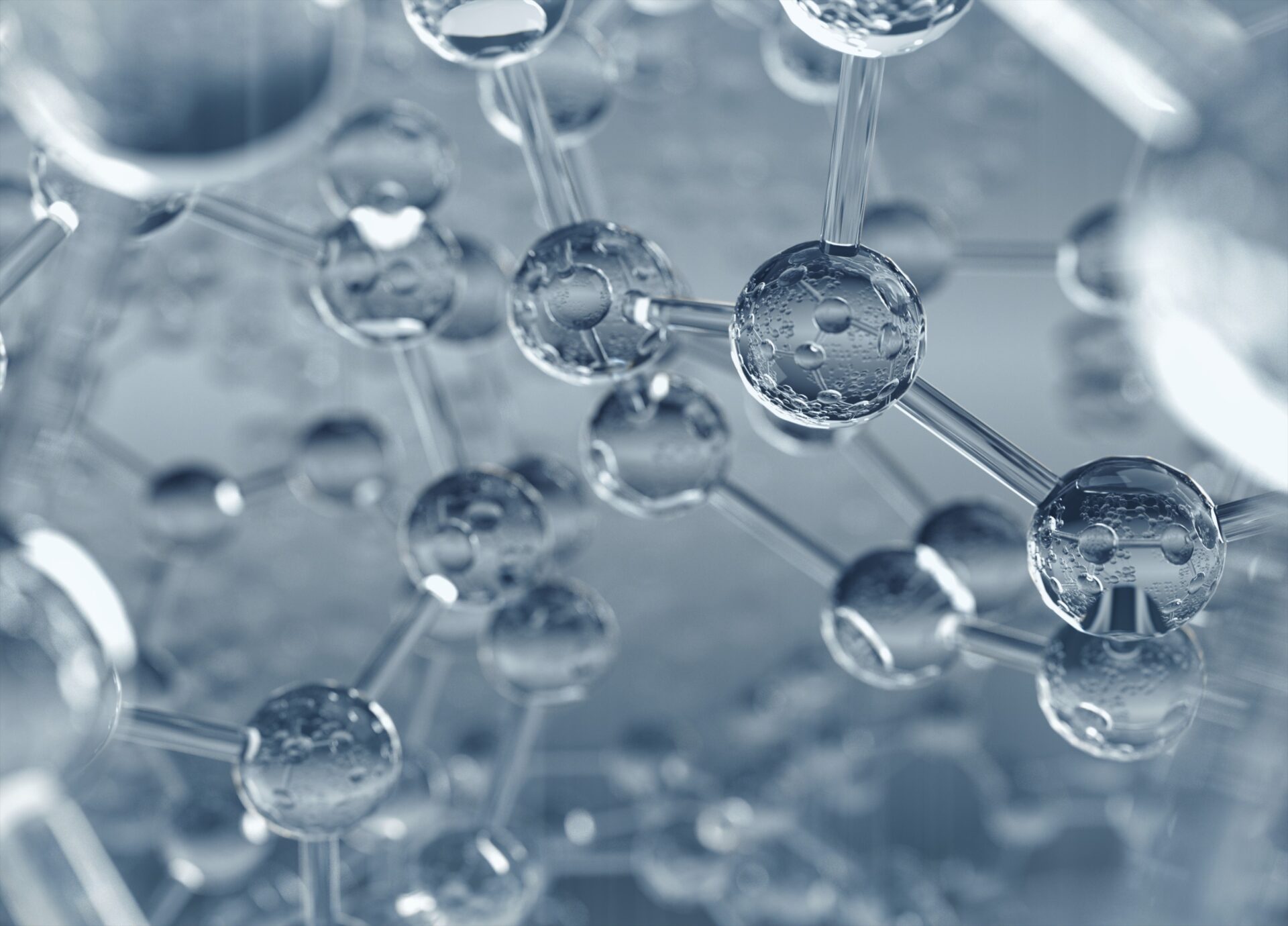
- Bonding Products
Thermo-curable Adhesive Mechanisms (Crosslinking Reactions and Their Types)
Contents
What are thermo-curable adhesives?
As the name indicates, thermo-curable adhesives are adhesive materials that undergo a hardening reaction in response to heat. While some are available in film form, most are liquids. Materials of various molecular weights are mixed into the liquid, and they harden and adhere via crosslinking reactions in which heat causes the functional groups of those molecules to connect three-dimensionally and polymerize.
Crosslinking reactions are irreversible
Crosslinking reactions are irreversible reactions. To illustrate this, let us examine the opposite concept of reversible reactions. Below are some common categories of adhesives—adhesives such as cellophane tape are also categorized as pressure-sensitive, but here we will focus only on cases where the adhesive itself undergoes change.
