
- 接合関連
3D、2.5Dに対応する車載ディスプレイの最新オプティカルボンディング技術
曲面形状などデザイン性が高まる車載ディスプレイ
ドライビングをより快適にするために、近年、自動車メーカーおよびTier1のサプライヤーは車載ディスプレイの機能向上に力を入れています。従来の車載ディスプレイは、全体に長方形のフラットな形をしたものがほとんどでしたが、最近はインテリアの形状に合わせて表面がゆるやかな曲面形状であったり、「フリーフォーム」と呼ばれる非長方形のディスプレイの開発が進んでいます。そうした新しいディスプレイの開発にともなって、ディスプレイとこれを保護するカバー部材を貼り合わせる「光学貼合」(オプティカルボンディング)にも、新たな技術が求められるようになりました。

「光学貼合」とは、液晶パネルなどのディスプレイモジュールとそれを覆うカバー(トッププレート)を、光学的に透明な材料で貼り合わせることを指します。
トッププレートには通常、ガラス板やアクリル板が用いられますが、ディスプレイとカバーの間に空気の隙間(エアギャップ)があると、屈折率の違いから画像のボケや輝度の低下が発生します。そこでディスプレイとトッププレートの間のエアギャップを埋めて、接着すると同時に、外光の「反射」とパネル内部の映像光の「拡散」を最小限に抑えるために、OCA(Optical Clear Adhesive)やLOCA(Liquid Optical Clear Adhesive)といった高い透明性を持った粘着材料が開発され、スマートフォンなどで広く使われています。
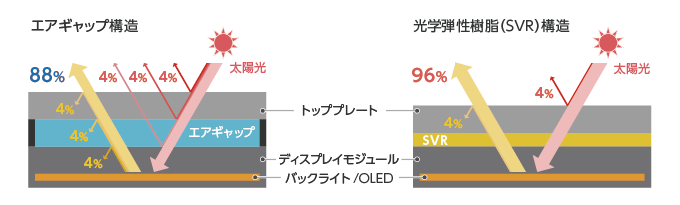
「かまぼこ型」も接着できる液状貼合剤「LOCA」
OCAやLOCAはトッププレートと屈折率を整合し、画面の視認性を向上させるだけでなく、自動車事故などが起こった際にガラス片やアクリル片の飛散を防ぎ、搭乗者の安全に寄与します。また光学貼合することで、ディスプレイの防塵効果、耐湿性も向上することから、多くの自動車メーカーが開発するディスプレイシステムに欠かせない部材となりました。
