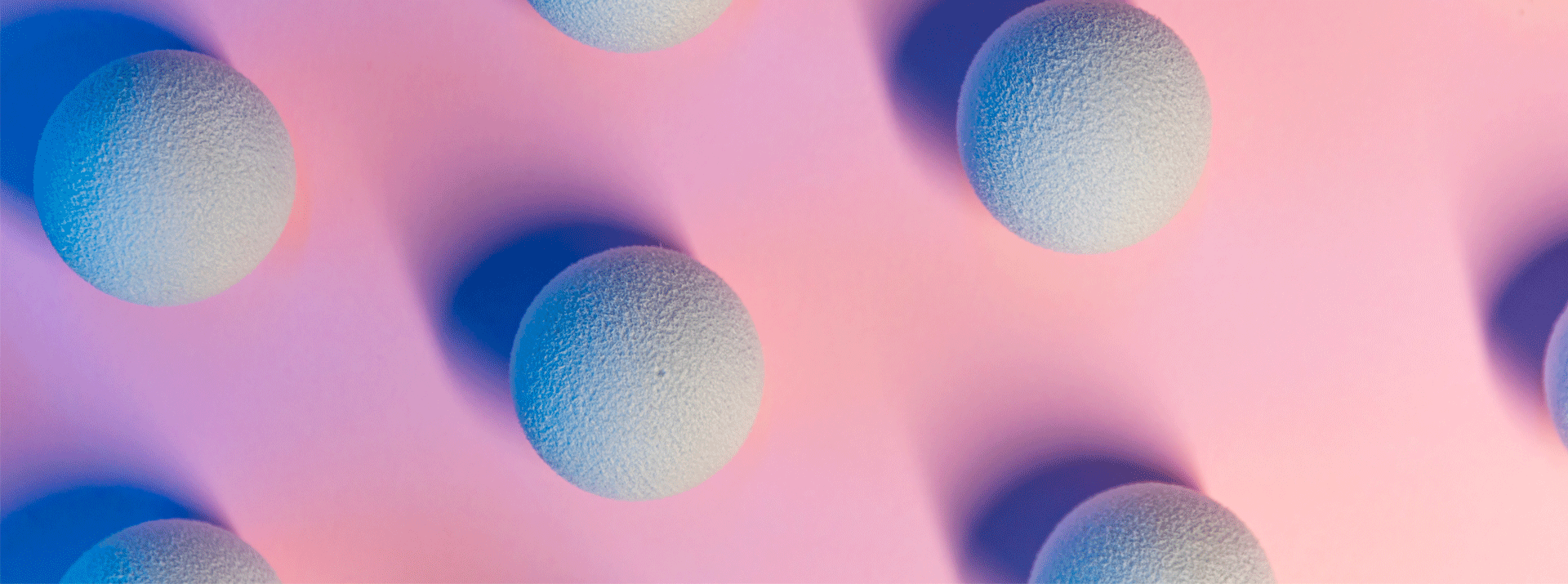
- 接合関連
粒子整列型異方性導電膜「ArrayFIX」の登場がもたらす新しい価値
ArrayFIXによる粒子捕捉の安定
デクセリアルズが2016年に上市した粒子整列型異方性導電膜「ArrayFIX」は、熱硬化性樹脂の中に分散する導電粒子が、一定の距離と配列で整然と並んでいることが特長です。従来型のランダムに粒子が分散した異方性導電膜(ACF)に比べ、その計算された配列により、安定的な端子の接続を実現するとともに、端子間のショートリスクを低減します。
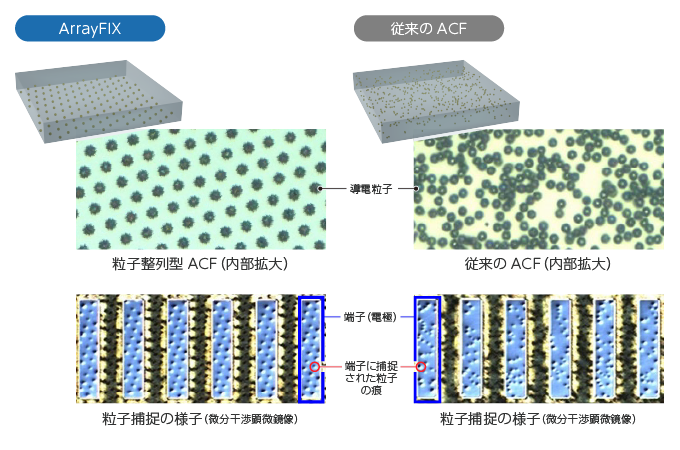
下記の電子顕微鏡写真は、ArrayFIXと従来型のACFを用いてガラス基板にICチップを接続したCOG(Chip on Glass)実装時の端子の断面を観察したものです。注目すべき点は、左右のIC側端子(バンプ)の間に見える粒子です。ArrayFIXはバンプ間に1個の粒子があるだけでこの写真からはショートのリスクは確認できません。一方、従来型ACFは、バンプ間に4つの粒子が存在し、この写真では接触していないもののかなり接近していることが確認できます。粒子同士が接触すると、ショートが起こる可能性があります。なお、断面観察は対象を削って露出した面を観察しているだけですので、写真に向かって奥側や手前側の領域は想像するしかありませんが、この写真からは従来型ACFと比べてArrayFIXはショートリスクが低いと言えます。
