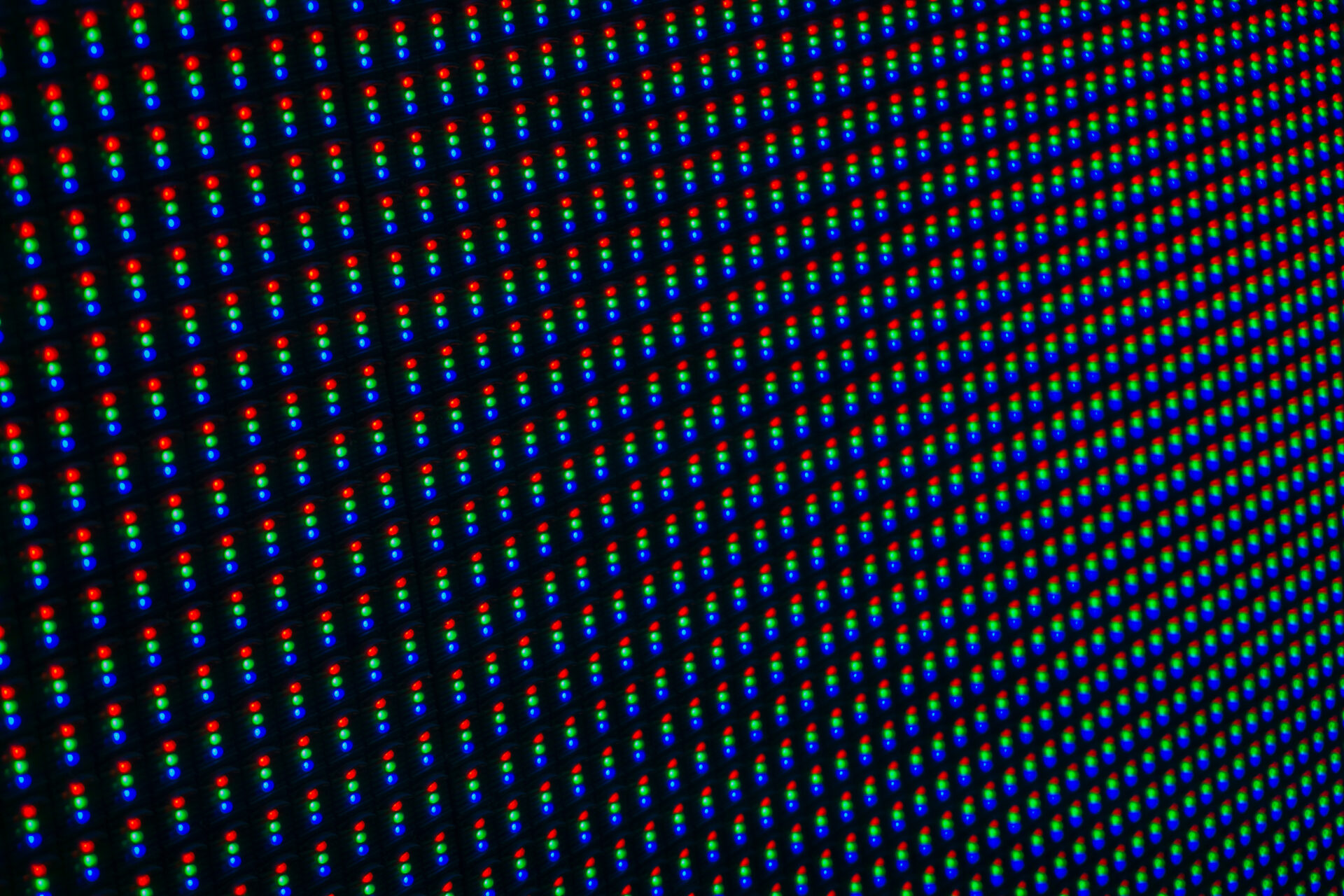
- 接合関連
革新的なマイクロLEDディスプレイの実現: 粒子整列型異方性導電膜「ArrayFIX」
目次
マイクロLEDディスプレイとは
マイクロLEDディスプレイは、世界中のエレクトロニクスメーカーから高い注目を集めるディスプレイ技術です。長い間、研究と開発の対象とされてきたこの技術は、近年、商品化のフェーズに入り、今後普及が加速していくと予測されています。この記事では、マイクロLEDディスプレイの基本的な特性、最新のトレンド、そして直面している課題について掘り下げます。また、デクセリアルズの製品である粒子整列型異方性導電膜「ArrayFIX」がマイクロLEDディスプレイの技術に対してどのような変革をもたらすかについても詳しく説明します。
マイクロLEDチップは、0.1ミリを下回るサイズの超小型LEDチップです。このマイクロLEDチップを使用したディスプレイ技術では、日常生活で見かける照明や信号の光源として使われるLEDをさらに小型化し、ディスプレイパネル全面に敷き詰めます。LEDの特長である高輝度、低消費電力、長寿命を活かしながら、これらの小さなLEDチップを使って精緻な画像を映し出します。
マイクロLEDディスプレイは、各画素の色と輝度を精密に制御することで、絵画のようにリッチな映像を生成します。この技術は、スタジアムで使用される大型ディスプレイと同様の原理に基づいていますが、マイクロLEDディスプレイでは、それぞれの光源をさらに小型化することで、高精細な画像を近距離からも鮮明に表示できます。マイクロLEDチップは、通常のLEDの半分以下、時には1/6以下にまで小型化されています。
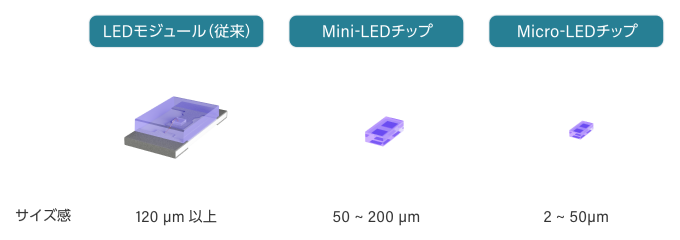
この技術の進化により、マイクロLEDはデジタルサイネージ、テレビ、ウェアラブルデバイス、さらには拡張現実(AR)用スマートグラスなど、多様なデバイスへの応用が検討されています。マイクロLED技術は、より小さく、より精巧なディスプレイの実現を可能にし、今後の電子デバイスの進化に大きく貢献することが期待されています。