しかし近年になって、車載ディスプレイの曲面化、フリーフォーム化が進むにともない、OCAでは対応が難しい製品が登場するようになってきました。OCAは形状が平面のフィルムであるため、同じ平面同士を接着するのは得意なのですが、インクの厚みなどに起因する段差を乗り越えて接着したり、曲面を埋めるといった使い方には向いていませんでした。
対照的にLOCAは液体のため、接着したい部品の間に隙間なく充填し、部品同士をしっかりと貼り合わせることができます。次の図のようにLOCAは、カーブを描いた形状のカバーとディスプレイの間に充填し段階的にUV硬化させることで、ピッタリと接着します。このような2.5D、3Dディスプレイの「かまぼこ型」と呼ばれる形状の貼合にはLOCAの使用が向いています。
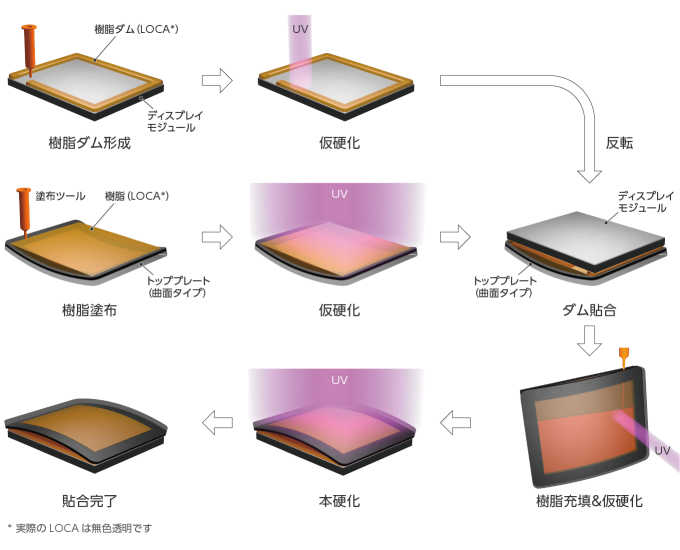
光学弾性樹脂(SVR)シリーズ
デクセリアルズでは業界に先駆けて2007年に光学弾性樹脂(SVR)というアクリルベースのLOCAを開発し、各社の携帯電話やスマートフォンのディスプレイに採用されてきました。2013年にはそれを改良し、トッププレートに塗布してから紫外線で仮硬化させると粘着特性が現れる「ハイブリッドSVR」を開発。SVR同様に視認性の向上を実現するとともに、フィルム状のOCAが持つ作業面での容易性・簡便性を両立した商品として、ハイブリッドSVRも普及が進んでいます。
デクセリアルズのSVR、ハイブリッドSVRの特性を表したのが、次の表です。比較対象の表の右側2つは、他社のシリコーンベースのLOCA、アクリルベースのOCAになります。「★」が多い方が優れていることを示します。
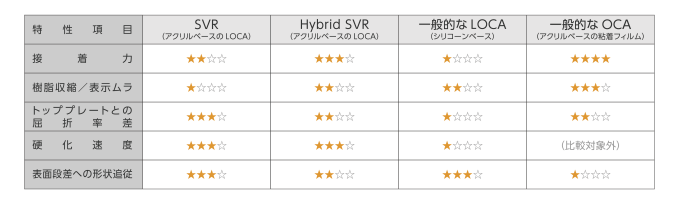
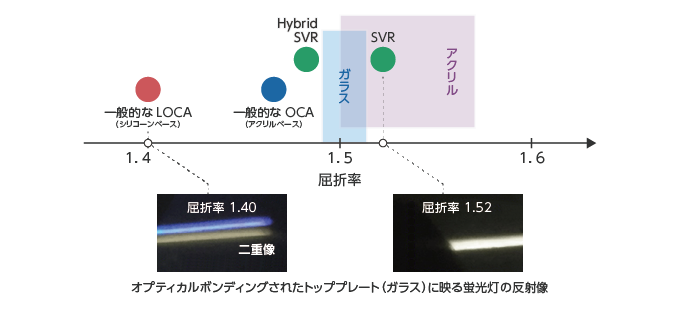
これまで車載用ディスプレイのオプティカルボンディングにはシリコーンベースのLOCAが主に使われてきました。しかしシリコーンベースのLOCAは、ガラスやポリカーボネート製のトッププレートと屈折率の違いが大きいため、空気に比べれば改善されるものの、ボケや二重にものが見えるという現象を完全には解決できずにいました。