
- 接合関連
接着テープの特徴とその用途
耐熱性に優れる接着テープ
デクセリアルズでは「粘着テープ」と「接着テープ」の2種類を生産販売しています。文字通り粘着テープには「粘着剤」が、接着テープには「接着剤」が、基材と呼ばれる芯材やフィルム上に塗布されています。
粘着剤は接着剤に比べて、緩やかに部品を固定する役割が求められ、一度貼り付けた後でもはがせるのが特徴です。それに対して接着剤は、より強力に部品を固定し、基本的に一度貼ったら剥がせないように設計されています(剥がそうとすると、物そのものが壊れてしまう可能性があります)。また、接着強度の他にも接着テープと粘着テープには、次のような違いがあります。
- 粘着テープの粘着剤は貼り合わせの前後で物性が変化しないが、接着テープの接着剤は温度や湿度、紫外線などの刺激によって硬化し物性が変化する(それによって被着物を固定する)
- 被着体の形状の自由度が違う。粘着テープは平滑な面同士を貼り合わせることに向いているのに対し、接着テープは多少の凹凸や複雑な表面形状の被着体を貼り合わせることができる。
- 接着テープは強力に被着体を固定するため、応力による変形やズレが少ない。
- 接着、粘着後の耐熱性が違う。接着テープは粘着テープに比べて、高温でも接着状態を維持できる。
- 保管温度が異なる。一部製品を除いた一般的な熱硬化型接着テープは常温でも固化してしまうため、基本的に冷蔵で保管する必要があるのに対し、粘着テープは常温で保管が可能。
接着テープが活躍するフレキシブルプリント回路(FPC)
デクセリアルズの製品が利用されている電子デバイスで、接着テープがよく使われるのが、フレキシブルプリント配線板(略称FPC:Flexible Printed Circuitの略)の接着です。FPCとは、非常に薄いフィルムの上に電子回路用の配線を組み込んだ基板のことを指します。フィルムは自由な形に折り曲げることが可能なことから、繰り返し開け閉めされる携帯電話の可動部や、スマホ等の小型電子機器の狭い筐体内の配線に欠かせない部品となっています。接着テープは、このFPCにICやLSI等の部品を載せるために裏打ちされる、補強板を接着する箇所で使用されています。補強板があることで、FPCへの部品の実装が容易となり、製品の修理等の際に、基板を取り外しやすくなるメリットがあります。