マイクロLEDディスプレイの実用化に向けた課題
一方、マイクロLEDディスプレイの普及にはいくつかの課題が存在します。
その一つが価格です。2022年に発売された89インチモデルが約80,000米ドル、110インチモデルが約150,000米ドルで販売された事例が、それを示しています。韓国の大手電機メーカーは、2024年1月現在、TV用途のマイクロLEDディスプレイを販売していますが、価格は依然として高く、一般の消費者が気軽に手を出せる価格ではありません。高価格の要因には、マイクロLEDチップ自体のコストだけでなく、効率的な製造プロセスが確立されていないことが考えられ、製造コストを想定ほど圧縮できていないと考えられます。
LED配列プロセス(マストランスファー)も大きな課題の一つです。マイクロLEDディスプレイを製造する際、800万以上の画素(4Kディスプレイの場合)を構成するために、2400万個以上のRGB各色のLED素子が必要です。これらのLED素子を回路基板上に正確に配置するためには、「Pick and place」と呼ばれる手法で、エラストマースタンプを使用してLEDチップを吸着し、指定された場所に移送するプロセスが用いられますが、一度に移送できるLEDチップの数には限りがあり、その結果、全てのチップを移送するのに非常に多くの時間がかかるという問題があります。
また、点灯率の低さと不点灯部のリペアも製造プロセス上のボトルネックとなってきます。高精細な映像を実現するために使用される小さなLEDチップは、回路基板との接続が難しくなるほど小さくなり、不点灯の割合が増える傾向にあります。LEDチップの不点灯が発生した場合、ドット欠けとなり正しい色表現ができなくなるだけでなく、最悪の場合「画素欠け」して現れるため、部分的なリペアが必要となります。
これらの課題に対処するため、各メーカーはウエハー上でのLEDの一括回路形成といったチップ側での工夫やLEDチップの集約的な転写などの組立プロセス側の技術開発を進めています。また、小型のLEDディスプレイパネルをタイルのように並べて一つの大きなディスプレイを構成する「タイリング」、LEDチップの封止やラミネートなど、製造面での多くの挑戦に取り組んでいます。