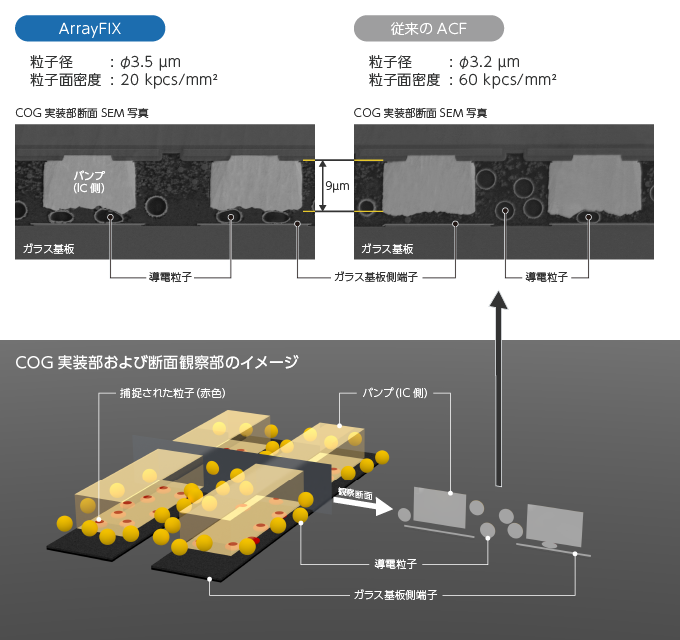
また、観察に際してはArrayFIXの場合はおおよそ粒子の相対的な位置が分かっていますので、断面観察が比較的容易です。これに対して、従来型ACFは粒子位置が事前に特定できないため、一断面だけで接続やショートの状況を説明することは困難です。従来型のACFの断面観察写真では左側バンプが粒子捕捉できていないように見えますが、この断面の手前側か奥側では粒子を捕捉しているはずです。
ACF実装後の出来映え確認の効率化
実際の組立の現場では破壊検査(断面観察)をすることはできないため、微分干渉顕微鏡などの顕微鏡画像を使って出来映え確認が行われています。以下は実装状態の検査に用いられる画像で、左側のグループは人が判定したもの、右側のグループは自動画像検査装置(AOI)が判定のものになり、いずれも同じ検体の同じ部位を判定したものです。
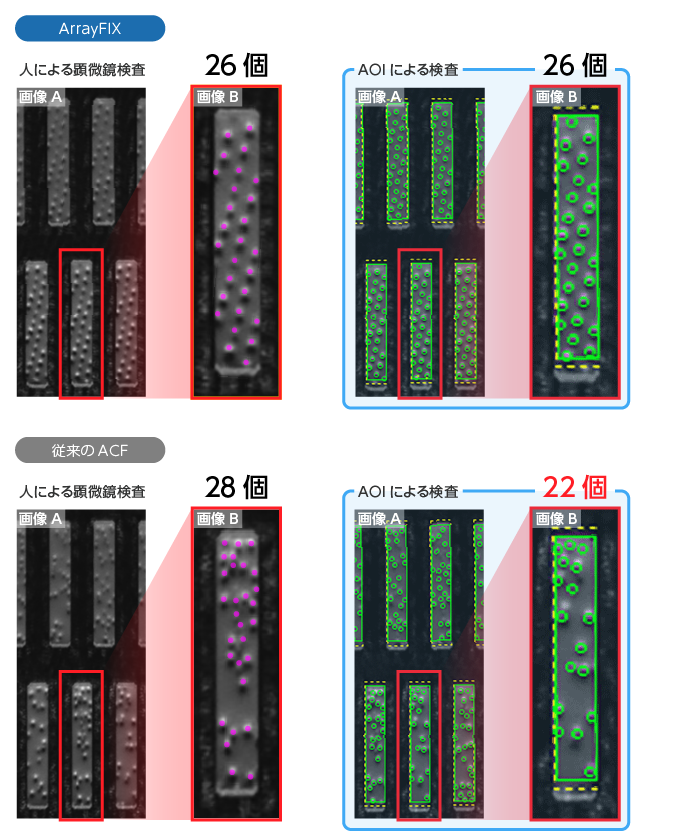
まず、画像の見方を説明します。いずれも画像処理されグレースケールでの表示となっており、縦長の長方形が接続端子、白い点が捕捉されたACF粒子の位置を示す「圧痕(あっこん)」と呼ばれるもので、粒子捕捉の状態が濃淡で表現されています(画像A)。画像Bは画像Aの赤枠の部分を拡大したもので、ピンクの点は人の眼で正常と判定した圧痕、緑の丸は自動画像検査装置(AOI)で正常と判定された圧痕を示しています。