-3角_E.png)
Some commonly-encountered examples of adhesives that undergo reversible reactions include starch paste and glue sticks used for school crafts, wood glue used for home DIY projects, and hot melt adhesives. Hot melt adhesives, also known as hot glue, melt when exposed to heat and are used to secure parts when they cool and solidify. In recent years they are often used with hot glue guns to handcraft things like accessories. The primary component of this hot glue is thermoplastic resin, which transitions from hard to soft states in response to heat. In other words, the change is reversible. This is because the resin molecules’ reaction to heat is not a crosslinking reaction but a change in intermolecular forces, similar to ice melting to become water—the molecular structure itself does not change.
However, thermo-curable adhesives undergo irreversible reactions, such as a crosslinking reaction triggered by heat to shift the liquid to a solid (phase change). Once the change occurs, applying heat to the resin again will not cause a change of state. This is because the resulting structure from the intermolecular crosslinking reaction is extremely strong and stable. When creating thermo-curable adhesives, it is possible to adjust the type and ratio of materials to increase the crosslinking density, resulting in higher heat resistance after curing as well as greater chemical resistance and moisture resistance.
As a result, thermo-curable adhesives feature high reliability after adhesion and are widely used as industrial adhesives, such as in semiconductor mounting materials for electronic parts.
The five main types of thermo-curable adhesives used in electronic parts
There are five types of thermo-curable adhesives used in the production of electronic parts. Let us examine the characteristics of each below.
■ Epoxy acid anhydride
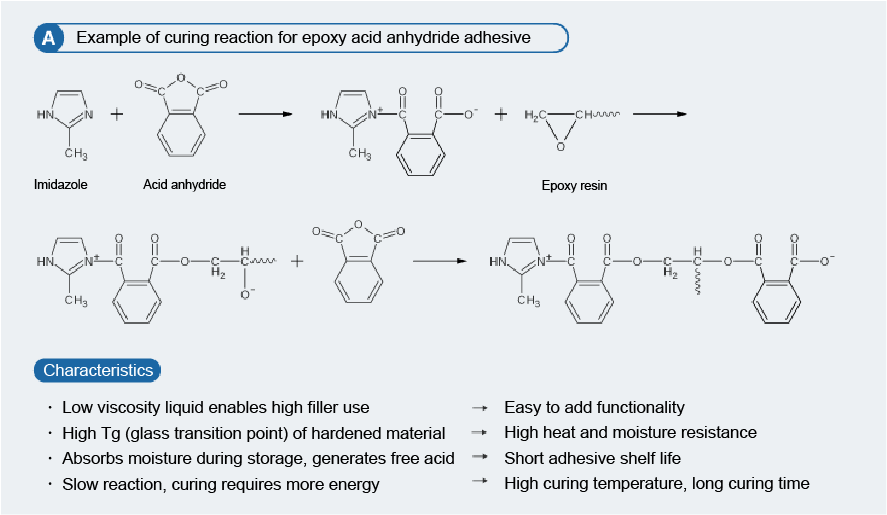
With this type of adhesive, imidazole and acid anhydride react and combine, then polymerize with epoxy to harden. Many acid anhydrides are low viscosity, making it possible to mix them together with a variety of other ingredients. It is easy to include fillers that add functionality to adhesives, enabling the creation of adhesives that retain their useful characteristics even at high temperatures by adding fillers that boost mechanical properties.
On the other hand, acid anhydrides decompose and generate free acid when combined with water. They absorb moisture easily during storage and have low resistance to humidity, making short shelf life one possible disadvantage. Other drawbacks are high curing temperature, slow reactivity and long curing times, and gas generation during curing due to low viscosity.
Despite these downsides, the aforementioned excellent heat resistance remains an attractive advantage. Epoxy acid anhydride adhesives are currently widely used in semiconductor mounting materials and are known as highly reliable adhesives.
