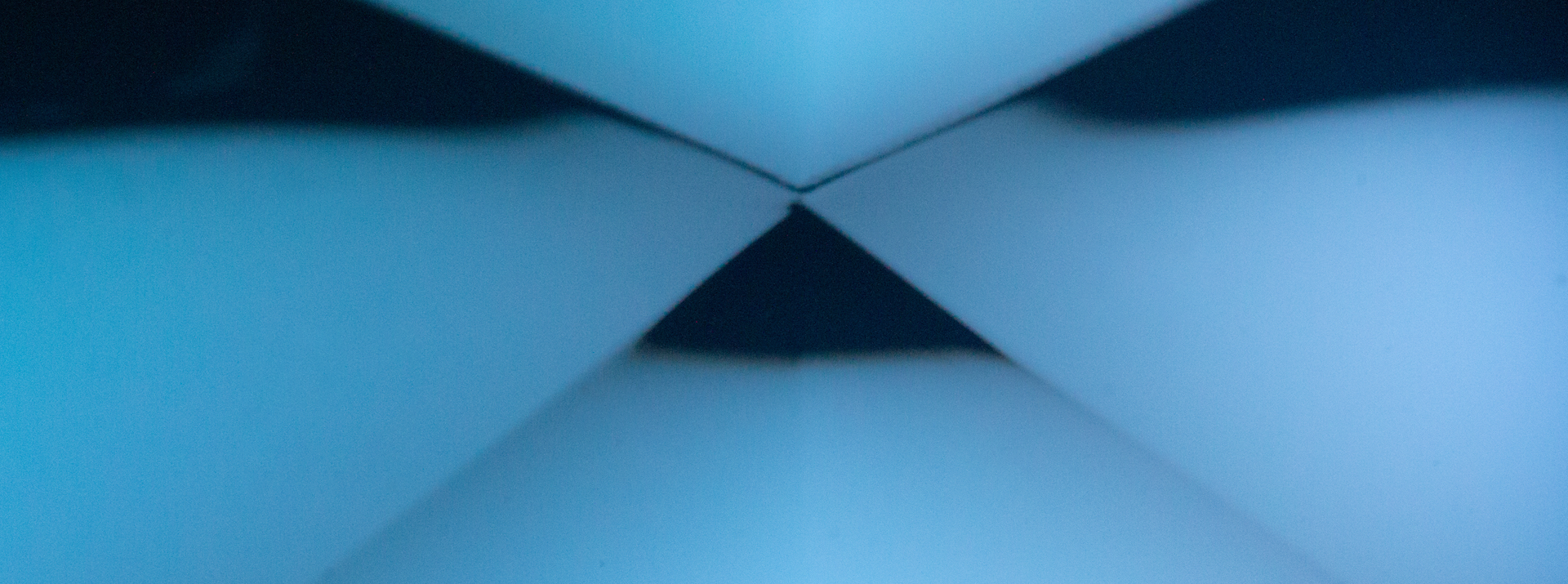
- Elemental Technologies
Precision Microstructures Created by Imprint Technology
Contents
The key to micromachining: Roll-to-roll imprint production technology
Dexerials’ micromachining technology can form microstructures of diverse sizes and patterns ranging from hundreds of nanometers to hundreds of micrometers by engraving the surface of substrates such as film, resin boards, or glass. Layering materials can also create the opposite effect. By forming complex microstructures based on meticulous calculations on the substrate surface, useful functionality such as controlling light reflection can be added. Imprint technology with Dexerials’ unique roll-to-roll process makes this possible.
Roll-to-roll production is where a roll of a substrate (like films) up to several hundred meters long is processed as it is unrolled, and the processed substrate is subsequently wound into another roll. In another approach to micromachining, batch processing, one flat substrate is processed at a time. However, our roll-to-roll technology’s continuous processing of extremely long materials makes it a particularly efficient production method.
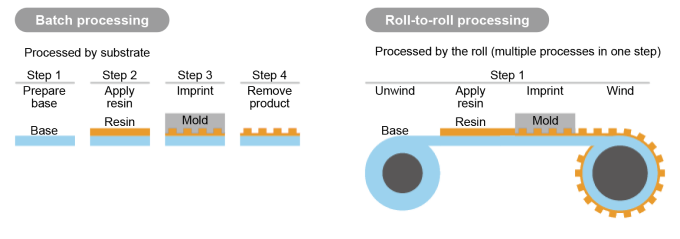
What is imprint technology?
Micromachining at Dexerials is a combination of the roll-to-roll process above and imprint technology.
In imprint technology, a mold is pressed into soft resin, etc., to transfer the shape. The images below show this process, but the same principle applies when a cylindrical mold made of metal or glass is used to transfer shapes into film, etc.
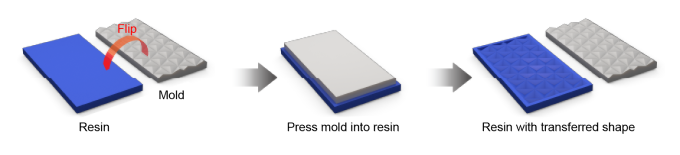
In UV-imprinting using ultraviolet light, UV-curable resin is applied to the surface of substrates such as film and cured via UV light while the mold is pressed into it. The inverted pattern forms on the film’s surface after removing the mold.
