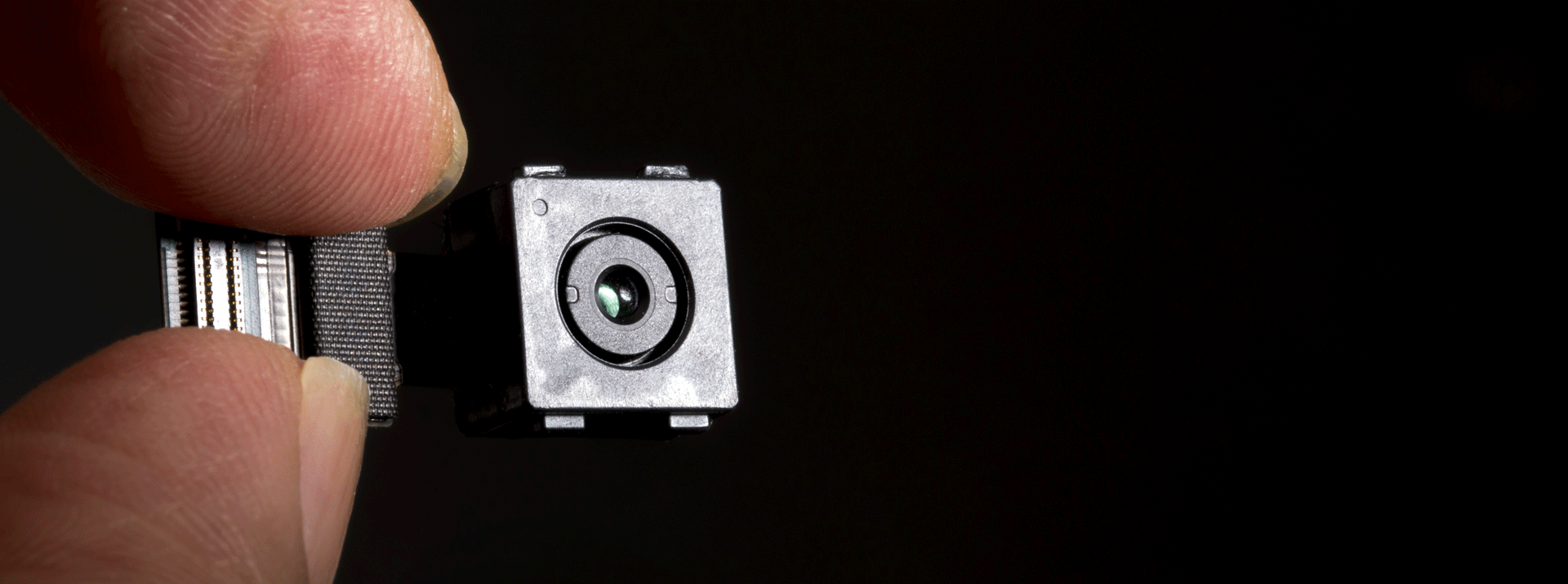
- Bonding Products
New ACF applications – from displays to camera modules
Contents
Main applications of Anisotropic Conductive Films (ACFs)
Anisotropic Conductive Film (ACF) is an adhesive that fixes and electrically connects electronic components such as ICs (integrated circuits) to circuit boards. Conductive particles are dispersed in a thermoset resin. By applying heat and pressure, the conductive particles are sandwiched between pads, creating electrical conductivity between the opposing pads. As ACFs can adhere, conduct, and insulate, their use as a bonding material is increasing, replacing conventional solder and connectors. In particular, they have been utilized to connect electrical circuits in smart cards, displays that require fine pitch connections (where fine wires are connected simultaneously), and in touch panels that require low-temperature connections.