■ Epoxy anionic polymerization
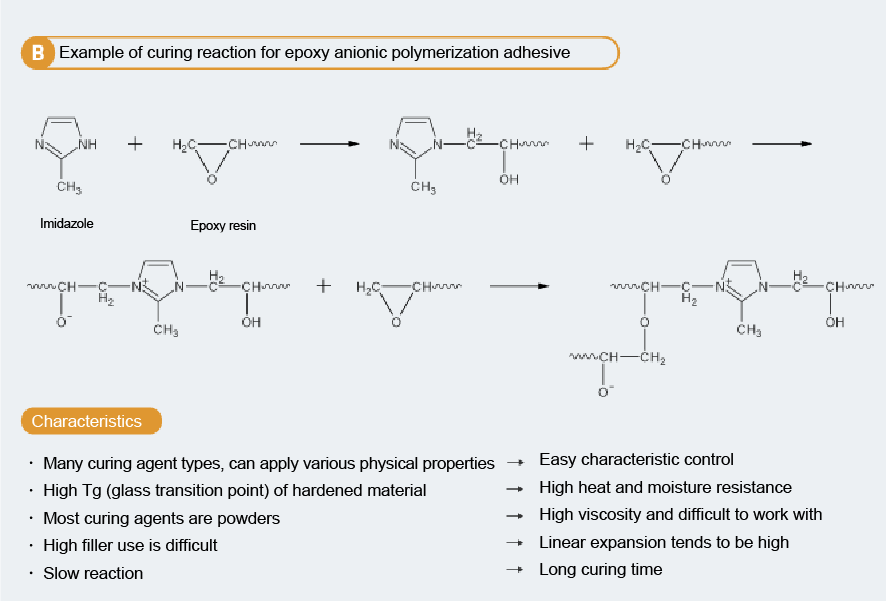
Epoxy anionic polymerization adhesives harden when epoxy groups combine with the amine molecules used as a curing agent. The materials have been in use for a long time and many amine types have been developed as curing agents, making it easy to control their physical properties.
Adhesives can be divided into two types—those consisting of one component and those in which two components are mixed together. When making a one-component epoxy anionic polymerization adhesive, a curing agent in powder form is often used, resulting in high viscosity of the mixed liquid. The higher the viscosity, the more difficult it becomes to achieve a high filler density to add heat resistance. The result is a higher linear expansion coefficient (coefficient of change in object size due to heat). Difficulty of use due to high viscosity, high curing temperature, and long curing time were the disadvantages of this type of adhesive, but Dexerials has developed low-temperature and fast-curing adhesives in recent years to explore their application to new purposes and new uses.
■ Silicone addition reaction
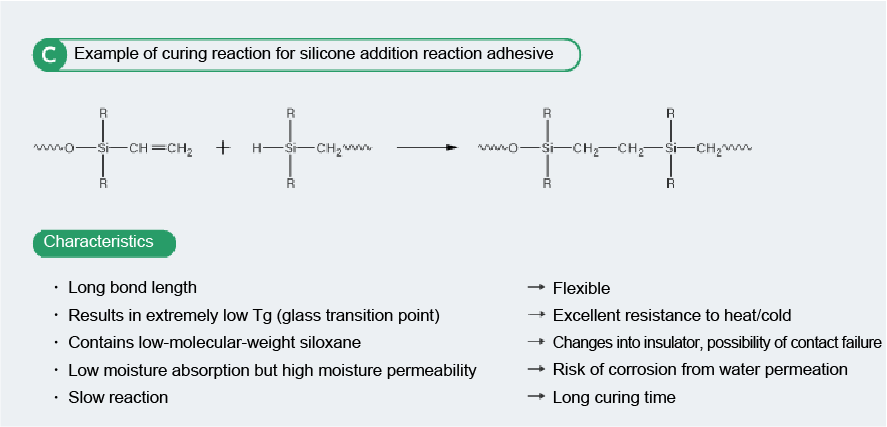
The molecules in silicone addition reaction adhesives have relatively long molecular bond lengths compared to other adhesives, enabling greater flexibility. The glass transition point (Tg) is extremely low, making it possible to create products with a curing temperature tens of degrees below zero. These adhesives are used in many applications due to their ease of use and excellent resistance to heat and cold.
Many silicone types are two-component adhesives and have the advantage of low curing temperatures, but many also have long curing times. In addition, the structure includes low-molecular-weight siloxane, which creates the risk of causing contact failure as time passes after adhesion and the material changes into an insulator. And while silicone is highly water repellent, it also allows moisture to pass through. It is necessary to take these characteristics into consideration when using it in parts with electrical pathways, such as electronic parts.
