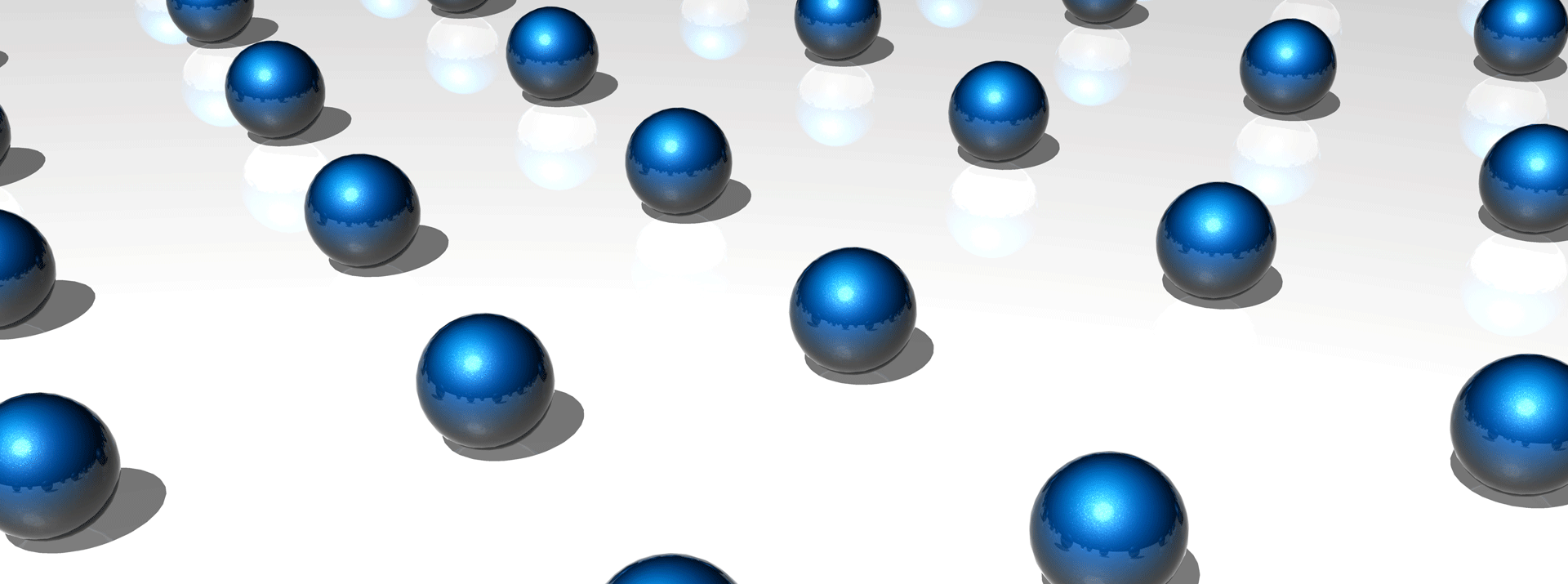
- Bonding Products
The benefits & background of ArrayFIX, a particle-arrayed ACF
Contents
History of the development of the ACF
In 1977, the company preceding Dexerials Corporation, Sony Chemicals, pioneered the development of anisotropic conductive film (ACF) made for IC connections. An ACF, which consists of fine conductive particles dispersed in a thermosetting resin, is a material that can connect many electrodes at once by applying heat and pressure. More than 40 years after its development, the ACF has undergone various improvements and is now an indispensable part of digital displays.
The below timeline shows the progression of material and size of conductive particles in ACFs. The first ACF employed carbon fiber conductors about 100 µm in size. A few years later came ACFs employing metal particles of 50 µm in diameter, about half the size of the original ones. In 1988, conductive particles plated with nickel or gold on resin were designed and used to connect glass substrates with ICs (integrated circuits).

In the 1990s, the technology to apply an insulating coating to the surface of the particles was developed. When the conductive particles are trapped between opposing pads, it removes the coating to create electrical connections while the particles that are not trapped retain their coating and maintain insulation. This mechanism prevents short circuits between adjacent pads, making it possible to accommodate small ICs and multiple pads with narrow pad spacing. In the early 2000s, demand for ACFs exploded as the transition from CRT to LCD TVs took off. It is no exaggeration to say that ACFs are now an essential material for digital displays.
