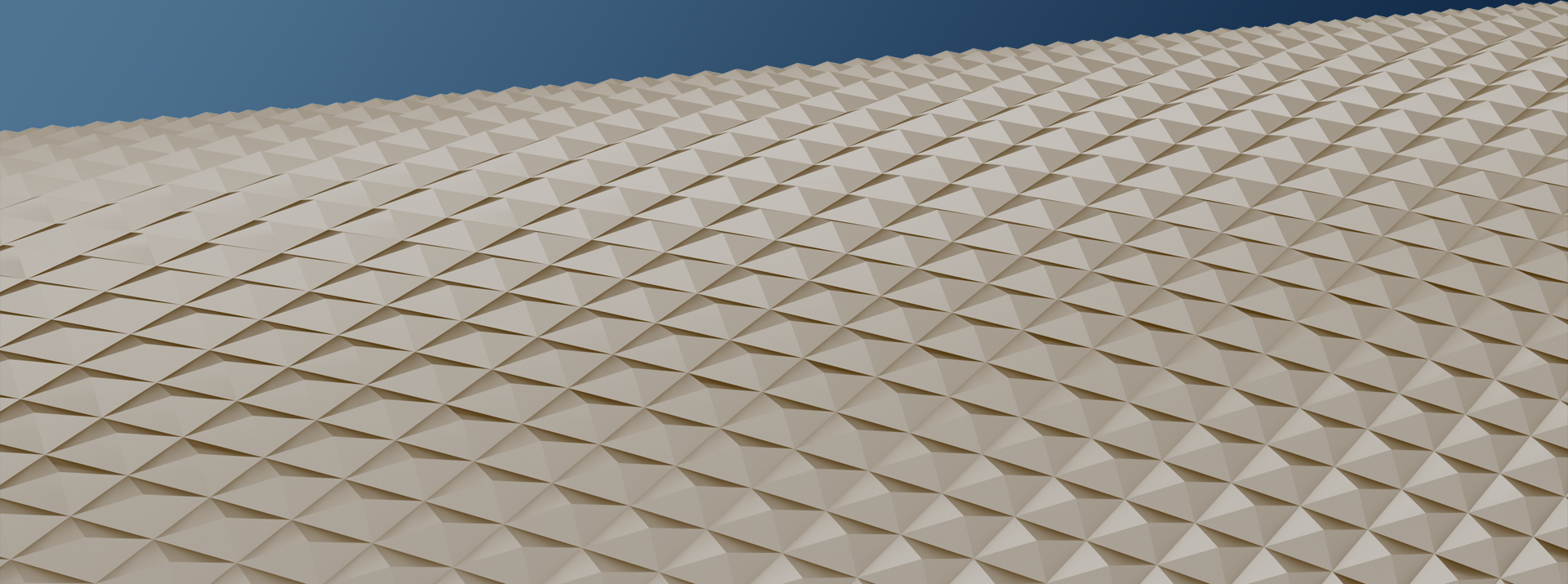
- Elemental Technologies
Master Mold Processing: The Key to Imprint Technology
Contents
How microstructures are formed on film
Dexerials’ roll-to-roll process for imprint technology can continuously form microstructures ranging from hundreds of nanometers to hundreds of micrometers on films up to hundreds of meters long.
The illustration below shows the concept for the roll-to-roll imprinting process. The base film, which has UV-curable resin applied to it, moves in from the left and is pressed against the cylindrical master mold for the microstructure in the center before moving on to the right. As the base film passes under the master mold, the resin is shaped by the mold and undergoes UV light curing to transfer the microstructure pattern to the substrate surface.
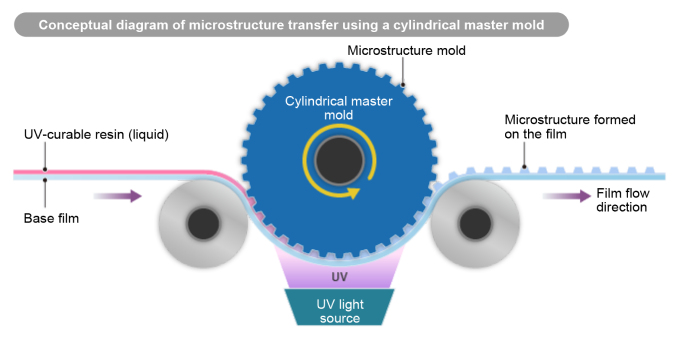
Creating a seamless and precise cylindrical master mold
Dexerials has two ways to create the master molds used in transferring microstructure patterns to film substrates—lithographic processing and precision machining. The diagram below shows a schematic of microstructure shapes being drawn onto the cylindrical base material with lithographic processing using laser imaging. Resin is applied to the surface of the cylindrical base material to form a resist. After a laser draws a pre-calculated pattern into the resist, gas turned into plasma is used to create the microstructure in a process called dry etching. Lithographic processing enables the etching of precise, nanometer-scale patterns onto the master mold.
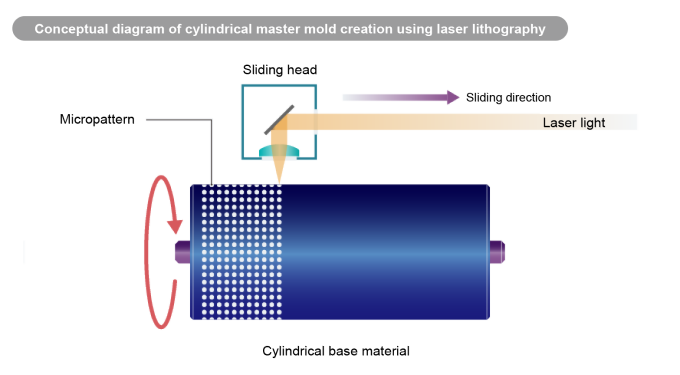
The other method of master mold creation is precision machining. Here, microstructures are formed on the surface with a high-hardness cutting blade made of diamond, etc., while spinning the cylindrical metal base material. Various patterns can be cut depending on the size and shape of the cutting blade.