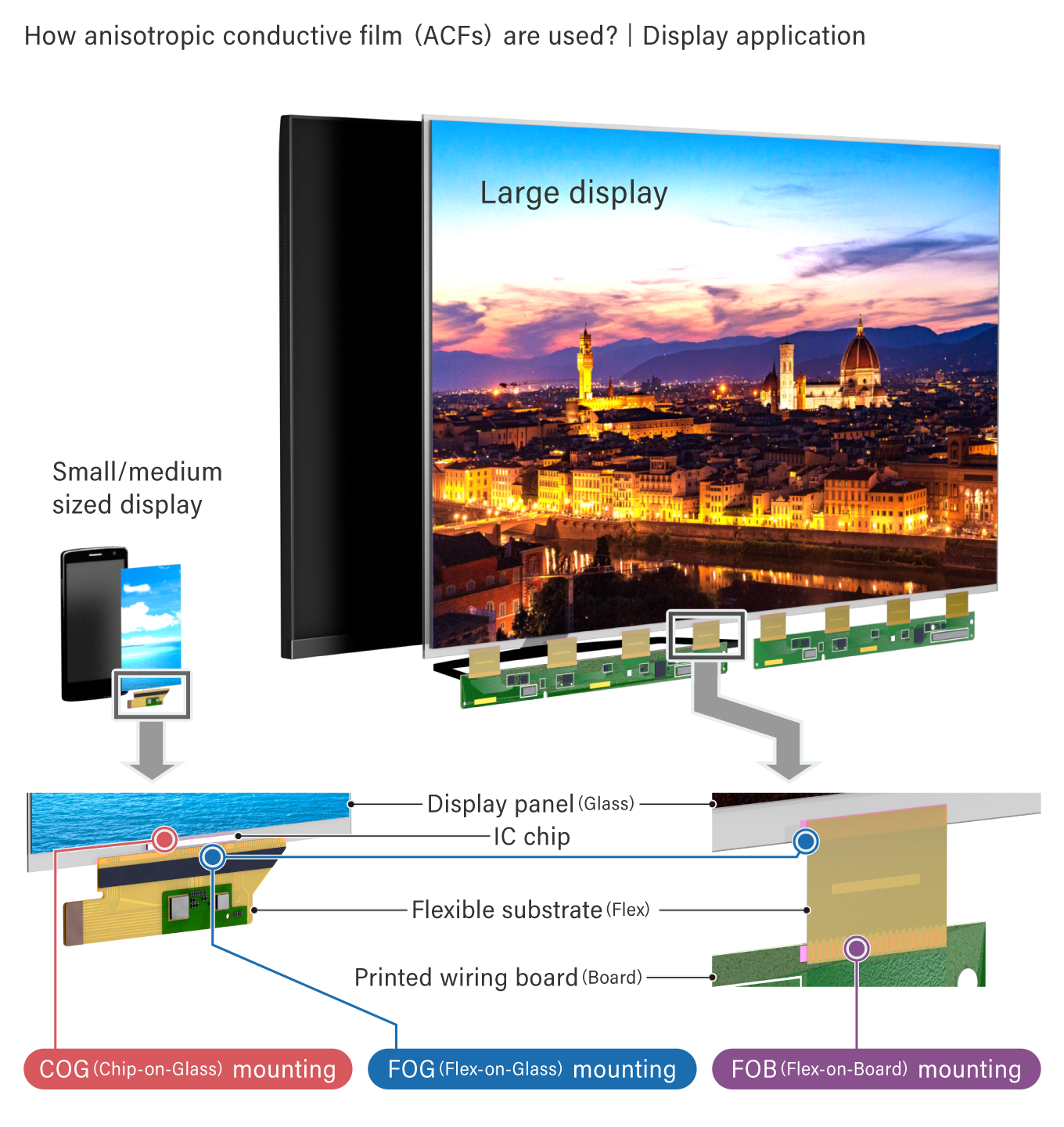
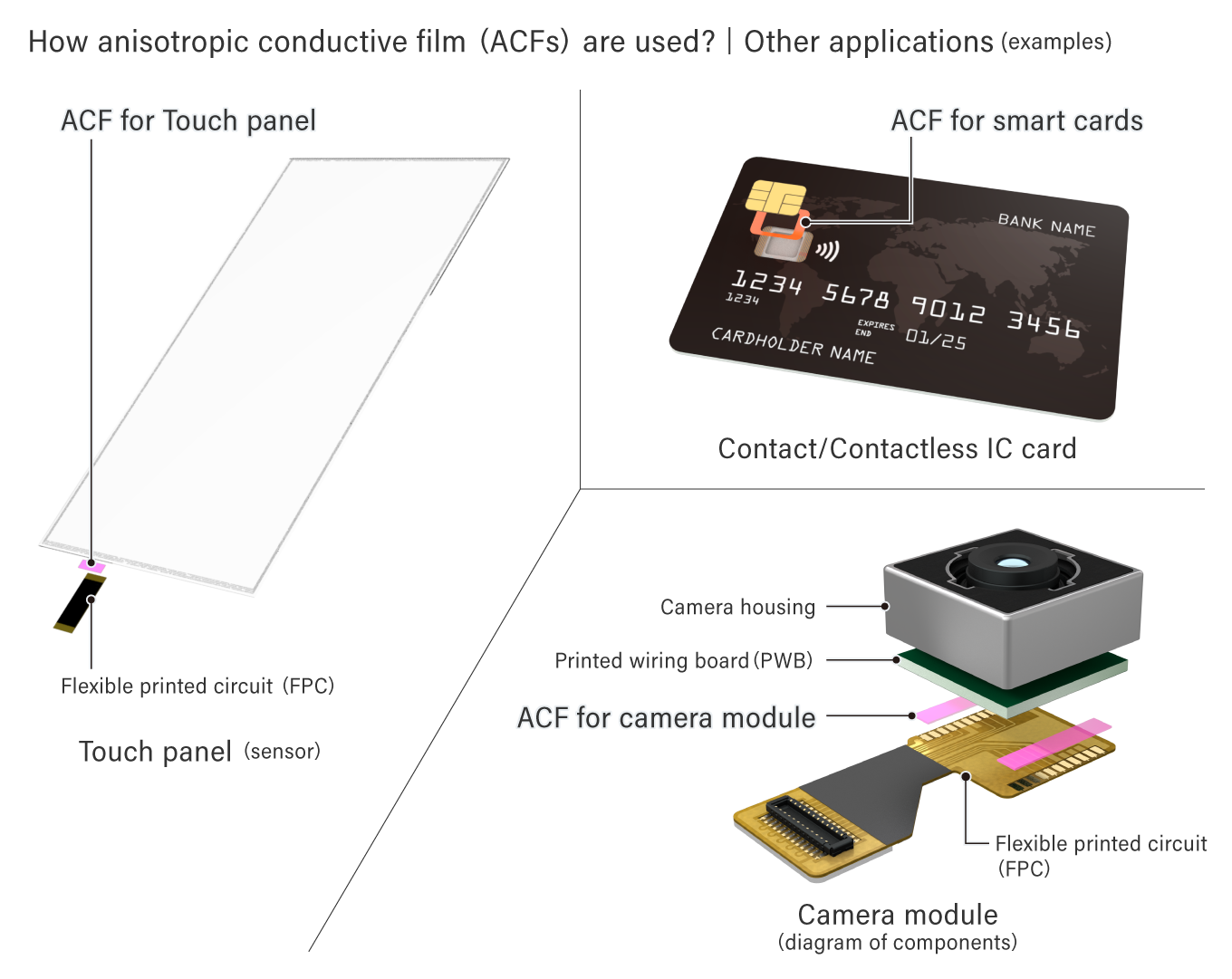
In recent years, ACFs have also been used as an adhesive in camera modules for smartphones, tablets, in-vehicle and security cameras. This article describes the features of ACFs used in camera modules.
ACFs used in displays vs. ACFs used in camera modules
Camera modules have fewer connecting pads than displays and other devices. In large displays, such as large-screen TVs, the number of pads connected by ACFs increases as the number of pixels increases. Depending on the product, thousands of pads may be connected simultaneously in a single unit. In comparison, camera modules have only a few dozen pads, and each pad area is large.
The size of conductive particles in ACFs used for camera modules and for display connections is different. For camera modules, the ACF’s conductive particles are relatively large, approximately 20 microns (μm) in diameter while conductive particles in ACFs used in displays are only a few microns in diameter.
Compared to glass substrates used in displays, the bonding area of components and substrates used in camera modules are not as flat as the ones in glass or ICs. Depending on the structure and size of the component used, some components have distortions such that the degree of flatness of the bonding area exceeds 20 μm. Hence, there is a need for larger particle size for ACFs used for camera modules.