マイクロLEDディスプレイの課題を解決する「ArrayFIX」
マイクロLEDディスプレイ技術が進化していく中で、デクセリアルズはマイクロLEDディスプレイの製造において重要な役割を担う製品群を提供しています。光学フィルムや光学弾性樹脂といった製品に加え、ディスプレイを構成する各部品を電気的に接合する際に欠かせない異方性導電膜(ACF)が特に注目されています。その中でも「ArrayFIX」という粒子整列型異方性導電膜は、マイクロLEDチップのような端子接続部の微細化に対応するために開発され、その応用可能性が高く評価されています。
マイクロLED向け「ArrayFIX」の技術
マイクロLEDディスプレイの製造過程で、LEDチップと基板の接続面が狭小化する中、デクセリアルズの「ArrayFIX」はその課題に対応するために進化を続けています。具体的には、導電粒子の径を従来品より小さくし、粒子密度を高めることでより精密な配置が可能になっています。
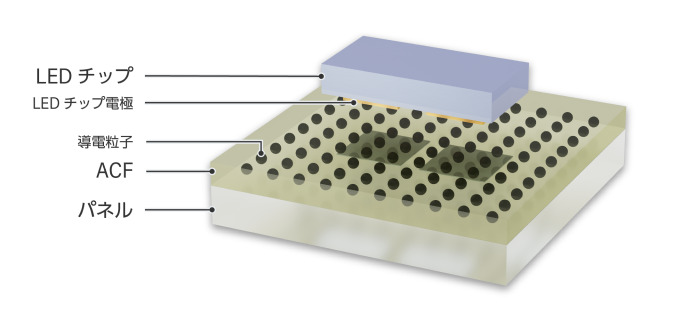
これまでの「ArrayFIX」では、スマートフォンなどの高精細ディスプレイのIC搭載技術である「COG(Chip on Glass)」向けに粒子径φ3.2μm、粒子密度28 kpcs/mm2のものが最も高密度に配置された異方性導電膜(ACF)として提供されていました。しかし、マイクロLED用の「ArrayFIX」では、より高い精密性が求められるため、粒子径をφ2.2μmに小さくし、粒子密度も58kpcs/mm²に増加させて設計しています。
マイクロLED用「ArrayFIX」の特徴は、整列した粒子による安定した接続を実現し、100μm²以下の極小電極への低抵抗接続が可能なことです。さらに、粒子自体がその位置を保持するため、狭小な電極間でも優れた絶縁性を維持できます。
「ArrayFIX」を使用することで、従来のはんだ接合では難しかった低温での実装が可能となり、Au/Snバンプの形成が不要となるため、製造プロセスが簡略化されます。ACFを基板に貼るだけで実装準備が完了し、他の接合方法に比べて前処理が不要なため、大幅な時間短縮とコスト削減も期待できます。また、LEDマストランスファー時には常温から50℃でのLEDの仮固定が可能であり、その後の一括熱圧着で、大型ディスプレイの製造を効率化できます。