The graphic below shows ACF applications in LCD TV and smartphone displays. ACFs are generally used to connect the display panel to the flexible substrate that sends signals to the panel, or to the IC. ACF applications include:
- COG (Chip-on-Glass), connection between the IC and the glass substrate
- FOG (Flex-on-Glass), connection between the flexible substrate and the glass substrate
- FOB (Flex-on-Board), connection between the flexible substrate and the rigid substrate
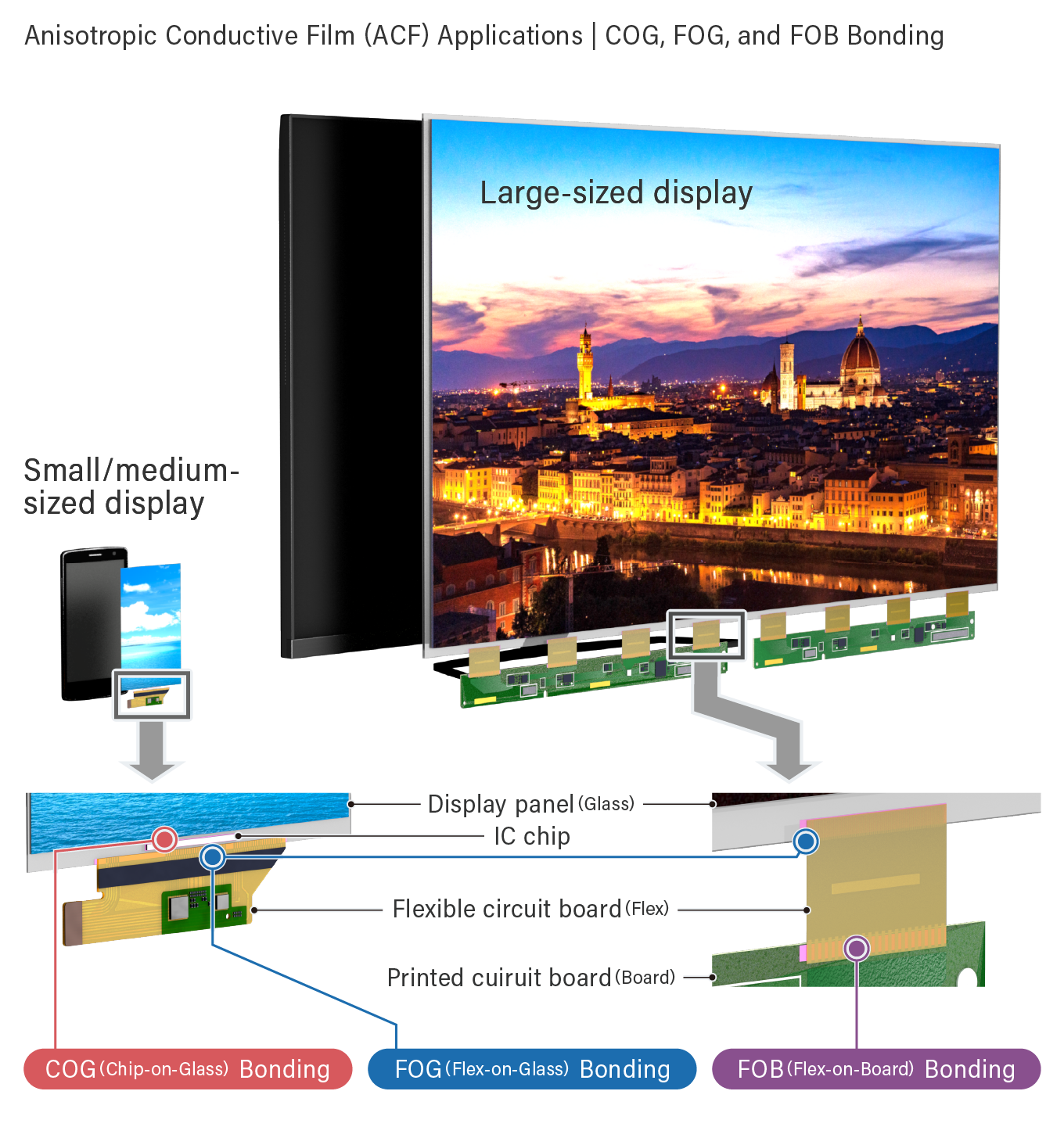
ArrayFIX, an anisotropic conductive film with aligned particles
A further breakthrough in ACF technology occurred in 2014. As fine pitch circuits emerged, the particles in ACFs continued to get smaller. In 2016, “ArrayFIX” was launched as a new ACF that had aligned conductive particles in the resin. Applications included, but not limited to, high-end smartphones, wearable devices, and automotive displays that use organic light-emitting diodes (OLEDs) in addition to conventional LCDs. The use of ArrayFIX is expanding in devices that require highly reliable fine pitch connections.