The reason for the higher distortion of ceramic circuit boards and printed circuit boards compared to glass substrates, which are used in displays, is due to the difference in manufacturing methods. Glass substrates are single-layer and made by solidifying liquid raw materials, which results in flat surfaces. On the other hand, circuit boards with a multilayer structure, such as ceramic substrates, are laminated and integrated with multiple layers of materials with different thermal and mechanical properties, which inevitably cause distortion. In the case of ceramic substrates in particular, the ‘firing’ process causes relatively large distortions as the substrate shrinks like porcelain. In addition, for camera modules, a window-like space is required to avoid the sensor section, which also contributes to distortion.
As shown in the illustration below, in case of connecting circuits, ACFs conduct electricity when the conductive particles are sandwiched and trapped between opposing pads. If conductive particles with a small diameter are used on a board with a non-flat crimped area, the particles may not get trapped, and thus, conductivity may not occur. For this reason, ACFs used in the assembly of camera modules employ conductive particles with a larger diameter than the conventional ACFs used in displays.
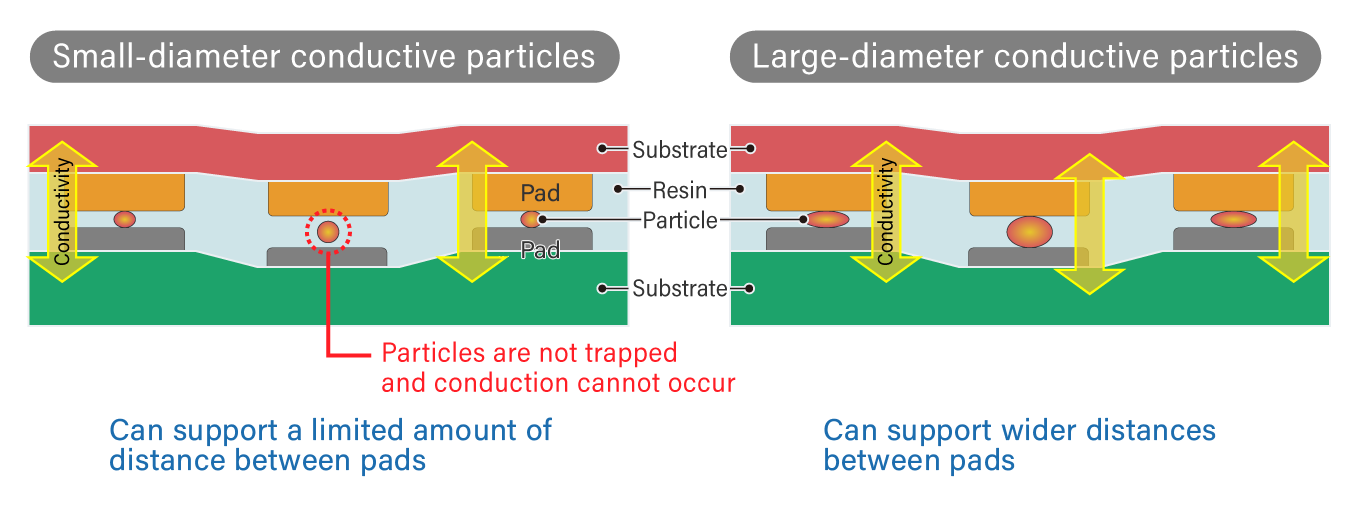
To verify the effect of large-diameter conductive particles, Dexerials tested a ceramic substrate with a distortion of approximately 40 µm and two types of ACFs with conductive particles of different diameters. The two graphs below show the resistance of individual circuits connected by ACFs with conductive particles ~10 µm- and 20 µm-diameter. On the top graph (“10 µm-diameter particles”), the values in the area outlined by the red dotted line are high, meaning that the circuit is not connecting well. In contrast, the lower graph (“20 µm-diameter particles”) shows that all the pads have almost the same resistance value, indicating normal conductivity even when the substrate is distorted.