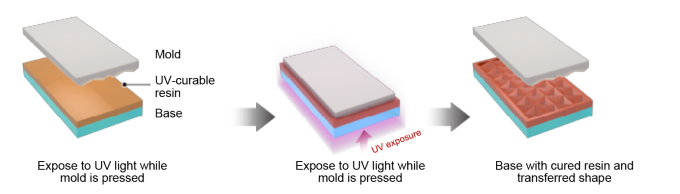
Imprint technology in the roll-to-roll process
The diagram below shows a schematic of the roll-to-roll process for imprint technology. First, a dispenser applies UV-curable resin to the base film unwound from a roll. Next, shapes are transferred to the applied resin as it passes through the cylindrical master mold. At the same time, UV light cures the resin. This applies micromachining from the master mold to the film surface, and the film is again wound into a roll as the finished product. The surface of the master mold is processed with a mold release treatment so the cured resin separates from the mold cleanly.
To enable this roll-to-roll process for imprint technology, a wide range of elements must be carefully adjusted: precise micromachining technology for the cylindrical master mold, humidity and temperature control inside the device, UV intensity, roll motion control, thickness and composition of the applied resin, viscosity, etc. Dexerials has many years of expertise in the roll-to-roll process for imprint production, with a bank of knowledge and results that give it an overwhelming advantage over other companies.
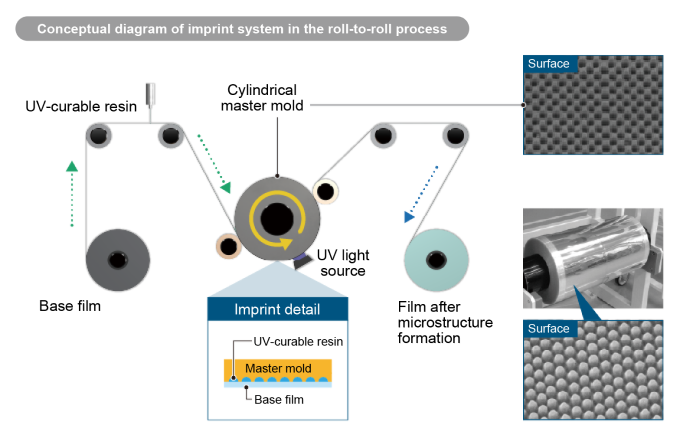
The starting point: Optical film for LCD TVs
Dexerials’ imprint technology used in the roll-to-roll process started with the development of prism-type brightness enhancement film (often called lens film) used inside displays to enhance the brightness of LCD TVs. Prism-shaped structures are formed on the surface of brightness enhancement film to efficiently collect light from the LCD TV’s backlight and raise the brightness by approximately 1.7 times. It is now an indispensable part of LCD TV manufacturing that not only increases screen brightness but also contributes to reducing power use.
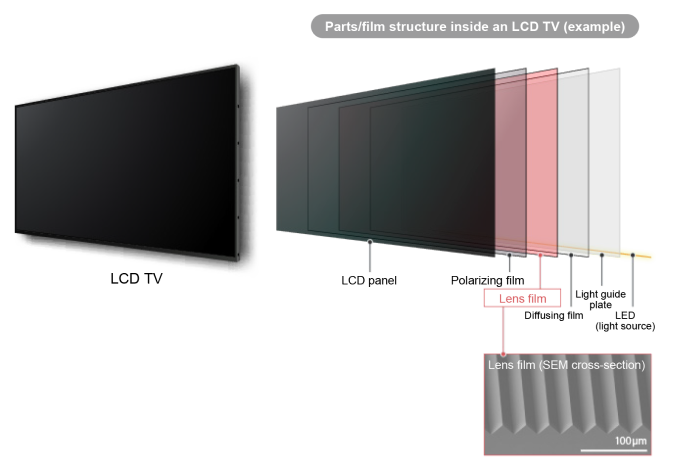
Working toward more advanced microstructures
Based on its proprietary imprint technology, Dexerials has developed functional films that control the effects of light and heat. The scanning electron microscope images below show some examples of microstructures on the film surface. The film on the left (Image A) shows a dense pattern of dents made by four-sided pyramids with a rhombus as a base. This retroreflective microstructure reflects incoming light back in the direction of its source (retroreflection) by forming a reflective layer on the surface. This makes it possible to create unique functions by selecting a light wavelength and forming a reflective layer, for example. It is also possible to create a pattern of small bell-shaped bumps or any image or text as we work to propose microstructures that meet our customers’ needs.
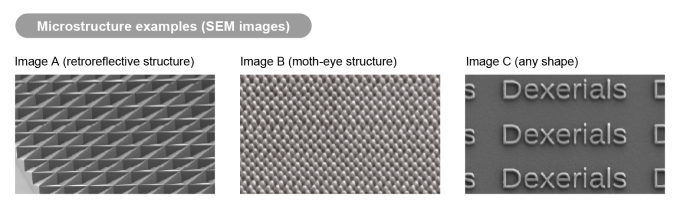
- SHARE