The image below shows the dispersion of particles inside a conventional ACF (left) and ArrayFIX (right). In the conventional type, the small particles are randomly dispersed, whereas in ArrayFIX, the particles are neatly aligned on a flat surface at regular intervals. This kind of fine control of particle alignment within the resin requires special technology, which is unique to Dexerials.
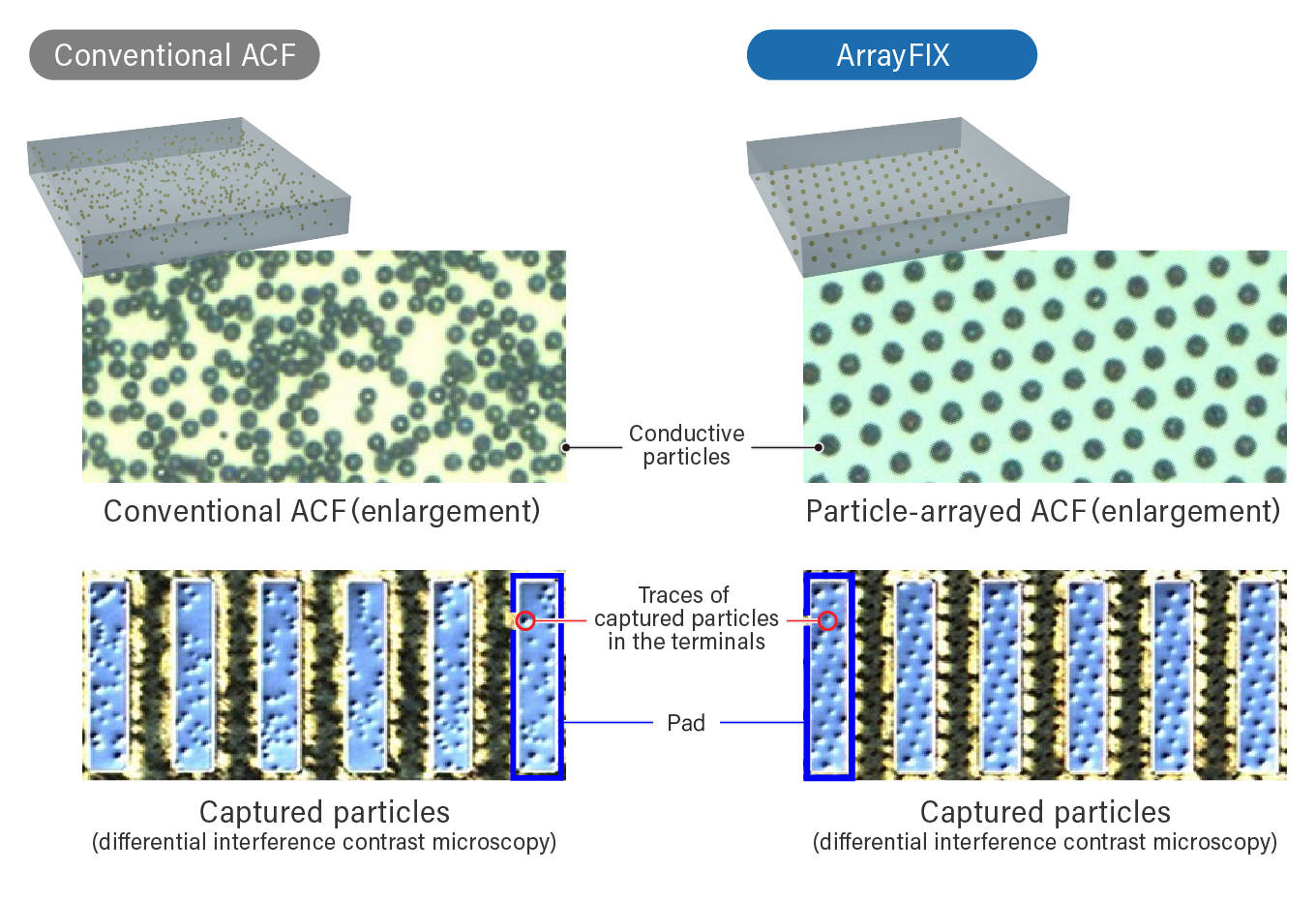
The greatest advantage of this arrangement of conductive particles at regular intervals is that it ensures conductivity and reduces the risk of short circuits between pads. The circuit boards are becoming increasingly fine pitch, the area of connecting pads is becoming smaller, and the spacing between them is becoming narrower every year. In response, the amount of conductive particles in conventional ACFs has increased so that more than the standard number of particles are trapped even in the smaller pads. However, this means that there are more particles between pads with narrow spacing, increasing the possibility of a short circuit. In contrast, ArrayFIX, where the particles are arranged in an orderly fashion, reduces the risk of a short circuit due to particle-to-particle contact between pads. This is because the particles are far enough apart to be safe, while at the same time trapping a sufficient number of particles in the pads to provide conductivity.