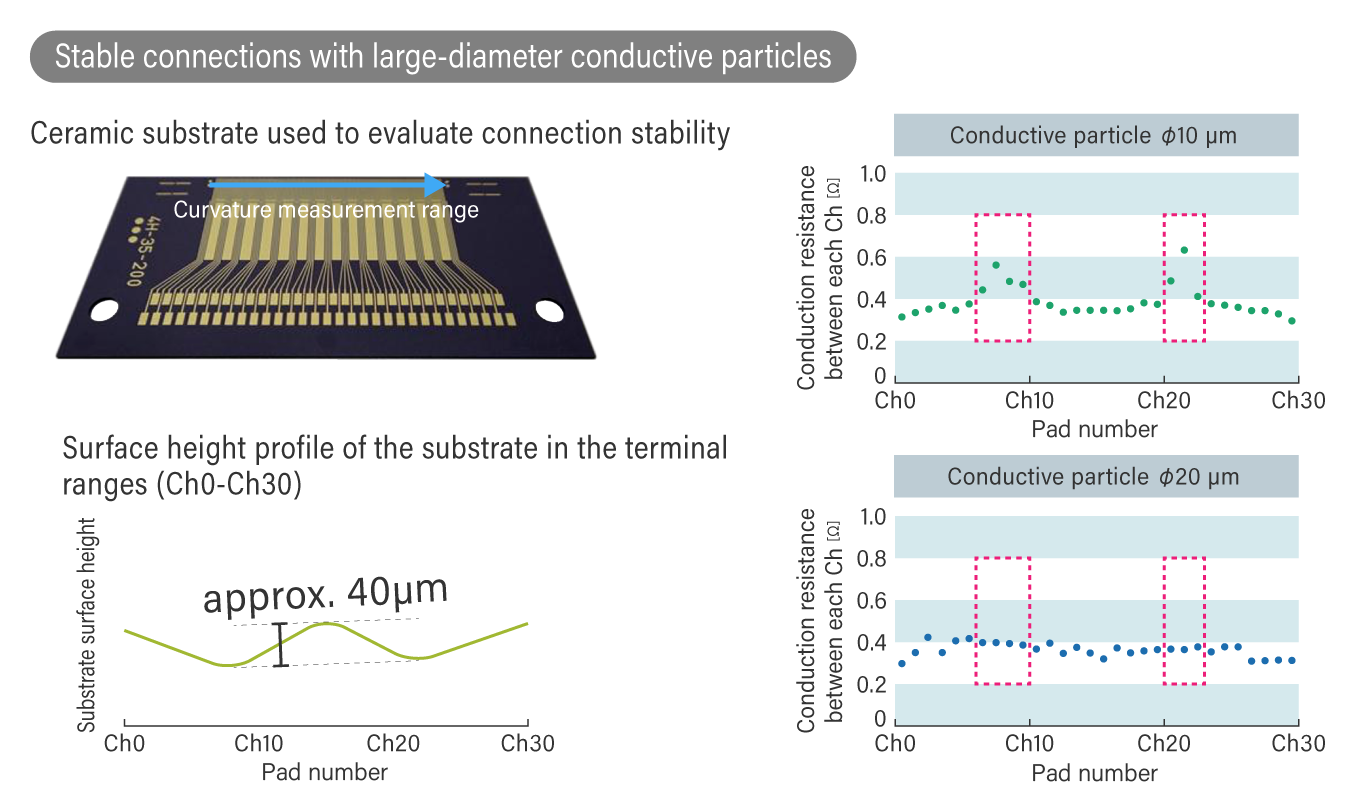
Advantages of bonding at low pressure
One major advantage of ACFs with large-diameter particles is that they can be bonded at low pressure. Camera performance is an indispensable aspect of smartphones. These cameras are made with great precision, and in the assembly of camera modules, ACFs must be able to bond at lower pressure to avoid applying unnecessary force to the camera body.
The larger the diameter of the particles, the less force is required to deform or collapse them, so that conduction can occur at lower pressure. Below are magnified images of conductive particles of 10 µm, 15 µm, and 20 µm when subjected to pressures 0.5 MPa to 2.0 MPa. It can be seen that the larger the diameter, the lower the pressure is required to deform the particles.