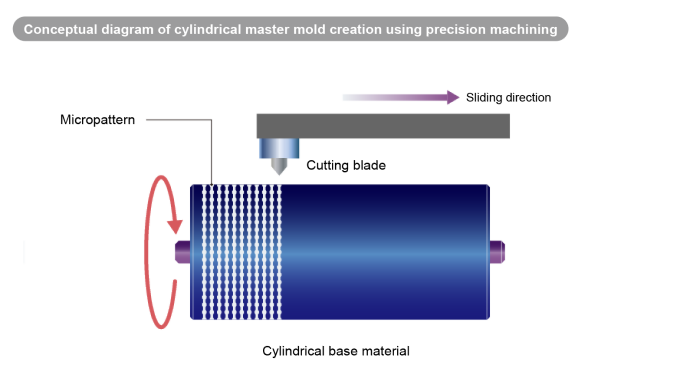
Exceptional accuracy in precision machining
Precision machining can create master molds with microstructures down to the nanometer scale at high accuracy. The cylindrical master mold is made of a metal base material such as stainless steel or iron, and its 1600 mm width allows it to transfer microstructure patterns across a large area at once.
Controlling the processing environment is critical for precision machining. If the room’s temperature rises by 1°C during processing, a piece of metal 1600 mm long will expand by 20 μm (0.02 mm) due to thermal expansion. This change cannot be ignored because the microstructures are several micrometers in size. There are also factors such as frictional heat from the area being cut with the blade. A stable environment is indispensable for precision machining at high accuracy. At Dexerials, we have implemented fully automatic processing and strict control of many parameters affecting processing precision, such as room temperature and base material temperature, to create the intended shapes accurately.
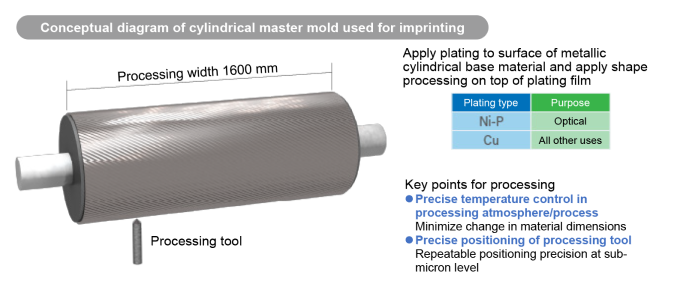
The cutting process for master molds
The diagram below shows the process for precision machining. First, an appropriate cutting blade is used to engrave the desired micropattern into the machinable plating layer applied to the base material. Next, a test UV film is formed for measurement and evaluation with a scanning electron microscope (SEM). Then, after cleaning and mold release treatment,* the cylindrical master mold for imprinting is complete.
*Treatment that makes it easier to separate the pressed resin from the master mold.
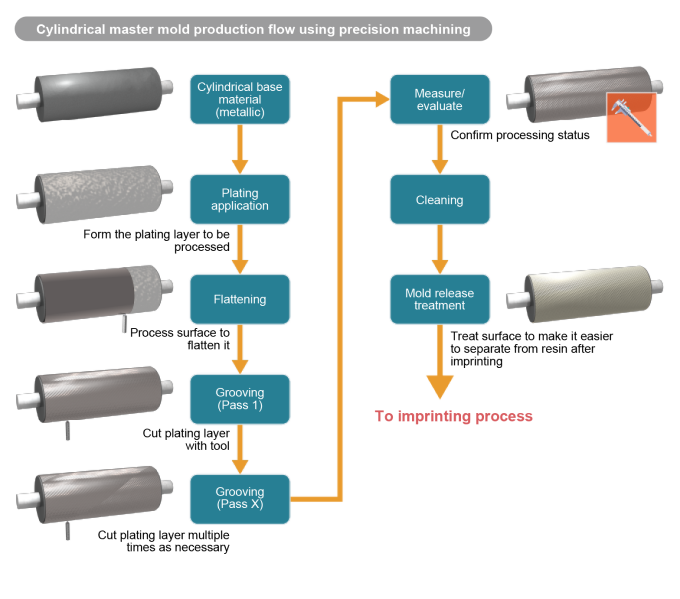
Examples of precision-machined micropatterns
The photographs below are magnified electron microscope images of brightness enhancement lens film for LCD TVs produced using a precision-machined master mold. The size and shape of the mountain-shaped patterns engraved into the surface can be changed freely by adjusting the size and shape of the cutting blade.
Micropatterns created through precision machining can control the reflection of light and heat in various ways depending on their shapes. Based on its precision machining technology for cylindrical imprinting master molds, Dexerials will continue its research and development toward functionality that cannot be achieved through materials alone to pursue potential new products.
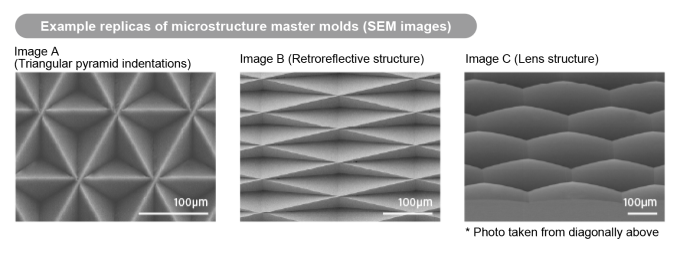
- SHARE