Simulated particle trapping
Due to its ability to reliably trap particles and reduce the risk of short circuiting as described above, ArrayFIX is being used in high-end smartphone displays and in automotive displays. Another advantage of the ArrayFIX is that it is easy to forecast the number of captured particles. This is because the number of trapped particles per pad in conventional ACFs follows a probability distribution, whereas in particle-arrayed ACFs, the position of the particles is designed and determined in advance, enabling very stable particle capture. The wiring and pads can be designed on a computer in advance, which allows customers to verify their designs in a short period of time leading to a shorter development period.
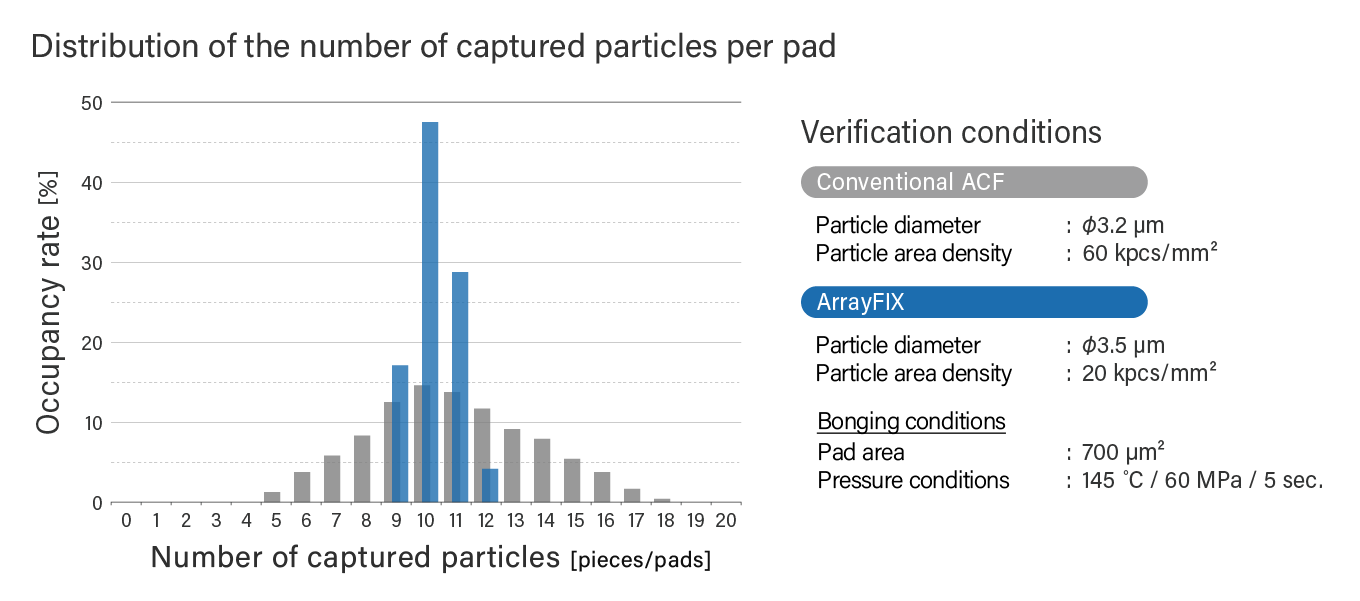
Dexerials currently offers three major types of the ArrayFIX: the PAF300 series, PAF400 series, and the PAF700 series. They differ in particle size, distance between arrays, and curing temperature of the base adhesive, making them suitable for a variety of applications.