これに対し当社が開発したアクリルベースのSVR、ハイブリッドSVRは屈折率がガラスとほぼ同じ、ポリカーボネートとも近く、視認性が大きく向上するという利点があります。またシリコーンベースLOCAは、OCAに比べると接着力が弱いという欠点がありますが、アクリルベースのSVR、ハイブリッドSVRはOCAに次ぐ接着力を実現することに成功しました。
高温にも強いアクリルベースの「SVR」シリーズ
次の図は、現在開発されている2.5D、3Dのディスプレイの断面図になります。トッププレートとディスプレイがそれぞれ、平面・曲面によって3パターンあり、それぞれにSVR、ハイブリッドSVRのどちらが貼合剤として適しているかを示しています。これからフリーフォーム化がさらに進んでいくディスプレイは、図の一番右の「ディスプレイもトッププレートも両方曲面タイプ」が増えていくと予想されますが、その接着に対応できるのが二段階で紫外線硬化するハイブリッドSVRとなります。
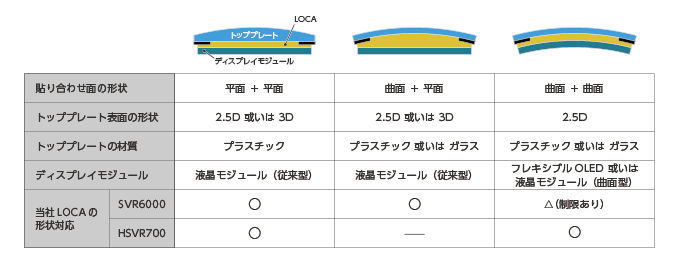
これまで、車載用のLOCAとしてはシリコーンベースのものが主流となってきました。それは一般にシリコーンベースのLOCAのほうがアクリルベースより高温に強かったことが大きな理由ですが、デクセリアルズが開発したSVR、ハイブリッドSVRは95℃・1000時間の耐久テストの結果、品質の劣化が見られず、十分に車載用ディスプレイの貼合剤としての機能を満たしています。私たちは、視認性の向上、デザインの自由度向上とともに、強い接着力を実現したSVR、ハイブリッドSVRの普及をさらに進めていきます。
関連記事
- SHARE
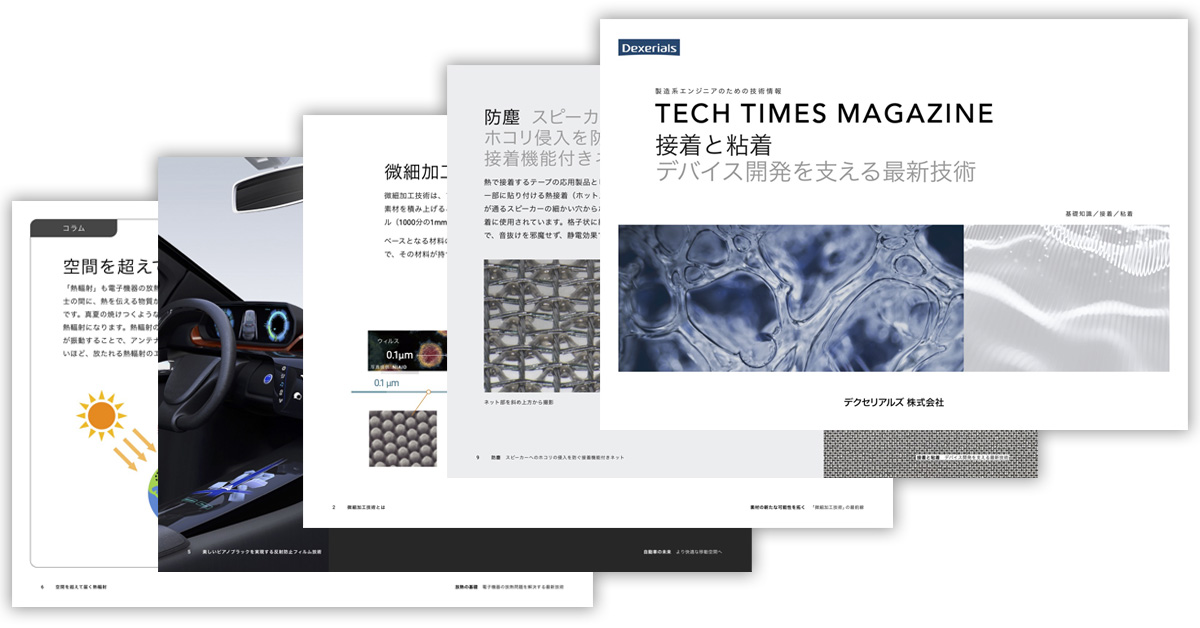
当社の製品や製造技術に関する資料をご用意しています。
無料でお気軽にダウンロードいただけます。
お役立ち資料のダウンロードはこちら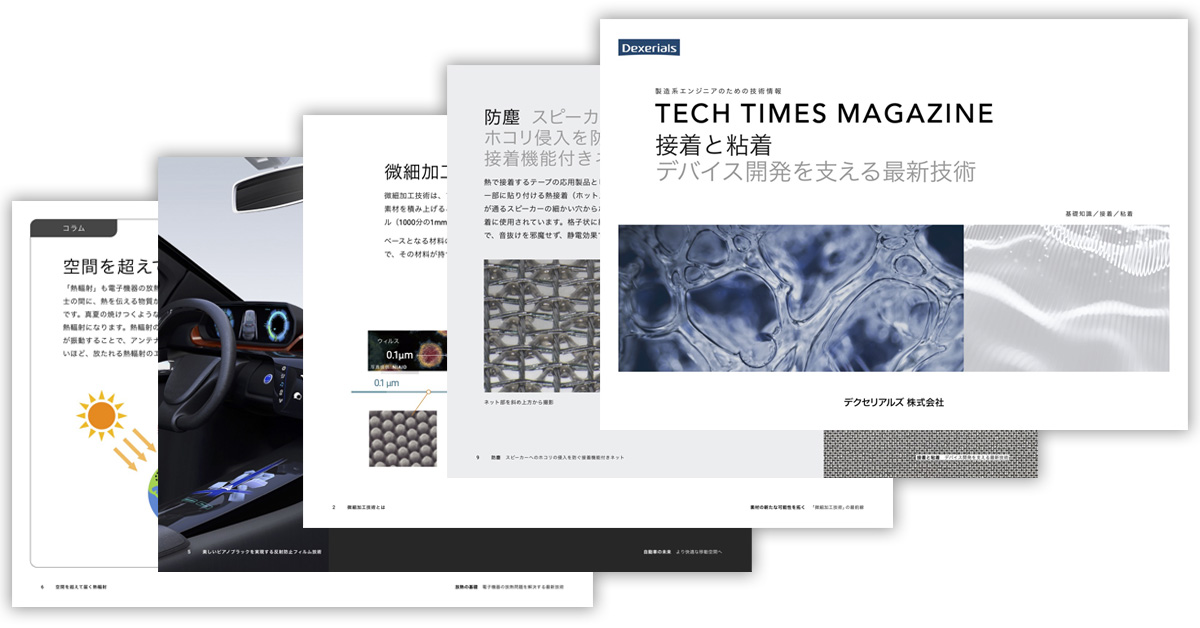
当社の製品や製造技術に関する資料をご用意しています。
無料でお気軽にダウンロードいただけます。
お役立ち資料のダウンロードはこちら