ArrayFIXの接続では、人の目とAOI判定はいずれも26個の圧痕(正常な接続痕)が確認できます。一方、従来型ACFの方では、人の目で28個の圧痕が確認されているにも関わらず、AOIの検査では22個しか確認されていません。これは、複数の圧痕が近い位置にある場合、AOIでは1つの圧痕として判定されてしまうためです。
仮に前述の例において圧痕数の判定基準が24個以上だったとすると、AOI判定がNGとなります。この場合、人による追加の検査が行われ、最終的に28個と判定され検査合格となります。このように、従来型ACFでAOI判定を行った場合、時間あたりの検査数が落ち、加えて追加作業が発生することになります。
ArrayFIXを使用した場合、粒子間隔がほぼ一定に保たれているため圧痕が重複してカウントされることはなく、AOI画像上に圧痕が鮮明に表示されることから誤判定が少なくなり、製品検査の精度向上、検査時間の短縮を図ることが可能になります。
ArrayFIXで粒子捕捉を「設計」−−新しい価値に挑戦する
従来型ACFは導電粒子を分散させていますが、粒子位置を事前に設定することはできません。そのため端子間に捕捉される粒子数については、確率論的分布を持つことになります。ArrayFIXの場合は、決められた位置に粒子があるため、機械設計で使われる公差設計の概念で粒子捕捉をある程度予測することができます。ここがポイントです。