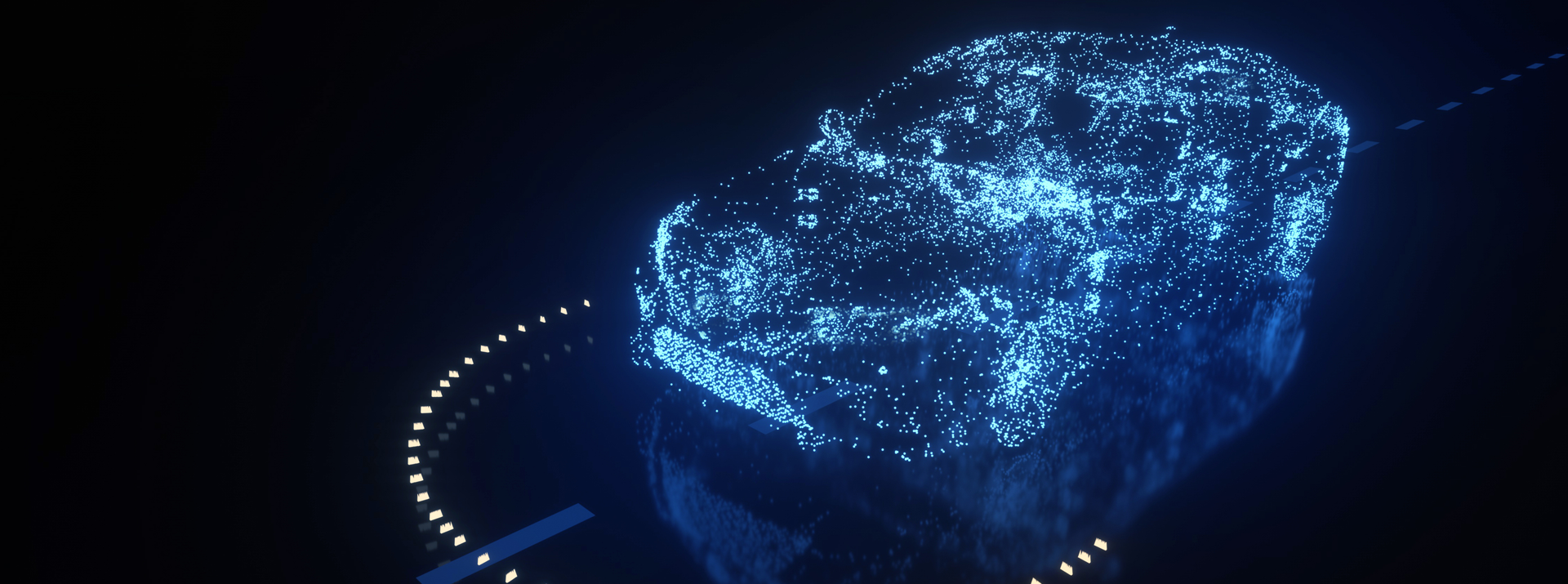
- Bonding Products
High-precision adhesives used in automotive camera sensors
Contents
The automotive camera sensors market to double by 2026
Modern vehicles are equipped with several camera sensors that allow the driver to be aware of the surroundings. Dexerials’ Smart-Precision Adhesives (SAs) are used to secure the components in these sensors. This article explores the technology behind it.
“The automotive camera sensors market has been growing rapidly worldwide in recent years, making it an important target for us”, states Motoyuki Nakane, General Manager of the Automotive Solutions Sales department at Dexerials Corporation.
What is the background behind the rapid expansion of the automotive camera sensors market?
“An increasing number of recently released vehicles are equipped with Level 1 and Level 2 Advanced Driver-Assistance Systems (ADAS), such as automatic braking, Automated Lane Keeping Systems (ALKS), and others. Automotive camera sensors are indispensable for ADAS, especially when the more advanced Level 3 or higher automatic driving functions are expected to expand in the future.”