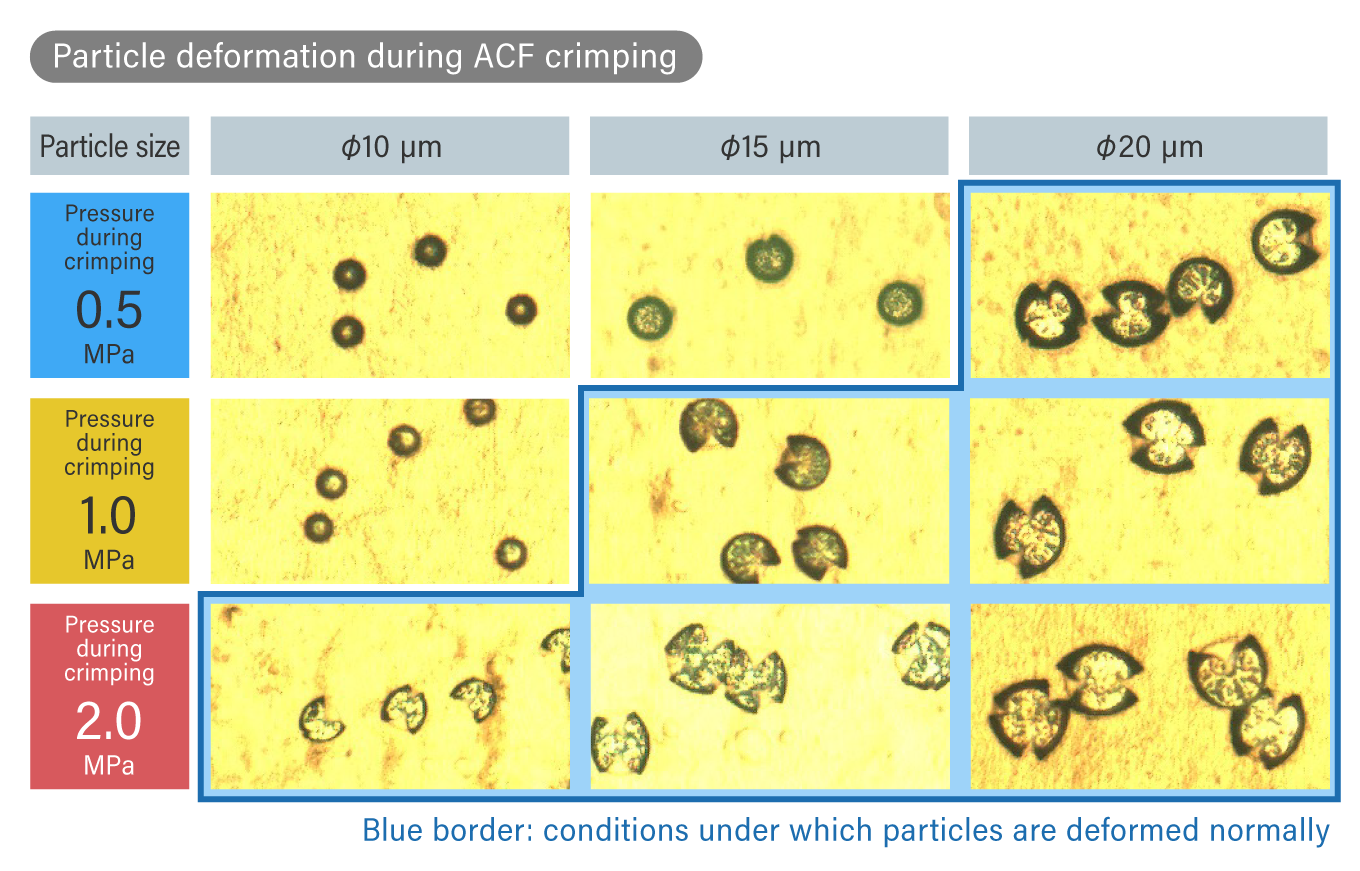
The above explains the features of ACFs with large-diameter conductive particles used in the assembly of camera modules. In recent years, cameras have been installed in a wide range of electronic products, including smartphones. The demand for automotive camera sensors is expected to grow dramatically in the future, which will further expand the application of ACFs used in camera modules.
- SHARE