■ Epoxy thiol
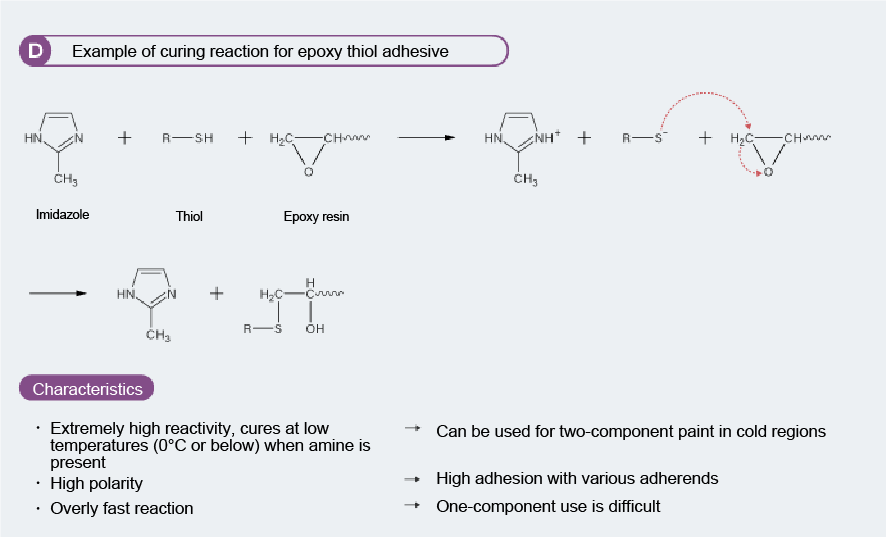
Epoxy thiol adhesives have relatively fast curing reactions compared to other thermo-curable adhesives. They use imidazole and thiol, two materials often used in two-component paint for cold regions, as materials to cure epoxy resin. This combination is marked by reactivity so high that the curing reaction occurs upon mixing even in places where the outside air is 0°C, but this also makes it hard to handle, and making it a one component adhesive has been considered difficult. In recent years, adjustments have been made to the catalyst and stabilizer, leading to the development of a one-component version that features significantly faster curing speed while maintaining curability at relatively low temperatures—performance has been improved to the point where it hardens in seconds at 100–120°C. With the emergence of a thermo-curable adhesive that hardens in seconds, new applications are being developed.
■ Epoxy cationic polymerization
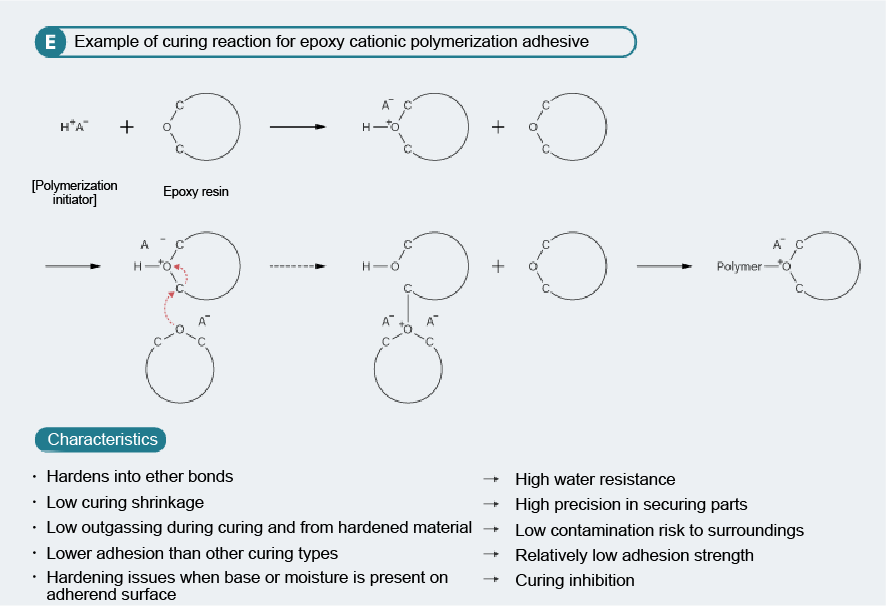
The hardened material resulting from epoxy cationic polymerization adhesives consists of ether bonds, producing significant advantages for precision part adhesives such as high water resistance, low curing shrinkage, and low outgassing during curing. On the other hand, it can cause metal corrosion because the catalyst generates acid and hardening is inhibited if there is base or moisture on the adherend surface. There are many limitations on the methods and parts in which it can be used, such as the fact that the catalyst contains the constituent element antimony, a toxic substance that is difficult to handle. But due to its unmatched performance, it has become an indispensable adhesive for certain electronic parts such as image sensor cap seals and stickers for LCD panel glass.
The aforementioned characteristics of the five types of thermo-curable adhesives are discussed only focusing on their use as adhesives for electronic parts. The advantages and disadvantages of each type change depending on the context—for example, irreversible adhesion results in a stronger bond which is an advantage for securing parts, but is a disadvantage in terms of making repairs. The concepts of adhesion and securing will continue to change as technology advances and lifestyles change, and things currently thought of as disadvantages may become useful advantages as perspectives shift. Dexerials will continue to leverage its expertise and knowledge in adhesives to take on new challenges in adhesives technology and respond to our customers’ needs.
- SHARE