Since its launch in December 2016, the demand for ArrayFIX continues to grow for flexible OLED devices, which require COP (Chip on Plastic) connections. Dexerials is certain that the use of ArrayFIX will continue to grow as the OLED market expands.
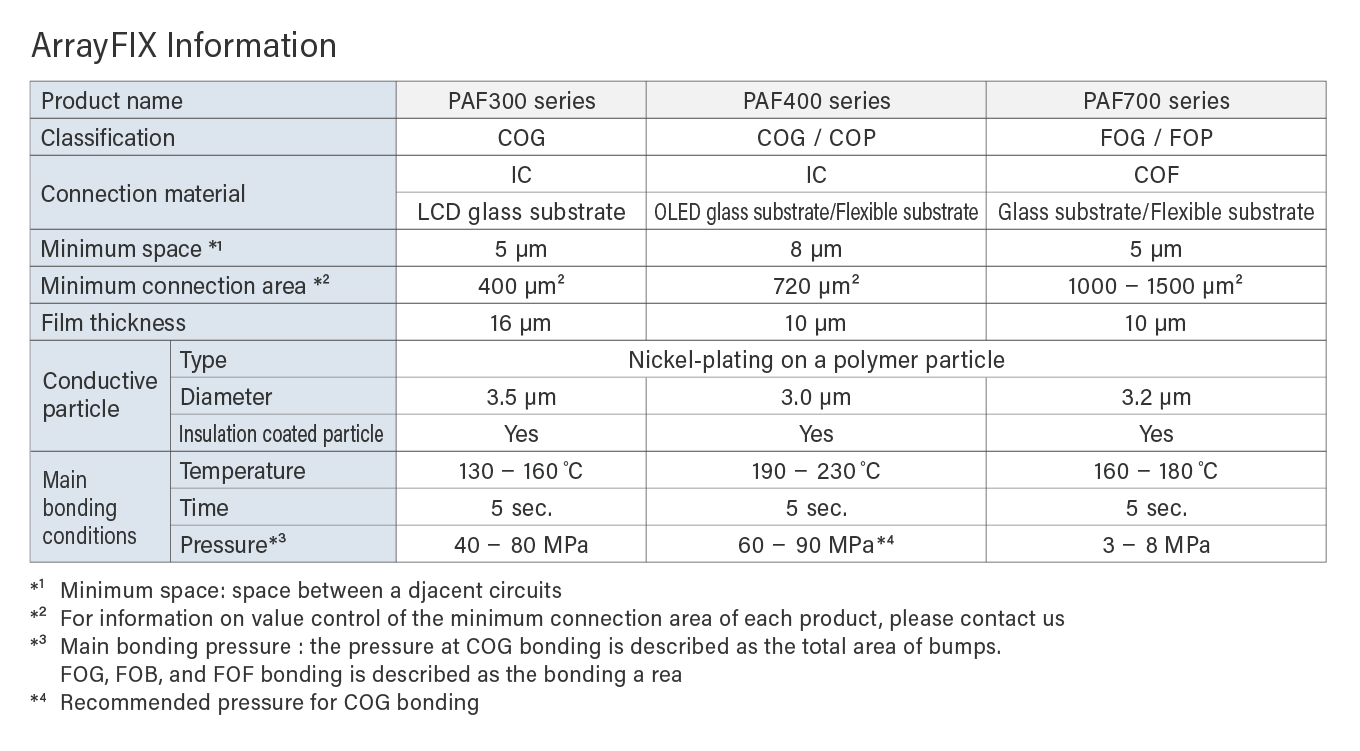
ArrayFIX and its logo are registered trademarks of Dexerials Corporation in Japan and in other countries.
- SHARE