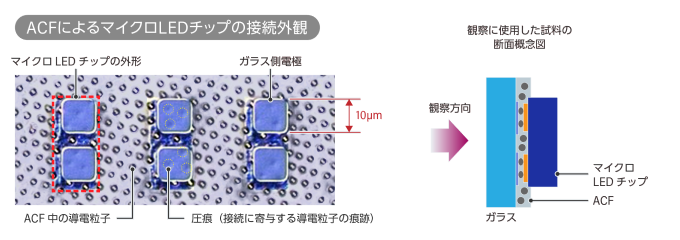
マイクロLEDディスプレイ製造における革新的ACF配置技術
マイクロLEDディスプレイの製造過程において、高精度なチップ実装は製品の品質を左右する重要な要素です。この課題に対応するため、デクセリアルズは微小な個片ACFを任意の箇所に正確に配置する革新的な方法を開発しました。この技術の中心となるのが、ミクロンレベルで個片化された「ArrayFIX」です。
具体的には、レーザーを使って実装が必要な部分のみにACFを転写する技術を考案しました。この方法により、必要な箇所にのみACFを配置し、LEDチップを回路基板上に高精度で実装することが可能となります。
さらに、この技術の応用として、特定のLEDチップとその周辺のACFをレーザーで除去した後、新たに個片ACFを任意の箇所に転写し、再圧着するプロセスも検討しています。これにより、ディスプレイの品質向上や製造効率の改善が期待できます。
また、この技術は基板接続部にのみACFを転写することが可能であり、透明マイクロLEDディスプレイの製造など、さらなる応用分野の開拓も進めています。
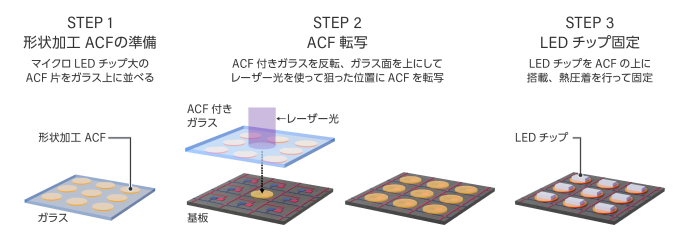
デクセリアルズは、これらの最先端技術を用いて、皆さまの生活を便利で豊かなものにするための技術開発に引き続き注力していきます。
関連記事
- SHARE
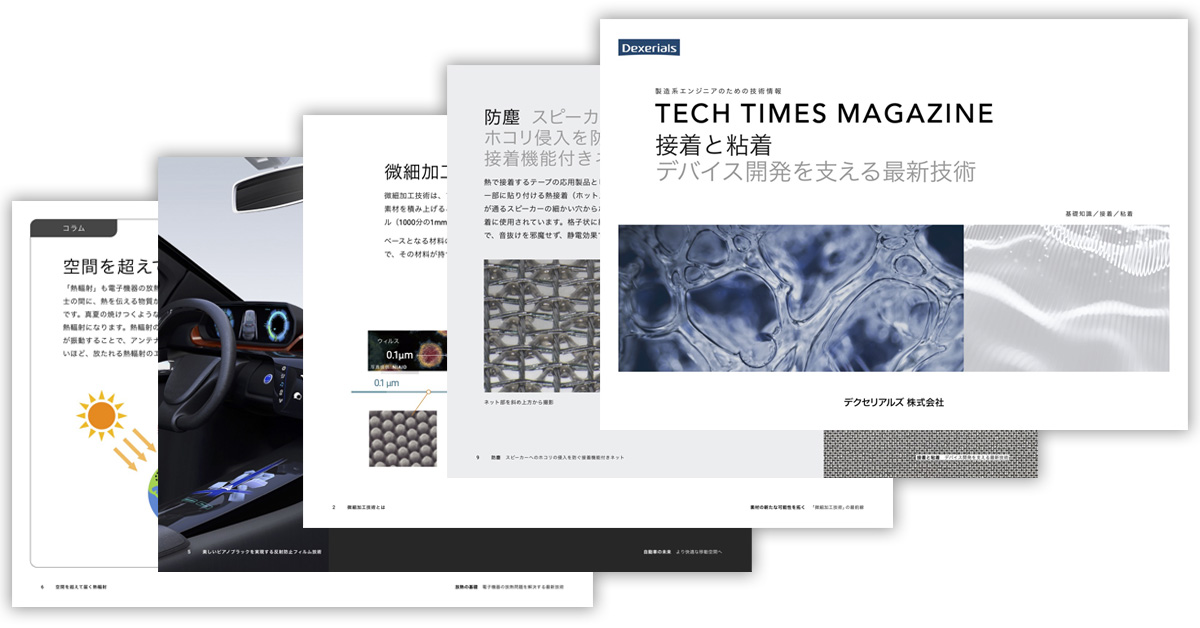
当社の製品や製造技術に関する資料をご用意しています。
無料でお気軽にダウンロードいただけます。
お役立ち資料のダウンロードはこちら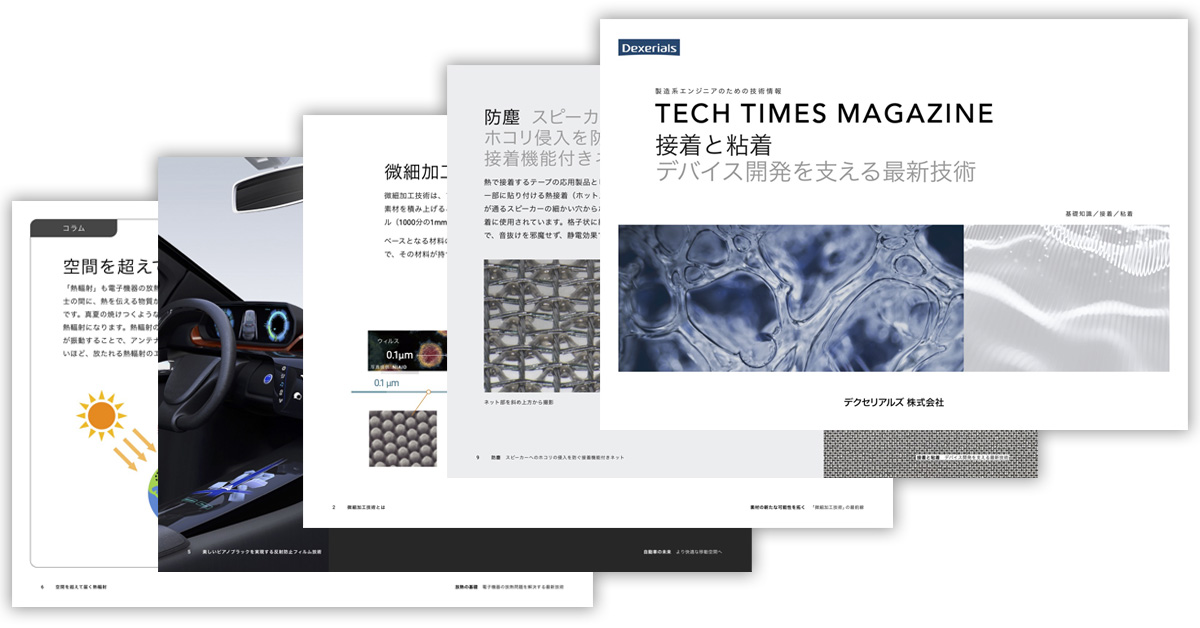
当社の製品や製造技術に関する資料をご用意しています。
無料でお気軽にダウンロードいただけます。
お役立ち資料のダウンロードはこちら