“Most modern cars have cameras in the rear-view mirror, but an increasing number of cars also have cameras mounted on the front, rear, left and right sides of the car body. The demand for in-vehicle camera sensors continues to increase as ADAS is expected to more than double by 2026.”
Application of high-precision adhesive technology from smartphone cameras to automotive camera sensors
Automotive camera sensing technology used in automated vehicles requires high precision, which is achieved through the adhesive technology that Dexerials has refined in the smartphone market.
In what areas are Dexerials Smart-Precision Adhesives (SAs) used in automotive camera sensors?
“The illustration below shows areas marked with ◎ shapes. Dexerials’ SAs are used to bond and secure the substrate on which the CMOS image sensor is mounted and the housing where the lens is inserted to form the camera module.”
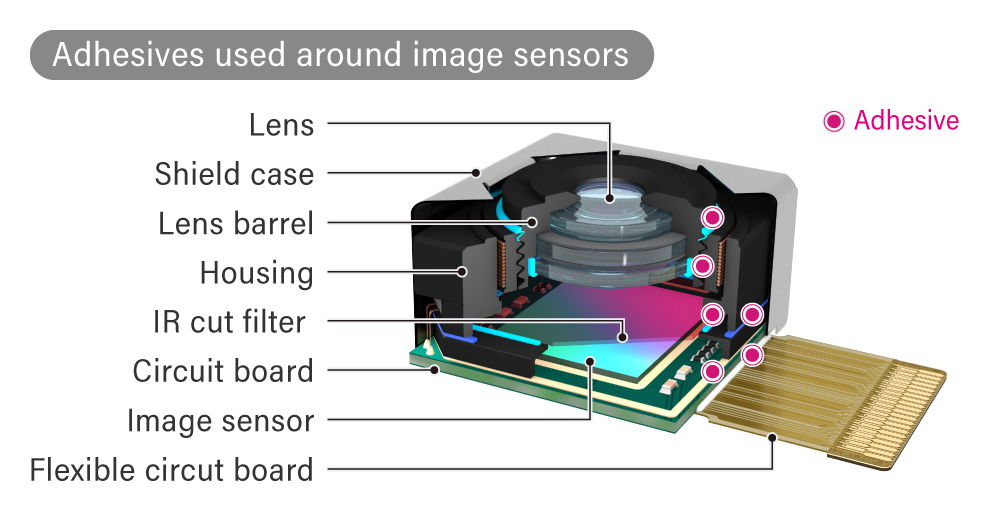
“The bonding of optical components that make up the camera requires accuracy in the µm scale (1/1000th of a millimeter). Even the slightest misalignment of the position or angle of bonding directly leads to blurring and image quality degradation. At the same time, it is important that the adhesive is easy to work with and it cures in a short amount of time at a low temperature to increase our customers’ production efficiency.”
“Since 2004, Dexerials has been refining its adhesive technology to fix components of flip phone cameras. Conventional cameras on mobile phones that time were held in place with screws. However, fixing components via screws became more difficult as cell phones became thinner and smaller, and as cameras became smaller and more sophisticated with the advent of smartphones. Hence, adhesives became more common to affix the components. Around 2015, more and more automotive cameras were used as sensors for safe driving. This required high-precision installation to maintain sensor accuracy, and the demand for Dexerials adhesive technology began to increase.”
Proposing optimal solutions for various adherends
In-vehicle sensing cameras enable safe driving. It also uses a range of adherends, including metals and plastics. Dexerials strives to provide the best solutions to meet the needs of its customers, which vary from project to project.
What are the differences in adhesives between automotive and smartphone cameras?
“The biggest difference is that cars have a much longer service life than smartphones, so the adhesives need to be durable over a longer period of time. In addition to not peeling off due to vibrations during driving, the product must be temperature and humidity resistant, especially in summer time. Adhesion is not just a matter of getting things affixed. If the hardened resin itself does not follow the expansion and contraction of the bonded adherends, it will peel off.”