またFPCに使用される接着テープは、導電性フィラーを混ぜることで導電性を持たせることもよくあります。ステンレスなどの金属製の裏打ち材を導電性の接着テープで基板のグラウンドに接続することにより、回路で発生するノイズを逃がすことができるからです。
FPCの上に部品を実装するために「リフロー」というはんだづけの工程が必要となります。リフロー工程では、粉末状にしたハンダに松脂などを混ぜてクリーム状にしたクリームはんだを基板にあらかじめ印刷しておき、そこに部品を載せて、最高到達温度が260℃ほどの「リフロー炉」をくぐらせることではんだを溶融して部品を組み上げます。その際に、接着テープが接着している補強板の部分も高温となるため、十分な耐熱性が求められるのです。
スピーカー内部のホコリ侵入を防ぐ接着フィルム
熱接着テープの応用技術としてデクセリアルズが開発したのが、各種のスピーカーに貼り付ける熱接着(ホットメルト)スピーカー用防塵ネットです。スピーカーには音を通すために細かい穴が空いていますが、使用にともないそこから細かいホコリやチリが侵入して、故障の原因となる可能性があります。当社のスピーカー用防塵ネットは、格子状に細かくメッシュが入ったフィルムを熱接着で貼り付けることで、スピーカーの音抜けを邪魔せずに、ホコリ・チリの侵入を静電効果によって防ぐことができます。

以上、デクセリアルズが製造販売する、接着テープ・接着フィルムの特徴と使われ方を簡単に解説しました。接着テープと粘着テープには、それぞれに適した用途、箇所があり、また十分な接着能力を発揮するために生産工程ごとの細かな調整も必要です。電子部品の接着などでお困りのことや不明な点があれば、ぜひお気軽にご相談ください。
関連記事
- SHARE
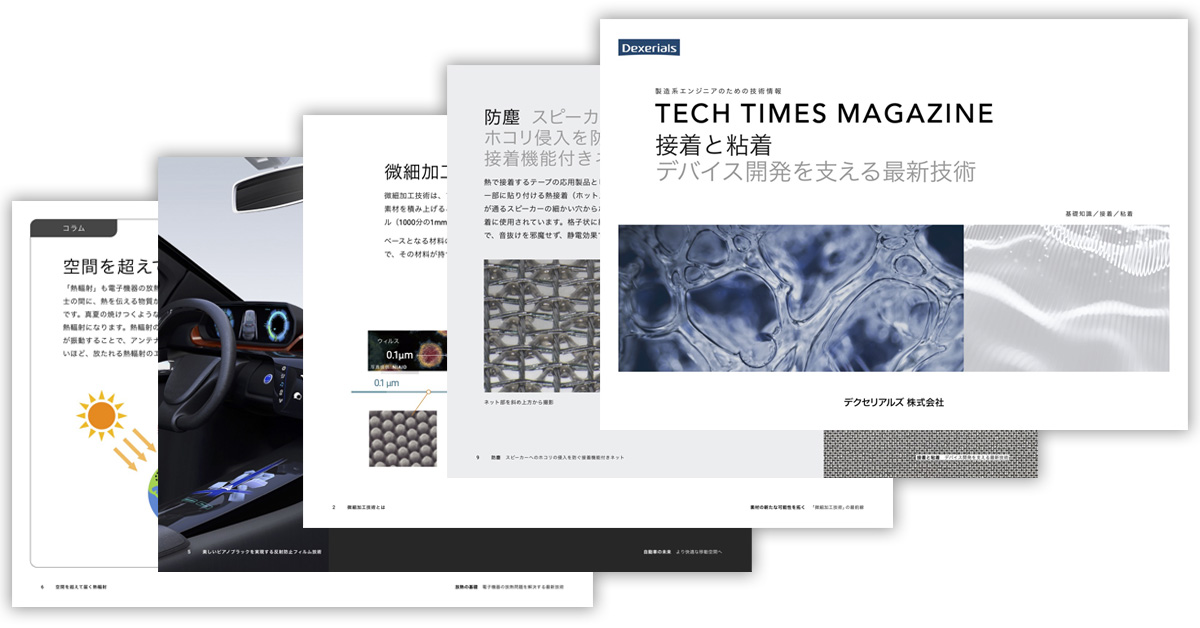
当社の製品や製造技術に関する資料をご用意しています。
無料でお気軽にダウンロードいただけます。
お役立ち資料のダウンロードはこちら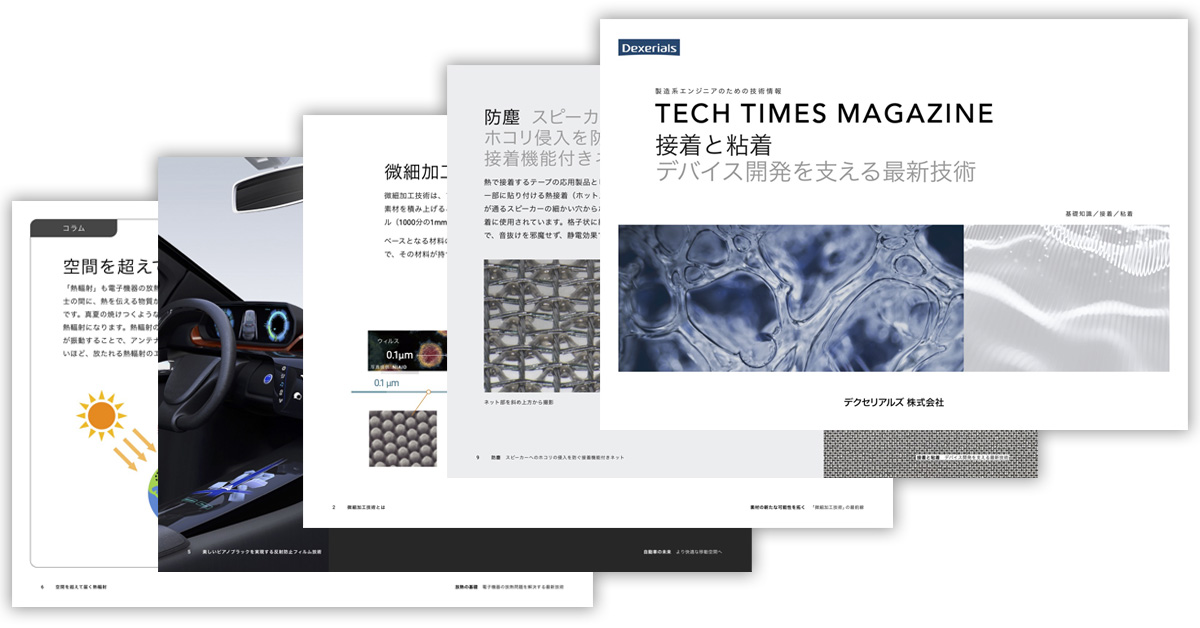
当社の製品や製造技術に関する資料をご用意しています。
無料でお気軽にダウンロードいただけます。
お役立ち資料のダウンロードはこちら