これまでは新しい設計にチャレンジする際には、その都度、評価用部材を準備、組み立て、評価を行って設計の妥当性を確認していました。評価がNGの場合には原因を究明して、設計をやり直し、評価OKになるまでこのループから抜けられません。これに対し、粒子捕捉を「設計」できるArrayFIXを使えば、前出のループに陥る可能性は低くなります。ArrayFIXは安定した粒子捕捉やショートリスクの低減と言った接続品質の向上はもちろん、開発期間の短縮やよりよい設計(アイデア)へのチャレンジを可能にします。
デクセリアルズはこれまでACFのトップランナーとしてさまざまな技術を開発、ACFを進化させてきました。今回紹介したArrayFIXは、確率論的粒子捕捉の領域を抜け出し、理想的な接続材料に向けてのステップアップとなる製品です。進化を続けるデクセリアルズのACF、その今後にご期待ください。
”ArrayFIX”及びそのロゴは、デクセリアルズ株式会社の日本およびその他の国における商標または登録商標です。
関連記事
- SHARE
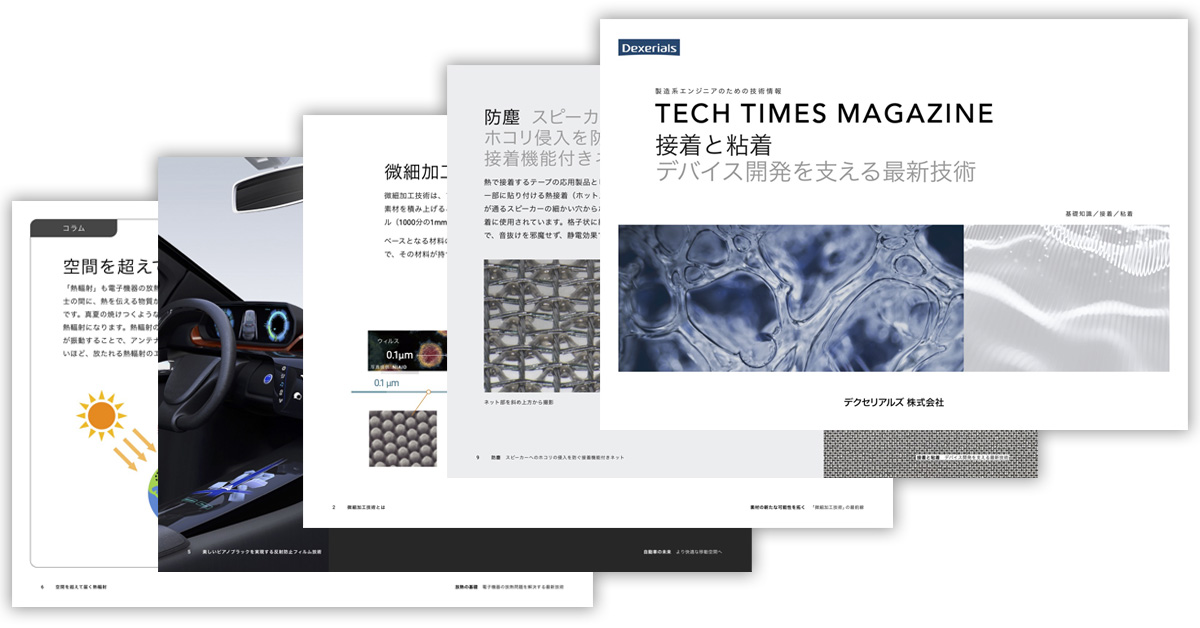
当社の製品や製造技術に関する資料をご用意しています。
無料でお気軽にダウンロードいただけます。
お役立ち資料のダウンロードはこちら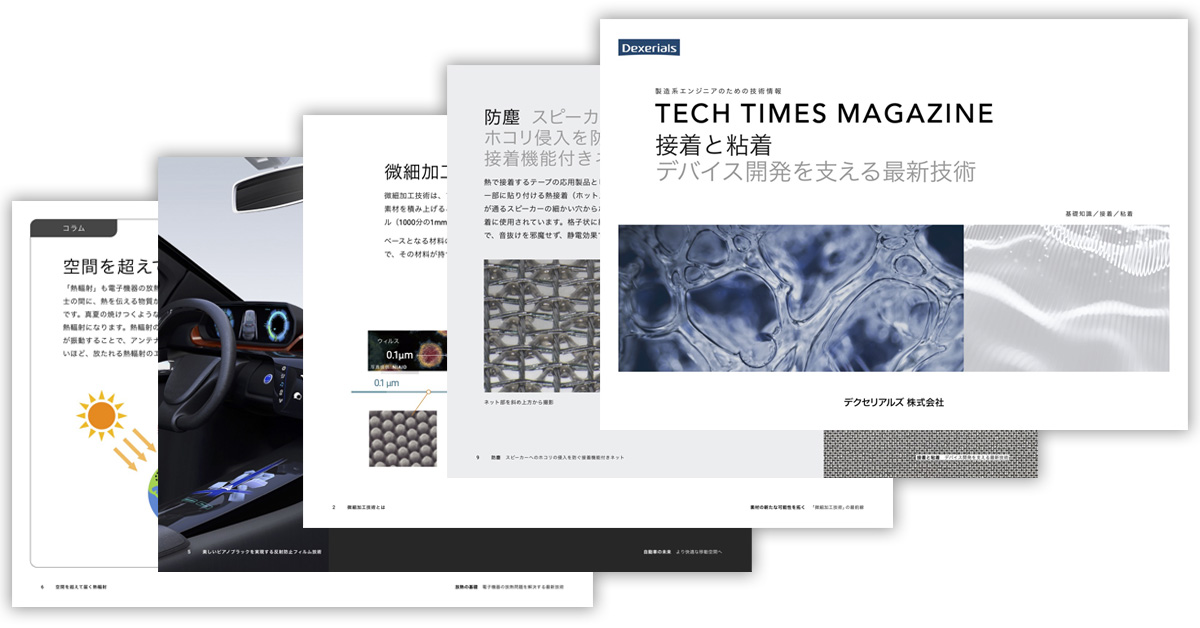
当社の製品や製造技術に関する資料をご用意しています。
無料でお気軽にダウンロードいただけます。
お役立ち資料のダウンロードはこちら