“A technology called the ‘active alignment method’ is used for high-precision adhesion when assembling modules in automotive camera sensors. In this method, a CMOS image sensor is used to capture test patterns while aligning the optical axis and confirming that all areas of the image are blur-free before final adhesion.
“There are several different materials for automotive camera modules that are bonded using the active alignment method. Typical metals include aluminum, SUS, brass, and typical plastics – FR4, polyamide, PPS, and PBT. These various materials are bonded using adhesives, but it is not always a simple task as the ease of adhesion depends on whether the surface has been treated. The adherends and the needs of each customer differ greatly, and so we develop and propose the best solutions by repeatedly meeting with the client for each project.”
In the ever-growing automotive camera sensors market, what is the greatest advantage that Dexerials adhesives has to offer?
“What is most important is the abundant knowledge, technologies, and product lines we have cultivated over the years in the adhesives industry. Some adhesives have high bonding strength and cure with both heat and ultraviolet (UV) light, while others specialize in low moisture absorption or small shrinkage after curing. Rather than simply providing materials, our strength is our ability to use our knowledge to propose total solutions, including usage guidance, to meet various customer needs. We will continue to monitor the evolution of automotive camera sensors and trends, and provide products that bring even more value to our customers.”
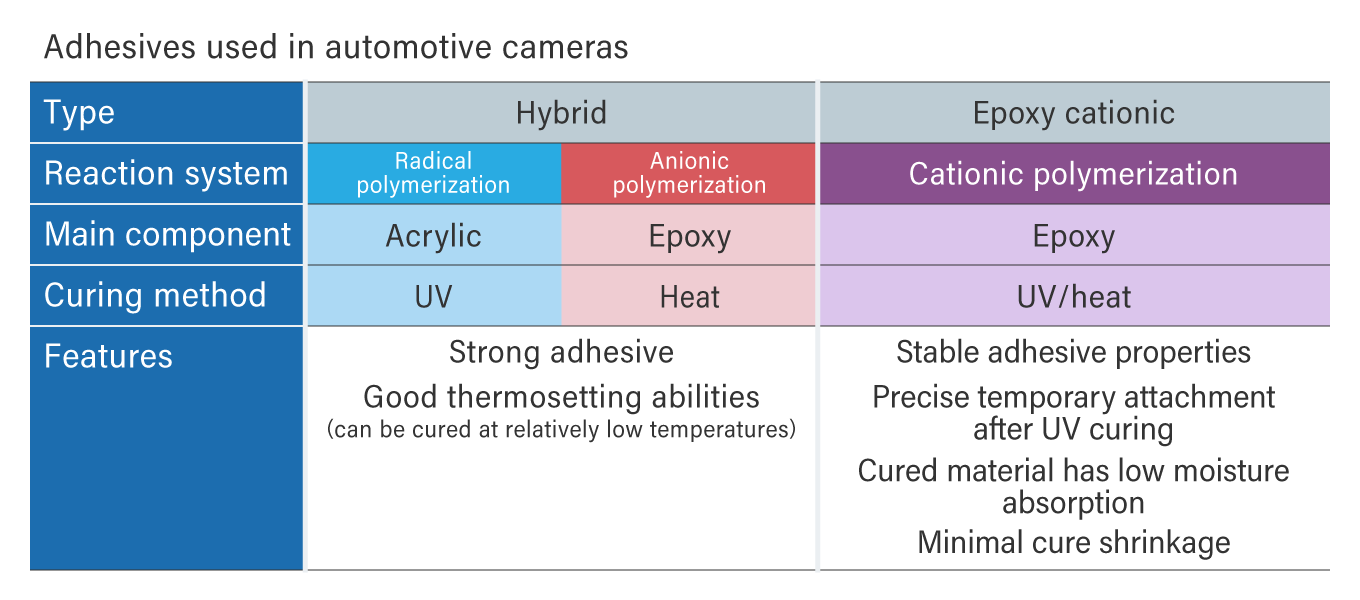
- SHARE